Состав для изготовления топливных брикетов. Состав топливных брикетов
Состав для изготовления топливных брикетов
Применение: технология брикетирования угля, углистых пород, отходов углеобогащения на горных и обогатительных предприятиях. Сущность изобретения: состав для изготовления топливных брикетов содержит, мас. % : белитовый шлам с содержанием оксида натрия 0,8 - 2,2 мас. % 15 - 25; фторгипсовый шлам глиноземного производства 5 - 15; вода 5 - 10; угольная мелочь до 100, что повышает прочность брикетов. 1 табл.
Изобретение относится к технологии брикетирования угля, отходов углеобогащения и может быть использовано на горно-обогатительных предприятиях.
Известна смесь для изготовления топливных брикетов, включающая угольную мелочь и связующее на основе нефтебитума и сульфидно-дрожжевой брошки, изготовление шихты на основе нефтебитума в количестве 20-70% от массы брикетов прессование (1). Недостатком смеси является высокая стоимость вяжущего и необходимость использования сложной технологии брикетирования. Наиболее близким аналогом по технической сущности и достигаемому результату является смесь, включающая угольную мелочь - 95-97 мас. % , неорганическое связующее на основе оксидов кальция и кремния - портланд-цемента 3-15 мас. % , неорганическую добавку - известняк 0,5-5 мас. % и воду (2). Недостатком данного способа является относительно высокая стоимость брикетов, за счет использования в качестве вяжущего портланд-цемента и известняка. Целью изобретения является снижение стоимости брикетов, за счет использования в качестве вяжущего отходов глииноземного производства. Это достигается тем, что в смеси используют белитовый шлам, с содержанием оксида натрия 0,8-2,2 мас. % , а в качестве активизирующей добавки фторгипсовый шлам, при следующем соотношении компонентов, мас. % : Беллитовый шлам 15-25 Фторгипсовый шлам 5-15 Вода 5-10 Угольная мелочь До 100 П р и м е р. Для приготовления смеси используются карьеры Канско-Ачинского буроугольного бассейна. В качестве связующего используется белитовый шлам, отход Ачинского глиноземного комбината, характеризующейся содержанием оксида натрия 0,8-2,2 мас. % . Химический состав белитового шлама, мас. % : ППП (потери при прокаливании) 4,5 SiO2 28; CaO 53, MgO 1,7; Fe2O3 5,0; Al2O3 5; Na2O3 2, K2O 0,8. В качестве дополнительной активизирующей добавки вяжущих свойств белитового шлама используется фторгипсовый шлам, также являющийся отходом Ачинского глиноземного комбината. Его химический состав, мас. % : СaSO4 2h3O 84; CaF3 14; потери при прокаливании 2. Угольная мелочь крупностью 0-25 мм, белитовый шлам, крупностью 0,05-2 мм, фторгипсовый шлам, крупностью 0,05-0,1 мм в соотношении, приведенном выше с водой затворения совместно перемешивается в шаровой мельнице в течении 30 мин, что соответствует суммарному содержанию класса 0,08 мм в составе не менее 50% на выходе из мельницы. Полученная смесь плотностью 1,7-2 г/см3 заливается в формы размеров 100х100х100 мм и просушивается при естественной температуре (18-20оС) в течении 28 сут, до остаточной влажности 3-5% . Образцы-кубики испытываются на механические свойства и исследуются их теплотехнические характеристики. Брикеты, полученные по вышеописанному способу используются в колосниковых печах, а также в качестве добавок при факельном сжигании углей. Брикеты характеризуются содержанием золы сухой до 30% . влажностью максимальной до 12% , рабочей теплотой сгорания до 2600 ккал/кг, содержанием углерода до 70% . Прочностные характеристики образцов приведены в таблице. Таким образом, отходы Ачинского глиноземного комбината и угольная мелочь КАТЭКа могут использоваться для получения топливных брикетов, что позволит решать проблемы утилизации шламов и использования отходов углеобогащения. (56) Авторское свидетельство СССР N 1452841, кл. С 10 L 5/16, 1989. Заявка Японии N 62-91506, кл. С 10 L 5/12, 1987.Формула изобретения
СОСТАВ ДЛЯ ИЗГОТОВЛЕНИЯ ТОПЛИВНЫХ БРИКЕТОВ, включающий угольную мелочь, связующее на основе оксидов кальция и кремния, неорганическую добавку и воду, отличающийся тем, что в качестве связующего на основе оксидов кальция и кремния он содержит белитовый шлам глиноземного производства с содержанием оксида натрия 0,8 - 2,2 мас. % и в качестве неорганической добавки - фторгипсовый шлам глиноземного производства при следующем соотношении компонентов, мас. % : Белитовый шлам с содержанием оксида натрия 0,8 - 2,2 мас. % 15 - 25 Фторгипсовый шлам глиноземного производства 5 - 15 Вода 5 - 10 Угольная мелочь До 100РИСУНКИ
Рисунок 1www.findpatent.ru
Состав для изготовления топливных брикетов
Использование: в топливной промышленности, на горно- обогатительных предприятиях. Сущность изобретения: состав для изготовления топливных брикетов содержит, мас.% : белитовый шлам 10-30, хлорид сульфат тиосульфат натрия - отход получения диафена азотного производства 0,3-1; вода 9,0-9,7, угольная мелочь остальное. 1 табл.
Изобретение относится к технологии брикетирования угля, отходов углеобогащения и может быть использовано на горно-обогатительных предприятиях.
Известна смесь для изготовления топливных брикетов, включающая угольную мелочь и связующее на основе нефтебитума и сульфидно-дрожжевой бражки, изготовление шихты на основе нефтебитума в количестве 2-70% от массы брикетов прессованием (А.с. СССР N 1452841, кл. С 10 L 5/16, 1989). Недостатком смеси является высокая стоимость вяжущего и необходимость использования сложной технологии брикетирования. Наиболее близким аналогом по технической сущности и достигаемому результату является смесь, включающая угольную мелочь 95-97%, неорганическое связующее на основе оксидов кальция и кремния, портландцемента - 3-15 мас.% , неорганическую добавку-известняк - 0,5-5 мас.% и воду. (Заявка Японии N 6291596, кл. С 10 L 5/12, 1987, реферат 9П54П), РЖ "Химия", 1988). Недостатком данного способа является относительно высокая стоимость брикетов за счет использования в качестве вяжущего портландцемента и известняка. Целью изобретения является снижение стоимости брикетов за счет использования в качестве связующего смеси на основе оксидов кальция и кремния - белитового шлама, отходов глиноземного производства с неорганической добавкой хлорид сульфат тиосульфат натрия - отходов получения диафена азотного производства. Это достигается тем, что в смеси используется белитовый шлам с активизирующей добавкой хлорид сульфат тиосульфат натрия, при следующем соотношении компонентов, мас.%: Белитовый шлам 10-30 Хлорид сульфат тиосуль- фат натрия 0,3-1 Вода 9,0-9,7 Угольная мелочь Остальное П р и м е р. Для приготовления смеси используются карьеры Канско-Ачинского буроугольного бассейна. В качестве связующего используется белитовый шлам, отходы Ачинского глиноземного комбината, характеризующегося содержанием оксида натрия 0,8-2,2 мас.%. Химический состав белитового шлама, мас.%: ппп - потери при прокаливании: SiО2 24-28; Al2О3 3-5; СаО 47-53; МgО 0,8-1,7; Na2О 0,8-2,2; потери при прокаливании 2-6%. Угольная мелочь, крупность 0-25 мм, белитовый шлам - крупность 0,05-2 мм, хлорид сульфат тиосульфат натрия - крупностью 0,05-0,1 мм в соотношении, приведенном выше, с водой затворения совместно перемешивается в шаровой мельнице в течение 15 мин, что соответствует суммарному содержанию класса 0,08 мм в составе не менее 60% на выходе из мельницы. Полученная смесь плотностью 1,6-1,9 г/см3 заливается в формы размером 100х100х100 и просушивается при естественной температуре (18-20оС) в течение 20-25 сут до остаточной влажности 3-5% . Образцы кубики испытываются на механические свойства и исследуются их теплотехнические характеристики. Брикеты, полученные по описанному способу, используются в колосниковых печах, а также в качестве добавок при факельном сжигании углей. Брикеты характеризуются содержанием золы сухой до 32%, влажностью максимальной до 12% , рабочей теплотой сгорания до 2700 ккал/кг, содержанием углерода до 70%. Прочностные характеристики образцов приведены в таблице. Таким образом, отходы получения диафена азотного производства (г. Кемерово), отходы получения глинозема (г.Ачинск) и угольная мелочь КАТЭКа могут использоваться для получения топливных брикетов, что позволяет решать проблемы утилизации шламов и использования отходов углеобогащения.Формула изобретения
СОСТАВ ДЛЯ ИЗГОТОВЛЕНИЯ ТОПЛИВНЫХ БРИКЕТОВ, включающий угольную мелочь, связующее на основе оксидов кальция и кремния, неорганическую добавку и воду, отличающийся тем, что в качестве связующего на основе оксидов кальция и кремния он содержит белитовый шлам глиноземного производства и в качестве неорганической добавки - хлорид сульфат тиосульфат натрия - отход получения диафена азотного производства при следующем соотношении компонентов, мас.%: Белитовый шлам глиноземного производства - 10 - 30 Хлорид сульфат тиосульфат натрия - 0,3 - 1,0 Вода - 9,0 - 9,7 Угольная мелочь - ОстальноеРИСУНКИ
Рисунок 1, Рисунок 2www.findpatent.ru
Производство топливных брикетов Технология, виды брикетов, использование
Топливными брикетами называют отходы деревообработки, продуктов переработки сельскохозяйственной деятельности, торфяных продуктов, подготовленными в специальные сжатые формы, имеющие вид брикетов для дальнейшего их применения как топливный материал. Производство топливных брикетов регионально распространено на территории России, а изделия вполне доступны гражданам.
