Виды стеклопластиковых труб, характеристики, способы соединения. Стеклопластиковых труб монтаж
Минусы стеклопластиковых труб
Трубы из стеклопластика стали популярны всего лишь пятьдесят лет назад. Технология была разработана и воплощена на производстве благодаря западным ученым. Американцы научились использоваться специальные добавки и композитные составляющие, чтобы получить новый материал. В результате применения новой технологии, на рынке стройматериалов стали предлагаются такие изделия, как стеклопластиковые трубы.
Стеклопластиковая труба выполняется из уникального материала – стеклопластика с добавлением специальных компонентов: смолы, армирующих материалов. В результате производственного процесса, материал приобретает свойства, которые дополняют уже имеющиеся характеристики.
Где применяются конструкции такого типа?
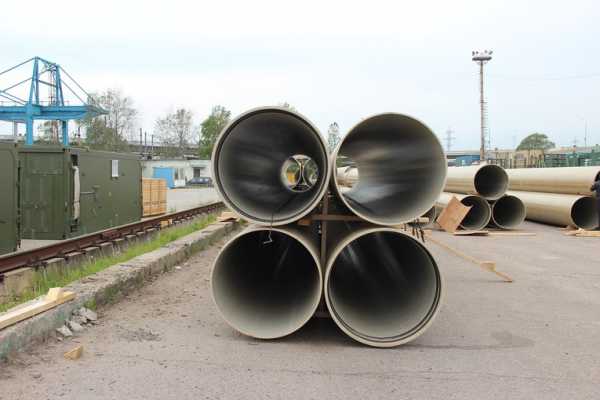
Сфера использования труб из стеклопластика очень широка. Конструкции разрешается использовать для устройства системы канализации и водоотведения. Также их применяют в процессе пожаротушения и при перевозке питьевой и технической воды. Разрешается прокладывать трубы на электростанциях и использовать для организации оттока различных видов отходов. Следует отметить, что трубы из стеклопластика широко используются при прокладке коммуникаций различного типа:
· магистральных систем коммуникаций;
· различных систем канализационного типа;
· водопроводов и дополнительных систем;
· в случаях прокладки газо- и нефтепроводов.
Как правило, трубы выпускаются в рамках стандартного технологического процесса. Готовая продукция используется для различных целей и может иметь особые параметры. Также, заводы-изготовители выпускают дополнительные комплектующие. Помимо труб стандартных размеров, по индивидуальным заказам изготавливаются трубы с другими диаметрами и характеристиками.
Для стандартной трубы предусмотрены следующие параметры:
· диаметр трубы находится в диапазоне от 300 до 4000 мм;
· длина трубы может составлять до 18 метров;
· трубы могут иметь шесть классов давления;
· материал имеет три уровня прочности.
Благодаря этим показателям, трубы из стеклопластика отличаются высоким качеством и долговечностью. Подобные конструкции отличаются высоким качеством изделий и долговечностью.
Плюсы и минусы труб из стеклопластика
Трубы такого типа имеют как преимущества, так и недостатки. Минусы стеклопластиковых труб незначительные и в основном сводятся к монтажу, который необходимо выполнять согласно инструкции. В основном трубы выпускаются по стандартной технологии определенных размеров и параметров. Основная масса труб выпускается по стандартной схеме. В процессе стекловолоконные нити наматываются на оправу непрерывным методом. Для придания конструкции повышенной прочности, нить армируется специальным составом из стекловолокна и пропитывается смоляной смесью, измельченным стекловолокном и песком.
Это позволяет получить готовый продукт с длительным сроком эксплуатации, до пятидесяти лет. Говорить о более длительном периоде использования пока не представляется возможным, поскольку с момента изготовления первых труб срок их эксплуатации еще не подошел к концу. Но, по мнению экспертов, трубы такого типа могут эксплуатироваться намного дольше.