Составляющие компоненты отходов из древесных материалов:
Отходы от деятельности сельского хозяйства:
- Злаковая шелуха;
- Кукурузные отходы;
- Помельченная солома;
- Уголь древесный;
- Торфяные продукты;
- Отходы подсолнуха.
Особенности использования брикетов в качестве топлива
Главное назначение спрессованных отходов - использование в качестве альтернативы жидким горючим материалам, включая другие твердые, для различных каминных сооружений, печей, котлов отопительных систем. Высокие показатели экологичности, возможность гореть, не выделяя много дыма, являются преимущественной особенностью топливных брикетов. Таким продуктом можно отапливать дома, палатки, бани, тепличные конструкции. Безвредность такого вида отапливания жилых зданий не принесет вреда для человека. Небольшие размеры, удобная форма позволяет легко перевозить, выгружать и загружать этот вид топливного материала. Свою популярность благодаря удобству использования, безопасности, экологичности топливные брикеты обрели во многих странах мира.
Типы опрессованных изделий
Выпуск топливных брикетов осуществляется в трех композициях:
1. Прямоугольные. По своей форме напоминает кирпич средних размеров. Производится путем давления гидравлического пресса до 400 бар.2. Цилиндрические. Цилиндр выпускается с радиальным отверстием и без. Производится под влиянием давления гидравлического (ударно-механического) прессов до 600 бар.3. Пини-кей. Брикеты с четырьмя или шестью гранями с радиальным отверстием. Их изготовление происходит под давлением шнекового пресса порядка 1100 бар и под термическим воздействием. По итогам термической обработки пини-кей - брикеты обретают черный или насыщенный коричневый цвет. Они обладают высокой устойчивостью к влажности, механическим влияниям, долговременности в процессе горения, высокой калорийностью.
Какой бы вид не имели топливные брикеты, это не влияет на их назначение. Стандартов и специальной технологии для производства этого вида топлива не существует. Достаточно индивидуальной рецептуры для использования тех или иных составляющих в исходном сырье, дальнейшая их обработка.
Технология производства топливных спрессованных брикетов
Основу всего процесса составляет воздействие пресса под давлением, иногда с применением термической обработки до 3500 °C, на отходы сельскохозяйственного производства, измельченных отходов деревообработки. Базовым соединительным компонентом в топливных брикетах считается лигнин. Это вещество имеет высокую концентрацию в отходах растительного происхождения.
При масштабном производстве топливных брикетов из сельскохозяйственных отходов, использование их в качестве соединительных компонентов весьма обоснованно. Высокие температуры при спрессовывании сырья в брикеты помогают оплавлять поверхность готовой продукции, обеспечивая ей необходимую прочность для удобства дальнейшей транспортировки. Соблюдение пропорций компонентов, контроль за показаниями влажности и плотности делают готовое изделие высокого качества функциональным и конкурентноспособным на рынке. Производство топливных брикетов даже из простых опилок доступно рядовому предпринимателю, не требует больших расходов.
Изготовление топливных брикетов намного легче технологически, чем производство тех же гранул.
Критерии прочности брикетов
Определяющим фактором в калорийности, стойкости к влаге и механическим воздействиям является показатель плотности. Качество брикета, его калорийность напрямую зависят от того, какую плотность он имеет.
Для примера: Если плотность брикета достигает 770 кг/см³, то его калорийность составит до 15 МДж/кг. Если плотность готового продукта определяется в 1400 кг/м³, то показатель калорийности соответствует 32 МДж/кг.
Уровень влаги в изначальном сырье тоже считается определяющим показателем в прочности будущего изделия. Их разделяют на оптимальные (допустимо до 10%) и критические (10-17%) нормы. Высокие механические качества топливных брикетов могут проявиться лишь при таких значениях.
Критический показатель содержания влаги в сырье способствует появлению в готовой продукции трещин, расколов, поверхность обретает нетоварный вид. Показатель от 10 до 17% определяется, исходя из верхнего предела нормы содержания влаги в отдельных видах исходного материала в 8%. Если у сырьевого материала для производства топливных брикетов влажность превышает порог в 15%, то их изготовление будет бессмысленным процессом.
Это обусловлено тем, что влага, возникающая от прессования измельченной сырьевой массы попросту разорвет готовое изделие под давлением изнутри. Если соблюдать все необходимые нормы, чтобы организовать производство брикетов, цена на них будет обоснованной, а бизнес рентабельным.
Виды топливных брикетов
Брикеты разделяют по двум направлениям:
1. По типу сырья, используемому в качестве исходного материала в готовом изделии (продукты отходов сельскохозяйственной деятельности, измельченная стружка и щепа, опилки без коры, лигнин, фанера, шлифовочная пыль, МДФ обрезки, измельченная шелуха, хлопковые отходы, сухой камыш и другие).
2. По методам опрессования и создания формы:
- Форма кирпича;
- Вид цилиндра;
- Экструдерные брикеты.
Оборудование для производства брикетов может быть различным. Именно механизмы и агрегаты обеспечивают выпуск заданной формы по итогам изготовления.
Топливный материал с формой кирпича
Изготавливается способом опрессовывания под воздействием гидравлического пресса и высокого давления. Изделия имеют вид параллелепипеда прямоугольной формы со скошенными уголками. Такой вид топлива имеет огромный спрос среди потребителей Белоруссии, Азербайджана, Узбекистана, Казахстана и в государствах Евросоюза. Доступность и практичность топливного материала определяет такую популярность у потребителей всего мира.
Брикеты, имеющие форму цилиндра
Технология изготовления заключается в воздействии ударно-механического пресса на исходный материал. На выходе получается готовая продукция с длинным стволом, что позволяет затем ее разрезать специальным инструментом на поленья или круги в форме шайбы. Получившаяся форма зависит от пожеланий заказчика и оборудования, которым располагает исполнитель. Также, наличие необходимого оборудования может осуществить практически любое нужное формирование брикета.
Готовому изделию можно придать вид круга, квадрата или восьмиугольника, брикет может подразумевать наличие или отсутствие радиальное отверстия. Страны Евросоюза предпочитают именно этот вид топливных брикетов. Получил максимальное признание и распространение. На российском рынке топливного сырья представлены, зачастую, кусковые изделия, которые предназначаются для использования в твердотопливных котлах.
Экструдерные топливные брикеты
Процесс изготовления осуществляется путем опрессовывании исходного материала шнеком под воздействием высокого давления и нагреванием сырья до 3500 °C. Высокая температура позволяет оплавлять поверхность изделия, чтобы повысить его прочность и упростить дальнейшее перемещение. Экструдерные брикеты обязательно имеют радиальное отверстие и обожженный верх. Закладка в печную топку или котел исходного сырья осуществляется вручную. Топливные экструдерные брикеты признаны странами Прибалтики и городами Российской Федерации.
incomeeasily.ru
Связующее для топливных брикетов
Изобретение относится к связующим, используемым для брикетирования угольных шахт, и может найти применение в производстве топливных брикетов, пригодных для сжигания в промышленных котельных и бытовых печах. Описывается связующее для топливных брикетов, содержащее мелассу, согласно изобретению дополнительно введены минеральный наполнитель и ортофосфорная кислота при следующем соотношении компонентов, мас.%: минеральный наполнитель - 30-55, ортофосфорная кислота - 15-25, меласса - остальное. Предложенное связующее позволяет формовать брикеты, обладающие необходимой прочностью и влагостойкостью. Кроме того, это связующее относится к числу тех, которые не увеличивают выделение канцерогенных веществ при сгорании и не увеличивают стоимость топливных брикетов. 1 з.п. ф-лы, 4 табл.
Изобретение относится к связующим, используемым для брикетирования угольных шихт, и может найти применение в производстве топливных брикетов, пригодных для сжигания в промышленных котельных и бытовых печах.
Основными причинами, связывающими развитие брикетирования каменных и старых бурых углей, являются отсутствие недефицитного и безвредного связующего, относительно высокая стоимость переработки угля в брикеты из-за высокой стоимости связующего и образование большого количества копоти при горении брикетов, что ограничивает их применение в бытовых условиях. Известно, что связующее вещество для брикетирования должно удовлетворять ряду существенных требований: обладать хорошей связующей способностью и придавать брикетам достаточную прочность при их небольшом расходе; иметь хорошие спекающие свойства и придавать брикетам необходимую термическую устойчивость при горении; быть устойчивым к влаге; быстро затвердевать и придавать брикетам устойчивость в летнее время года; быть безвредным как при производстве брикетов, так и при их употреблении; быть недорогим и не усложнять процесс брикетирования; не увеличивать содержание балласта в топливе и не понижать его теплоту сгорания; быть недефицитным и применяться при малом расходе [1] (Крохин В.Н. "Брикетирование углей".- М.: Недра, 1984, 224 с.). Подобрать связующее, полностью отвечающее перечисленным требованиям, - трудная задача. В литературе известно много попыток использования для брикетирования углей различных материалов, но они не получили постоянного применения, так как не отвечают полностью перечисленным требованиям. Наибольшее применение для брикетирования мелочи каменных углей нашли каменноугольный пек и нефтебитумы. Известно связующее для угольных брикетов, содержащее каменноугольный пек и углеводородную фракцию с точкой кипения 220 - 450oC, которое в качестве каменноугольного пека содержит пек с точкой размягчения 120 - 200oC при следующем содержании компонентов, вес.%: Каменноугольный пек с точкой размягчения 120 - 200oC - 35 - 77 Углеводородная фракция с точкой кипения 220 - 450oC - 23 - 65 Брикеты, изготовленные с использованием описанного выше связующего, обладают высокой прочностью на сжатие и разрыв, однако использование такого связующего потребует значительных энергетических затрат для размягчения связующего, кроме того, при сжигании брикетов, содержащих каменноугольный пек, выделяются и канцергенные вещества, что ограничивает использование таких брикетов в бытовых котельных [2] (РФ N 988196, С 10 L 5/14). Известно также связующе, содержащее белитовый шлам глиноземного производства, хлорид сульфат тиосульфат натрия при следующем соотношении компонентов, мас.%: Белитовый шлам глиноземного производства - 25 - 75 Хлорид сульфат тиосульфат натрия - 0,7 - 2,5 Вода - Oстальное Для получения брикетов удовлетворительного качества используют такое связующее в количестве 20 - 40%, угольная мелочь - остальное. Технология приготовления брикетов с таким связующим сравнительно простая, так как брикеты сушат и формуют на воздухе, однако брикеты характеризуются высокой зольностью (содержание золы сухой до 32%) и низкой теплотой сгорания (до 2700 ккал/кг) [3] (РФ 2030448, C 10 L 5/48). Наиболее близким к заявляемому решению по назначению, технической сущности и достигаемому результату при использовании является связующее из отходов сахарной промышленности, например мелассы, которую предварительно превращают в гидромассу и затем смешивают с угольной мелочью. Мелассу в связующем берут в количестве 10 - 50%, а по отношению к угольной мелочи связующее составляет 10 - 30% [4] (a.c. СССР N 1778160, C 10 L 5/44). Как видно из описания связующего, приведенного выше, оно позволяет сформовать брикеты, отрицательное действие на окружающую среду при сжигании которых будет минимальным. Технология формования брикетов на таком связующем также не требует значительных энергетических затрат, поскольку весь процесс формования и сушки осуществляют в основном на воздухе. Брикеты обладают низкой зольностью, не более 9,9%, и высокой теплотворной способностью - 6500 - 7110 ккал/кг. Однако они обладают значительной пористостью - 40 - 50% и низкой объемной массой - 0,82 - 0,90 г/см3. Их отличает низкая прочность и значительная способность к влагопоглощению. Такие брикеты практически не пригодны к транспортировке на значительные расстояния и к длительному хранению. Кроме того, значительное содержание отходов сахарной промышленности в составе связующего может привести к удорожанию брикетов, несмотря на низкие энергетические затраты на их изготовление. Поэтому целью предлагаемого технического решения является разработка связующего, которое позволило бы формовать брикеты, обладающие необходимой прочностью и влагостойкостью. Поставленная цель достигается тем, что в известное связующее для топливных брикетов, содержащее мелассу, согласно изобретению дополнительно введены минеральный наполнитель и ортофосфорная кислота при следующем соотношении компонентов, мас.%: Mинеральный наполнитель - 30 - 55 Oртофосфорная кислота - 15 - 25 Mеласса - Oстальное В качестве инертного наполнителя может быть использована или глина, или угольный шлам, или зола уноса тепловых электростанций. Указанное содержание минерального наполнителя и ортофосфорной кислоты является оптимальным, так как их смешивание приводит к образованию нерастворимых фосфатов, что способствует повышению влагостойкости брикетов. Повышение содержания ортофосфорной кислоты нецелесообразно, так как это может привести к удорожанию конечного продукта. Увеличение содержания минерального наполнителя и снижение содержания мелассы также нецелесообразны, так как это может привести к недостаточной адсорбции связующего с брикетируемым материалом и, следовательно, к снижению прочности брикетов. Увеличение содержания мелассы может привести при невысокой температуре термической обработки брикетов к снижению влагостойкости, а также может быть экономически невыгодным. Как видно из изложения сущности заявляемого решения, оно отличается от прототипа и, следовательно, является новым. Решение также обладает изобретательским уровнем. В основу изобретения поставлена задача усовершенствования связующего для топливных брикетов, в котором, вследствие протекания реакции образования сахаратов и смешанных солей (фосфат + сахарат) с образованием зачатков пространственной структуры и дополнительных связок в виде полифосфатов (в основном пирофосфатов) обеспечивается образование на поверхности частиц тонкой пленки связующего, обеспечивающего эффективную адгезию и спекание при минимальной усадке, и за счет этого получают топливные брикеты, обладающие необходимой прочностью и влагостойкостью. В данном случае такие компоненты, как глина, угольный шлам или зола уноса тепловых электростанций, выполняют роль не только наполнителей, уменьшающих усадку, но они способствуют склеиванию и спеканию, образованию достаточно прочного каркаса, обеспечивающего влагостойкость и термическую стойкость при горении. Известно использование мелассы в качестве связующего [4]. Однако, как показано выше, гидромасса с использованием мелассы не обеспечивает необходимой прочности и влагостойкости брикетов. Известно также использование в качестве связующего мела, глины и тому подобных веществ, подготовленных в виде водной суспензии с добавлением в некоторых случаях коллоидного вещества [5, 6] (a.c. СССР N 54977, 10 B 2, 02.11.39; WO 87/00855, C 10 L 5/12). Однако брикеты, сформованные на основе таких связующих, не обладают необходимой влагостойкостью. Для того чтобы глина приобрела влагостойкость, необходимо брикеты спекать при температуре порядка 700oC, что существенно усложняет технологию брикетирования. Предлагаемое связующее не требует высокой температуры для обработки брикетов. Образование полностью замещенных фосфатов в результате взаимодействия ортофосфорной кислоты с наполнителями обеспечивает влагостойкость, а полимеризация мелассы в сочетании с продуктами реакции ортофосфорной кислоты и минеральных наполнителей после термической обработки брикетов обеспечивает их необходимую прочность. Предлагаемое связующее может найти широкое применение при производстве топливных брикетов для промышленных и бытовых котельных. Подготовку связующего для использования осуществляют следующим образом. К глине (угольному шламу или золе уноса тепловых электростанций), измельченной до фракций 3-0 мм, и влажностью до 20% добавляют ортофосфорную кислоту и тщательно перемешивают не менее 30 мин. Полученную массу перегружают в другой реактор и добавляют мелассу (отход сахарной промышленности) с содержанием сухих веществ до 80%, в том числе - сахарозы до 48%, и также тщательно перемешивают не менее 30 мин. Подготовленное таким образом связующее сливают в расходную емкость. В холодное время года мелассу следует нагреть до 30-50oC. Используют подготовленное таким образом связующее в технологическом процессе брикетирования, который включает смешивание связующего с угольной шихтой, прессование сырья на валковом прессе при давлении 50 МПа. При этом связующее в подготовленном для брикетирования сырье составляет 9 - 11 мас.%. Сырые брикеты после отсева брикетной мелочи подвергают тепловой обработке. После этого топливные брикеты охлаждают и направляют на склад. Влажность брикетов, прошедших тепловую обработку, составляет 2-5%, а температура охлажденных брикетов не более 40oC. Качество брикетов оценивали по прочности на сжатие (ГОСТ 21289 - 75) и влагопоглощению (ГОСТ 21290 - 75), характеризующему влагостойкость. Вяжущие и спекающие свойства связующего находятся в непосредственной зависимости от соотношения составляющих его компонентов. Результаты исследования влияния состава связующего на прочность и влагостойкость брикетов, полученных с использованием этого связующего, приведены в табл. 1, 2, 3, 4. Пример 1. Состав связующего, мас.%: глина 33 - 55%, ортофосфорная кислота 8 - 22%, меласса - остальное. Угольная шихта - антрацитовая мелочь. Пример 2. Состав связующего, мас.%: глина 30 - 60%, ортофосфорная кислота 5 - 25%, меласса - остальное. Угольная шихта - антрацитовая мелочь. Пример 3. Состав связующего, мас.%: угольный шлам (зола уноса тепловых электростанций) 55 - 70%, ортофосфорная кислота 5 - 15%, меласса - остальное. Угольная шихта - антрацитовая мелочь. Пример 4. Состав связующего, мас.%: угольный шлам (зола уноса тепловых электростанций) 50 - 80%, ортофосфорная кислота 3 - 17%, меласса - остальное. Угольная шихта - антрацитовая мелочь. Как видно из результатов исследования влияния составляющих на основные эксплуатационные характеристики топливных брикетов, предложенное связующее позволит формовать брикеты, обладающие необходимой прочностью и влагостойкостью. Кроме того, это связующее относится к числу тех, которые на увеличивают выделение канцерогенных веществ при сгорании и не увеличивают стоимость топливных брикетов.Формула изобретения
1. Связующее для топливных брикетов, содержащее мелассу, отличающееся тем, что в него дополнительно введены минеральный наполнитель и ортофосфорная кислота при следующем соотношении компонентов, мас.%: Минеральный наполнитель - 30 - 55 Ортофосфорная кислота - 15 - 25 Меласса - Остальное 2. Связующее по п.1, отличающееся тем, что в качестве минерального наполнителя использована или глина, или угольный шлам, или зола уноса тепловых электростанций.РИСУНКИ
Рисунок 1, Рисунок 2, Рисунок 3www.findpatent.ru
Технология производства брикетов из опилок своими руками
На деревообрабатывающих предприятиях всегда есть отходы – это опилки и тырса. Часто их просто вывозят на свалку. Многие частные предприниматели налаживаются производство брикетов для своих нужд, чем экономят на отоплении. Скажем сразу, что качественные евродрова можно получить только на специальном оборудовании. Есть и ручные прессы, на которых делают брикеты из опилок своими руками. Видео такого производства легко можно найти в сети. Посмотрев их, возникают серьезные сомнения в целесообразности самостоятельного изготовления низкокачественных евродров. Добиться высокого качества на ручных прессах просто невозможно априори.
Технология производства брикетов из опилок
Конвейер брикетирования опилок.
Производство брикетов состоит всего из двух процессов – это дробление и прессование. Главное – это хороший, мощный пресс, а он очень дорогой. Если пресс выдает недостаточно высокое давление, то добавляется еще один производственный цикл – это сушка. Если делать топливные брикеты из опилок своими руками сушка будет самым долгим процессом. Также читают: «Производство пеллет».
Тырса для брикетов должна быть мелкой фракции, чем меньше, тем лучше. Такое сырье получается при распиловке леса. На производство же поступают в основном опилки, которые остаются при обработке дерева. Опилки подают в контейнер дробильной машины и измельчают. После этого сырье пропускают через пресс.
В прессе происходит нагрев и создается огромное давление, под воздействием которого выделяется естественное связующее вещество – лигнин.
В домашних условиях такого достичь невозможно, поэтому в качестве связующего вещества можно использовать:
- глину;
- клеящие составы;
- размоченный картон.
Использовать клей для изготовления топливных брикетов из опилок своими руками нерентабельно, поэтому этот вариант отметаем сразу. В топке будет оставаться много золы, если в качестве связующего вещества будет глина. Она ведь не горит, а ее содержание составляет 10% от общей массы. То есть после сожжённых 100 кг брикетов в топке останется 10 кг глины – это без учета пепла от опилок.
Картон горит, выделяя тепловую энергию, от него остается мало пепла. Брикеты, где в качестве связующего вещества выступает размоченный картон, удобнее в эксплуатации. При этом время сушки увеличивается, соответственно, либо вы сможете сделать меньше брикетов, либо придется найти место, где можно будет разместить больше кирпичиков.
Чтобы краска легла ровным слоем нужно сначала нанести грунтовку для труб отопления. Работы проводятся когда контур холодный.
О том, как рассчитать трубы для отопления читайте здесь.
Как сделать брикеты своими руками
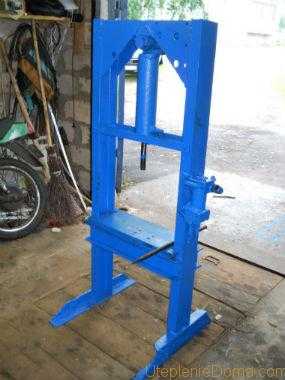
Пресс из домкрата.
Чтобы сделать брикет из опилок потребуется пресс. Можно купить готовый гидравлический пресс, к которому еще нужно докупить компрессор. Производство на таком оборудовании быстрее и проще, но аппарат потребляет очень много электроэнергии, так как в нем есть сушка. Потребление зависит от модели, диапазон от 5 до 35 кВт. Также есть и ручные прессы, где давление создается через рычаг или за счет накручивания. В первом случае не удастся нормально отжать брикеты от влаги. Во втором случае процесс занимает много времени.
Оптимальный вариант – использовать в качестве пресса автомобильный гидравлический домкрат. Их грузоподъёмность бывает разной, минимум 2 тонны. Нужно подготовить прочную металлическую рамку, к верхней балке корой крепится домкрат (вверх ногами). То есть усилие домкрата будет направлено вниз, где находится форма, заполненная сырьем.
Алгоритм изготовления топливных брикетов своими руками:
- замочить измельченный картон;
- смешать мокрый картон с опилками – пропорция 1:10;
- поместить массу в пресс и отжать от влаги;
- вынуть брикеты из форм и высушить
Своими глазами увидеть, как делают топливные брикеты своими руками можно на видео ниже:
Мешать опилки можно бетономешалкой или миксером. Сушить уже готовые брикеты можно на солнце или на печи. Влажность топлива должна быть минимальной. Например, в заводских брикетах влажность 8-10%. В домашних условиях хотя бы достигнуть уровня обычных дров 18-25%. Большинство твердотопливных котлов и пиролизных печей работает на топливе, влажность которых не более 30%. Чем меньше влаги в топливе, тем меньше пойдет тепловой энергии на ее выпаривание. Соответственно, сухой энергоноситель отдаст больше тепловой энергии, на обогрев помещения.
Когда есть смысл производить топливные брикеты
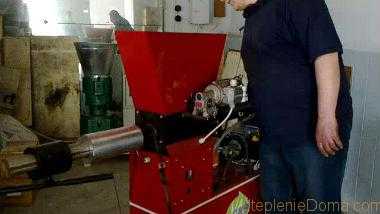
Мини-станок, который делает брикеты.
Делать топливные брикеты своими руками, как указано на видео выше, выгодно только тогда, когда у вас есть бесплатные опилки. Но даже при этом не всегда есть целесообразность этого мероприятия. К примеру, у вас свое деревообрабатывающее производство, которое нужно отопить. Просто опилки бросать в печку неудобно, да и не горят они нормально. В этом случае есть смысл купить станок и штамповать на нем брикеты для своих нужд. Качество изделий будет приемлемым, и вы сэкономите на отоплении. Вручную делать брикеты в этом случае слишком хлопотно, так как энергоносителя нужно много.
Современные пропиленовые трубы для отопления по отзывам сегодня самые популярные для сборки контура.
Сделать разводку труб системы отопления своими руками несложно. Поэтапная инструкция тут.
Для отопления частного дома самодельные брикеты тоже не лучший вариант и вот почему:
- низкое качество из-за использования самодельных прессов;
- на производство нужно много времени и сил.
Это, если не учитывать того, что пресс тоже надо изготовить самостоятельно. К тому же брикеты могут и не получиться. Неприятный сюрприз может ждать после сушки – кирпичики бывает просто распадаются. Смысл самостоятельного производства есть тогда, когда вы хотите сделать несколько кубов брикетов, чтобы иногда отапливать дачу. Но опять же, если есть свои опилки и вы готовы потратить на это несколько дней.
utepleniedoma.com
Использование и применение топливных брикетов из опилок
На дворе 21 век. Эпоха, когда человечество семимильными шагами начало развивать альтернативные источники энергии. И если о солнечной энергии или ветряных электростанциях слышали многие, то информация о топливных брикетах для большинства станет открытием.
Брикеты могут иметь цилиндрическую или прямоугольную форму. Их вес начинается от 500 грамм и может доходить до 2 килограмм. Пеллеты могут подаваться автоматически в топку котла, брикеты же подаются вручную. Сейчас началось развитие технологии производства коротких брикетов. Их длина составляет считанные сантиметры и это позволило полностью автоматизировать подачу топлива. Основное сырье для производства — это измельченные сухие отходы деревообрабатывающей промышленности, стружка и опилки. Изготавливаются брикеты методом прессования под высоким давлением и температурой. Топливные брикеты являются полностью экологически чистым продуктом.
Отопление брикетами
Можно ли топливными брикетами отапливать дом? Подходят ли они для поддержания температуры дома в холодное время? Выгодно ли это? Единственным ответом на эти вопросы будет — да. Брикеты производятся только из сухого сырья, поэтому влажность брикета не превышает 8%, в то время как влажность сухих дров колеблется в районе 50%. А это значит, что дрова львиную долю тепловой энергии тратят не на обогрев дома, а на выпаривание влаги. Это значит, что брикеты нагреют ваш дом гораздо быстрее дров.
Топливные брикеты — это твердые, плотные кирпичи, крепко спрессованные на специальном прессе. В отличие от дров брикеты не содержат пустот с воздухом, за счет своей плотности время их горения в 2–3 раза выше, чем время горения дров. Для обогрева дома нужно меньшее количество брикетов, нет необходимости постоянно находиться у котла и подбрасывать новые порции топлива. Теплотворность брикетов порядка 4200–4500 ккал/кг, а это больше чем, у дров и бурового угля. Топливные брикеты подходят для всех типов каминов, печей и котлов отопления, поэтому являются идеальным топливом для отопления дома. Брикеты удобно фасуют, в пачки по 10 килограмм, поэтому их легко разгружать, переносить и складывать вручную.
Про топку печей
Топливные брикеты подходят для топки любых печей. Теплотворность брикетов, которая составляет 4200 ккал/кг, позволяет протопить печи значительно быстрее. Не содержащие смол брикеты, защищают дымоход и газоводы от появления копоти. У брикетов очень низкая зольность — всего 0,5–1%. После сгорания брикетов остается немножко пепла, а не углей. Топка печи практически не захламляется, интервал обслуживания и чистки увеличивается в несколько раз. При сгорании брикеты выделяют угарного газа в 50 раз меньше угля и в 10 раз меньше природного газа. Растопить брикеты легче легкого, например, с помощью бумаги, веточек или жидкости для розжига.
Для твердотопливных котлов
Сложно найти более экономичное, эффективное, безопасное и подходящее средство. Что главное для твердотопливного котла?
- Высокая теплотворность топлива.
- Минимальное наличие загрязняющих веществ при горении.
- Подходящий размер для котла.
- Малое количество углей и золы.
Трудно поверить, но теплотворность топливных брикетов выше, чем у дров и бурового угля. Отметка в 4400 ккал/кг достигается минимальным наличием влаги (8%) и отсутствием пустот с воздухом в структуре брикета. Брикет горит в 3 раза дольше обычных сухих дров. Если дрова большую часть тепловой энергии отдают на выпаривание влаги, так как их влажность составляет 40%, то брикеты с первых минут отдают всю тепловую энергию на обогрев.
Да, теплотворность черного угля немного выше, чем у топливных брикетов. Однако КПД котлов при использовании брикетов на 5,28% выше и достигает отметки в 51,83%. Расход условного топлива на 1 Гкал выработанного тепла: каменный уголь − 306,9 кг у.т./Гкал, топливные брикеты − 276,1 кг у.т./Гкал.
Топливные брикеты не содержат химических добавок, являясь полностью экологически чистым продуктом. Они выделяют в 10 раз меньше угарного газа, чем природный газ. Также они практически не содержат смол, которые сильно забивают дымоходы и газоводы теплового оборудования. Например, котлы КВ-Р-1 имеют колосниковую решетку, которая забивается при работе на угле на естественной тяге. В отличие от угля топливные брикеты не допускают разрушения своей формы и оставляют минимум пепла, за счет этого решетка не забивается и котел получает достаточное количество воздуха. Что это значит? Значит, что котел не запускает дополнительные воздушные насосы на электротяге, экономится много электроэнергии, а в итоге и семейный бюджет.
Топливные брикеты характеризует устойчивое и равномерное горение в топке котла. Брикеты не выделяют едкого дыма, не дают сильного пламени и не стреляют. Пламя ярко-желтого цвета, которое не выходит за пределы котловой зоны. После сгорания брикеты оставляют минимум золы. Это позволяет увеличить интервал обслуживания котла, снизить время и частоту обслуживания. Топливные брикеты понижают вероятность появления коррозии поверхности котла, труб и дымохода.
Про бани и сауны
Топливные брикеты сильно облегчают обслуживание банных комплексов и саун. Во-первых, брикеты упаковывают в пачки по 10–12 килограмм. Их легко разгружать, переносить и очень удобно хранить. Освобождается много места, становится чище и опрятнее.
Во-вторых, брикеты имеют влажность всего 8%. Их не нужно высушивать перед применением — это экономит силы и время. Теплотворность брикетов в два раза выше сухих березовых дров, а горят они в три раза дольше. С помощью топливных брикетов баню можно растопить в два раза быстрее. При закрытых заслонках топки топливные брикеты будут тлеть до трех часов, наполняя прекрасными ароматами дерева все пространство вокруг. Они не содержат химических добавок и ядовитых смол, сохранят в чистоте вашу топку и дымоход.
Другое применение
Топливные брикеты можно использовать где угодно. Они аккуратно и безопасно горят в каминах, наполняя пространство лесными запахами и согревая все пространство. Брикеты можно брать на природу для приготовления шашлыков, для обогрева палатки и лежбища на ночь. С помощью брикетов можно отапливать теплицы, подвалы, чердаки и гаражи. Это удивительный и универсальный вид топлива.
toplivobriket.ru
Топливный брикет
Изобретение относится к области твердотопливных брикетов на основе углеродсодержащих материалов, используемых для автономного обогрева жилых и хозяйственных помещений, теплиц и парников, железнодорожных вагонов, бытовок для рабочих и военнослужащих, а также приготовления пищи в мангалах и грилях. Топливный брикет содержит измельченный древесный уголь с размером частиц от 0,05 мм до 5 мм, воду и связующее, выбранное из крахмала, карбоксилметилцеллюлозы, или гидросиликата натрия или сапропеля при следующем соотношении компонентов, мас.%: крахмал от 4 до 8, или карбоксилметилцеллюлоза от 4 до 8, или гидросиликат натрия от 2 до 5, или сапропель от 2 до 10, вода менее 3, измельченный древесный уголь - остальное до 100, а плотность топливного брикета составляет от 500 кг/м3 до 900 кг/м3. Заявляемое техническое решение расширяет ассортимент твердого топлива и обеспечивает создание экологически чистого брикетированного топлива с высокими энергетическими и прочностными характеристиками. Технический результат - повышение теплоты сгорания и снижение зольности топливных брикетов, увеличение их прочности на сбрасывание, а также улучшение процессов воспламенения и каталитического горения топливных брикетов. 5 з.п. ф-лы.
Область техники, к которой относится изобретение
Изобретение относится к области твердотопливных брикетов на основе углеродосодержащих материалов, в частности к топливным брикетам, используемым в бытовых условиях для автономного, экологически чистого и экономичного обогрева жилых и хозяйственных помещений, теплиц и парников, особенно в районах, не имеющих природных топлив (дров, каменного угля, торфа и т.п.), для каминов, походных печек, самоваров и для отопления железнодорожных вагонов, бытовок для рабочих и военнослужащих, а также приготовления пищи в мангалах, грилях и шашлычницах.
Уровень техники
Известен топливный брикет и способ его получения по патенту РФ 2078120, МКИ C10L 5/16, опубл. 1997, включающий термообработанную формованную смесь угольной мелочи и связующего, содержащего производную сульфокислоты (лигносульфонат или натриевую соль метиленнафталинсульфокислоты) не менее 0,5% от массы угля и пек из кубового остатка ректификации талового масла не менее 0,5% от массы угля (например, омыленный или окисленный таловый пек). Данный брикет обладает недостаточной механической прочностью, сложным и длительным процессом изготовления топливных брикетов, высокой себестоимостью из-за большого ассортимента сырья.
Известен также топливный брикет и способ его получения по патенту РФ 2130047, МКИ C10L 5/12, опубл. 1999 г., содержащий высушенные смеси измельченных твердых топлив и связующего на основе нефтешлама и/или отработанного машинного масла, а также компоненты из группы, включающей, % от массы брикетируемой смеси:
лигносульфонат или мелассу, -2-7 и/или
обезвоженный активный ил, - 3 - 8 и/или
глину, - 3 - 10 и/или
парафин или парафиновый гач - 1-6 при следующем соотношении компонентов, мас.%:
связующее - 10-32, измельченные твердые топлива из группы древесные опилки, торф, обезвоженный птичий помет, обезвоженный навоз, коксовая или угольная мелочь, угольный шлам, лигнин или их смеси - до 100. Недостатком данного брикета является сложный технологический процесс изготовления брикета, высокая энергоемкость и себестоимость продукции, а также большая остаточная влажность 3-12%.
Кроме того, известен топливный брикет по патенту РФ 2043392, МКИ C10L 5/14, опубл. 1995, предназначенный для обогрева теплиц и других помещений. Топливный брикет содержит натриевую соль карбоксиметилцеллюлозы 3-5%, нитрат калия 2-6%, измельченный древесный уголь остальное. Основным недостатком данного топливного брикета является выделение в процессе горения топливных брикетов веществ, преимущественно солей натрия и калия, воздействие которых на пищевые продукты в процессе их приготовления в мангалах, грилях и шашлычницах ухудшает органолептические свойства.
Наиболее близким по существу технического решения к заявляемому топливному брикету является известный топливный брикет по патенту РФ 2187542, МКИ C10L 5/12, опубл. 2002, включающий измельченный древесный уголь, связующее и воду, причем в качестве связующего он содержит крахмал, или пшеничную муку, или декстрин при следующем соотношении компотентов, мас.%:
измельченный древесный уголь - 50-93,
крахмал, или пшеничная мука, или декстрин - 3-45,
вода - остальное до 100.
К основным недостаткам таких топливных брикетов следует отнести недостаточную механическую прочность (плотность топливного брикета от 350 до 450 кг/м3) и довольно высокую остаточную влажность (от 3 до 5 мас.%).
Сущность изобретения
Задачей настоящего изобретения является разработка и создание экологически чистого брикетированного топлива каталитического горения (горение без пламени) с улучшенными энергетическими и прочностными характеристиками, изготовляемого из доступного, дешевого и экологически чистого сырья и применимого как для обогрева помещений, в том числе жилых, так и для приготовления пищи в мангалах, грилях и шашлычницах без ухудшения ее органолептических свойств.
В результате решения данной задачи при реализации изобретения могут быть получены новые технические результаты, заключающиеся в повышении теплоты сгорания и снижении зольности топливных брикетов, в увеличении их прочности на сбрасывание, а также в улучшении процессов воспламенения и каталитического горения топливных брикетов за счет снижения величины остаточной влажности.
Данные технические результаты достигаются тем, что в топливном брикете, содержащем измельченный древесный уголь с размером частиц от 0,05 мм до 5 мм, воду и связующее, выбранное из крахмала, карбоксилметилцеллюлозы, гидросиликата натрия или сапропеля при следующем соотношении компонентов, мас.%:
- крахмал от 4 до 8 или
- карбоксилметилцеллюлоза от 4 до 8, или
- гидросиликат натрия от 2 до 5, или
- сапропель от 2 до 10,
- вода менее 3,
- измельченный древесный уголь - остальное до 100, а плотность топливного брикета составляет от 500 кг/м3 до 900 кг/м3.
Отличительная особенность заявляемого топливного брикета состоит в том, что связующее выбрано из крахмала, карбоксилметилцеллюлозы, гидросиликата натрия или сапропеля при следующем соотношении компонентов, мас.%:
- крахмал от 4 до 8 или
- карбоксилметилцеллюлоза от 4 до 8, или
- гидросиликат натрия от 2 до 5, или
- сапропель от 2 до 10,
- вода менее 3,
- измельченный древесный уголь с размером частиц от 0,05 мм до 5 мм - остальное до 100, а плотность топливного брикета составляет от 500 кг/м3 до 900 кг/м3. В результате повышается теплотворная способность и прочность заявляемых топливных брикетов, а также уменьшается время их разжигания. Причем экспериментально было установлено, что выбранные диапазоны связующего и плотности топливного брикета обеспечивают увеличение прочностных и эксплуатационных характеристик топливных брикетов, лишь при выполнении топливных брикетов с определенными вышеприведенными параметрами и при содержании остаточной влаги в топливных брикетах после их сушки менее 3 мас.%.
Таким образом, из приведенного выше следует, что новые технические результаты могут быть получены при реализации всех существенных признаков, характеризующих заявляемый топливный брикет.
Кроме того, в качестве же связующего может быть использован картофельный крахмал, кукурузный крахмал или их смеси и/или карбоксилметилцеллюлоза, а также водный раствор гидросиликата натрия с содержанием воды 10% (жидкое стекло) или сапропель озера Руковского Владимировской области.
Причем топливный брикет выполнен в виде таблетки (цилиндрической шашки) с диаметром от 30 мм до 100 мм и отношением длины L таблетки к ее диаметру d от 0,4 до 2,0 или призматической шашки с высотой от 20 мм до 40 мм, шириной от 40 мм до 80 мм и длиной от 80 мм до 150 мм.
Сведения, подтверждающие возможность осуществления изобретения
В качестве исходного сырья для изготовления топливных брикетов используют измельченный древесный уголь с размером частиц от 0,05 мм до 5 мм, например пылевидную крошку - отходы производства (по фракционному составу) высококачественного древесного угля (ГОСТ 7637-84, ГОСТ 7657-88). В качестве связующего используют картофельный крахмал (ГОСТ 4567-89), кукурузный крахмал или их смесь и/или карбоксиметилцеллюлозу, или гидросиликат натрия (силикат-глыба - отход стекольного производства), например жидкое стекло - водный раствор гидросиликата натрия с 10% содержанием воды или сапропель, например сапропель озера Руковского Владимировской области.
Вышеуказанные исходные компоненты после дозирования смешивают с водой и тщательно перемешивают при комнатной температуре, например, в смесителе СПУ-2, снабженном планетарными мешалками и обогревом. Дозирование исходных компонентов осуществляют общеизвестными методами путем взвешивания на весах соответствующего класса точности или с применением дозаторов. Полученную однородную смесь выдерживают для набухания связующего, после чего производят брикетирование.
Брикетирование исходных компонентов осуществляют посредством гидравлического пресса (давление прессования от 50 кг/см2 до 200 кг/см2) в таблетки или цилиндрические шашки диаметром от 30 мм до 100 мм и отношением длины L таблетки к ее диаметру d от 0,4 до 2,0, а также в призматические шашки высотой от 20 мм до 40 мм, шириной от 40 мм до 80 мм и длиной от 80 мм до 150 мм. Затем топливные брикеты подвергают сушке, например, при температуре 120°С до содержания остаточной влаги в топливном брикете менее 3%.
Промышленный выпуск топливных брикетов может быть осуществлен на предприятиях, имеющих промышленное смесительное (смесители любого типа: бетономешалки, «пьяные бочки», тестомесители, смесители с мешалками) и формовочное (шнек-прессы, прессы для проходного прессования, прессы для глухого прессования) оборудование, а также сушильные шкафы с температурой сушки от 80°С до 180°С и принудительной конвекцией воздуха.
Рецептура заявляемого топливного брикета иллюстрируются следующими примерами.
Пример 1. На вышеуказанном оборудовании из измельченного древесного угля с размером частиц ~0,1 мм изготовлена партия топливных таблеток диаметром 50 мм и высотой 48 мм. Состав топливных таблеток, мас.%: уголь древесный 92, картофельный крахмал 6 и вода 2. Прессуют и сушат по вышеуказанной технологии. Полученные топливные брикеты легко воспламеняются от спички, горят с едва различимым красным свечением без образования пламени, дыма, копоти, токсичных веществ и без запаха в течение 2 часов и выделяют большое количества тепла, достаточное для обогрева теплиц и других помещений, в том числе жилых помещений в холодное время года. Топливные брикеты имеют плотность 700 кг/м3, удельную теплоту сгорания 7000 ккал/кг и тепловую мощность более 2 Вт/см2 при нормальных условиях.
Пример 2. На том же оборудовании из измельченного древесного угля с размером частиц ~ 0,1 мм изготовлена партия топливных таблеток диаметром 50 мм и высотой 48 мм. Состав топливных таблеток, мас.%: уголь древесный 92, карбоксилметилцеллюлоза 6 и вода 2. Смешивают, прессуют и сушат по режимам примера 1. Готовые топливные брикеты не уступают по качеству вышеприведенным, имеют плотность 700 кг/м3, удельную теплоту сгорания 7000 ккал/кг и тепловую мощность более 2 Вт/см2 при нормальных условиях.
Пример 3. На том же оборудовании из измельченного древесного угля с размером частиц ~0,1 мм изготовлена партия топливных таблеток диаметром 50 мм и высотой 48 мм. Состав топливных таблеток, мас.%: уголь древесный 94, гидросиликат натрия 4 и вода 2. Смешивают, прессуют и сушат по режимам примера 1. Готовые топливные брикеты обладают повышенной механической прочностью, а в остальном не уступают по качеству вышеприведенным, имеют плотность 700 кг/м3, удельную теплоту сгорания 7200 ккал/кг и тепловую мощность более 2 Вт/см2 при нормальных условиях.
Пример 4. На том же оборудовании из измельченного древесного угля с размером частиц ~0,1 мм изготовлена партия топливных таблеток диаметром 50 мм и высотой 48 мм. Состав топливных таблеток, мас.%: уголь древесный 94, сапропель 4 и вода 2. Смешивают, прессуют и сушат по режимам примера 1. Готовые топливные брикеты не уступают по качеству вышеприведенным, имеют плотность 700 кг/м3, удельную теплоту сгорания 7200 ккал/кг и тепловую мощность более 2 Вт/см2 при нормальных условиях.
Пример 5. На том же оборудовании из измельченного древесного угля с размером частиц ~0,1 мм изготовлена партия топливных таблеток диаметром 50 мм и высотой 48 мм. Состав топливных таблеток, мас.%: уголь древесный 80, крахмал 18 и вода 2. Смешивают, прессуют и сушат по режимам примера 1. Готовые топливные брикеты уступают по качеству вышеприведенным, имеют плотность 700 кг/м3, удельную теплоту сгорания 6000 ккал/кг и тепловую мощность менее 2 Вт/см2 при нормальных условиях.
Пример 6. На том же оборудовании из измельченного древесного угля с размером частиц ~ 0,1 мм изготовлена партия топливных таблеток диаметром 50 мм и высотой 48 мм. Состав топливных таблеток, мас.%: уголь древесный 92, крахмал 3, карбоксилметилцеллюлоза 3 и вода 2. Смешивают, прессуют и сушат по режимам примера 1. Готовые топливные брикеты по качеству аналогичны топливным брикетам примеров 2, 3 и 4, имеют плотность 700 кг/м3, удельную теплоту сгорания 7200 ккал/кг и тепловую мощность более 2 Вт/см2 при нормальных условиях.
Пример 7. На том же оборудовании из измельченного древесного угля с размером частиц ~0,1 мм изготовлена партия топливных таблеток диаметром 50 мм и высотой 48 мм. Состав топливных таблеток, мас.%: уголь древесный 96, крахмал 2 и вода 2. Смешивают, прессуют и сушат по режимам примера 1. Готовые топливные брикеты имеют плотность 700 кг/м3, удельную теплоту сгорания 7200 ккал/кг и тепловую мощность более 2 Вт/см2 при нормальных условиях, но имеют малую механическую прочность.
Пример 8. На том же оборудовании из измельченного древесного угля с размером частиц ~0,1 мм изготовлена партия топливных таблеток диаметром 50 мм и высотой 48 мм. Состав топливных таблеток, мас.%: уголь древесный 88, крахмал 6 и вода 6. Смешивают, прессуют и сушат по режимам примера 1. Готовые топливные брикеты имеют плотность 700 кг/м3, удельную теплоту сгорания 7000 ккал/кг и тепловую мощность более 2 Вт/см2 при нормальных условиях, но плохо воспламеняются и затухают после воспламенения.
Пример 9. На том же оборудовании из измельченного древесного угля с размером частиц ~5,5 мм изготовлена партия топливных таблеток диаметром 50 мм и высотой 48 мм. Состав топливных таблеток, мас.%: уголь древесный 92, крахмал 6 и вода 2. Смешивают, прессуют и сушат по режимам примера 1. Готовые топливные брикеты имеют плотность 600 кг/м3, удельную теплоту сгорания 6500 ккал/кг и тепловую мощность менее 2 Вт/см2 при нормальных условиях и при этом имеют малую механическую прочность.
Пример 10. На том же оборудовании из измельченного древесного угля с размером частиц ~0,1 мм изготовлена партия топливных таблеток диаметром 50 мм и высотой 80 мм. Состав топливных таблеток, мас.%: уголь древесный 92, крахмал 6 и вода 2. Смешивают, прессуют и сушат по режимам примера 1. Готовые топливные брикеты имеют плотность 600 кг/м3, удельную теплоту сгорания 6500 ккал/кг и тепловую мощность менее 2 Вт/см2 при нормальных условиях, и при этом имеют малую механическую прочность.
Пример 11. На том же оборудовании из измельченного древесного угля с размером частиц ~0,1 мм изготовлена партия топливных призматических шашек высотой 30 мм, шириной 60 мм и длиной 90 мм. Состав призматических шашек, мас.%: уголь древесный 92, крахмал 6 и вода 2. Смешивают, прессуют и сушат по режимам примера 1. Готовые топливные брикеты превосходят по качеству брикеты, описанные в примере 1, имеют плотность 720 кг/м3, удельную теплоту сгорания 7200 ккал/кг и тепловую мощность более 2 Вт/см2 при нормальных условиях.
Пример 12. На том же оборудовании из измельченного древесного угля с размером частиц ~0,1 мм изготовлена партия топливных призматических шашек высотой 30 мм, шириной 60 мм и длиной 90 мм. Состав призматических шашек, мас.%: уголь древесный 92, карбоксилметилцеллюлоза 6 и вода 2. Смешивают, прессуют и сушат по режимам примера 1. Готовые топливные брикеты превосходят по качеству брикеты, приведенные в примере 1, имеют плотность 720 кг/м3, удельную теплоту сгорания 7200 ккал/кг и тепловую мощность более 2 Вт/см2 при нормальных условиях.
Пример 13. На том же оборудовании из измельченного древесного угля с размером частиц ~0,1 мм изготовлена партия топливных призматических шашек высотой 30 мм, шириной 60 мм и длиной 90 мм. Состав призматических шашек, мас.%: уголь древесный 94, гидросиликат натрия 4 и вода 2. Смешивают, прессуют и сушат по режимам примера 1. Готовые топливные брикеты превосходят по качеству брикеты, приведенные в примере 1, имеют плотность 740 кг/м3, удельную теплоту сгорания 7400 ккал/кг и тепловую мощность более 2 Вт/см2 при нормальных условиях.
Пример 14. На том же оборудовании из измельченного древесного угля с размером частиц ~0,1 мм изготовлена партия топливных призматических шашек высотой 30 мм, шириной 60 мм и длиной 90 мм. Состав призматических шашек, мас.%: уголь древесный 94, сапропель 4 и вода 2. Смешивают, прессуют и сушат по режимам примера 1. Готовые топливные брикеты превосходят по качеству брикеты, приведенные в примере 1, имеют плотность 740 кг/м3, удельную теплоту сгорания 7400 ккал/кг и тепловую мощность более 2 Вт/см2 при нормальных условиях.
Из вышеприведенных примеров видно, что энергетические и прочностные характеристики топливных брикетов варьируются в зависимости от конкретных количественных соотношений ингредиентов. Увеличение количества связующего свыше заявленных пределов приводит к снижению энергетических показателей топливных брикетов, а уменьшение количества связующего приводит к снижению прочностных свойств топливных брикетов и даже их разрушению. Увеличение количества воды ухудшает процесс воспламенения и приводит к парообразованию.
Испытания, проведенные в ОКБ-1 ЭНИН им. Г.М. Кржижановского, подтвердили соответствие заявляемых топливных брикетов ТУ 2162-465-00209591-97. Кроме того, испытания показали, что при использовании в качестве связующего жидкого стекла или силиката-глыбы прочность топливного брикета на раздавливание увеличивается в 1,5 раза, а на истирание - в 2 раза.
Необходимо отметить, что отсутствие открытого пламени при горении топливных брикетов исключает воспламенение при попадании на поверхность горящего брикета легко воспламеняющихся жидкостей, например бензина, спирта, ацетона и т.п. Это свойство топливных брикетов позволяет расширить их область применения за счет использования заявляемых топливных брикетов при разогреве в зимних условиях автомобильных двигателей, газопроводной арматуры и т.п.
1. Топливный брикет, содержащий измельченный древесный уголь с размером частиц от 0,05 до 5 мм, воду и связующее, выбранное из крахмала, карбоксилметилцеллюлозы, или гидросиликата натрия или сапропеля при следующем соотношении компонентов, мас.%:
крахмал | от 4 до 8, или |
карбоксилметилцеллюлоза | от 4 до 8, или |
гидросиликат натрия | от 2 до 5, или |
сапропель | от 2 до 10 |
вода | менее 3 |
измельченный древесный уголь | остальное до 100, |
2. Топливный брикет по п.1, отличающийся тем, что в качестве связующего использован картофельный крахмал, кукурузный крахмал или их смеси.
3. Топливный брикет по п.1, отличающийся тем, что в качестве связующего использован водный раствор гидросиликата натрия с содержанием воды 10%.
4. Топливный брикет по п.1, отличающийся тем, что в качестве связующего использован сапропель озера Руковского Владимирской области.
5. Топливный брикет по п.1, отличающийся тем, что топливный брикет выполнен в виде таблетки (цилиндрической шашки) с диаметром, выбранным от 30 до 100 мм, а отношение длины L таблетки к ее диаметру d составляет от 0,4 до 2,0.
6. Топливный брикет по п.1, отличающийся тем, что топливный брикет выполнен в виде призматической шашки с высотой, выбранной от 20 до 40 мм, шириной, выбранной от 40 до 80 мм, и длиной, выбранной от 80 до 150 мм.
www.findpatent.ru