Преимущества труб из стеклопластика:
· продолжительный период использования;
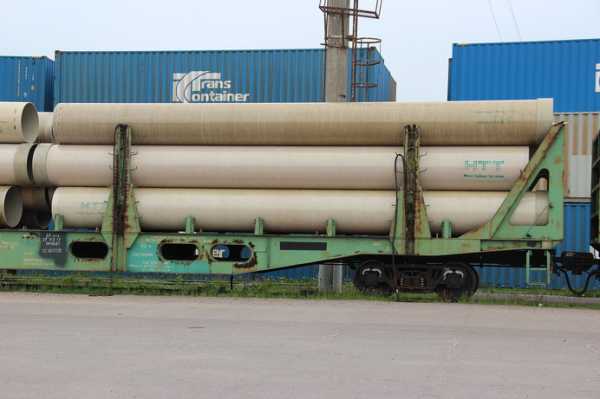
· монтаж стеклопластиковых труб выполняется в короткие сроки и с минимальными финансовыми расходами. Для этой цели подойдет муфтовое соединение и другие методики. Сварку и другие способы соединения использовать не требуется;
· все трубы имеют небольшой вес, который составляет порядка 80% от веса металлических конструкций;
· трубы не ржавеют и не поддаются воздействию коррозии;
· материал устойчив к изнашиванию, не подвергается воздействию различных агрессивных сред;
· трубы можно использовать в любое время года, независимо от окружающей среды и температурных показателей;
· стоимость материала отличается доступностью, благодаря низкой цене сырья;
· трубы отвечают всем нормам экологии;
· стеклопластик способен выдерживать различные температурные колебания: от – 65 до 155 градусов Цельсия;
Все указанные показатели являются преимуществами и позволяют считать стеклопластиковые трубы универсальной продукцией для устройства различных систем.
В качестве минусов таких изделий можно отменить такие, как низкая устойчивость к нагрузкам и появлению трещин. В результате этого, трубы при прокладке нефтепровода использовать нельзя. Этого можно избежать, если усилить герметизацию труб изнутри при помощи специального рифленого герметизирующего слоя.
Как выбрать тип стеклопластиковой трубы?
Чтобы выбрать подходящий материал, необходимо учитывать ряд следующих показателей:
· намотка стеклопластиковой трубы не должна иметь деформаций и посторонних вкраплений;
· поверхность материала должна быть ровной и гладкой;
· края трубы не должны иметь трещин или расслоений.
Крайне важно, чтобы трубы можно было сверлить распиливать, фрезеровать и даже точить. Это позволяет создать качественный водопровод или иную систему.
Если все работы выполнены качественно, а все трубы произведены согласно требуемым стандартам и технологиям, срок эксплуатации может быть увеличен в несколько раз. Напорные стеклопластиковые трубы применяются для создания самых сложных систем водоснабжения, поскольку имеют высокие качественные характеристики.
ООО «Новые Трубные Технологии» занимаются выпуском и разработкой труб из стеклопластика разного уровня качества. Материал очень практичный, продуманный, надежный. Каждая труба отвечает экологическим нормам и госстандарту. У нас вы сможете приобрести трубы по доступной цене и в любое удобное время.
www.ntt.su
производство труб из стеклопластика большого диаметра, монтаж
Содержание:
Одним из материалов, которые используются для изготовления полимерной трубной продукции, является стеклопластик, обладающий уникальными характеристиками. В основном стеклопластиковые трубы применяют в промышленных целях, но и среди бытовых застройщиков они становятся все более востребованными.
Область применения
Стеклопластик относится к композитным материалам, которые характеризуются высокой прочностью. По утверждению производителей стеклопластиковых труб эти изделия, пропитанные эпоксидными или полиэфирными или смолами, можно задействовать с целью прокладки трубопроводов самого разного назначения и наземным, и подземным способом.
Они превосходно функционируют при высоком давлении транспортируемых жидкостей и газов, в различных климатических условиях, даже самых суровых. На внутреннюю поверхность трубы из стеклопластика при необходимости наносят специальные защитные покрытия, позволяющие передвигаться по магистрали жидким и газообразным веществам. По стойкости к коррозийным процессам стеклопластиковые изделия превосходят металлические изделия.
Благодаря высокому качеству данной трубной продукции, область ее использования практически не ограничена, из нее прокладывают:
- водопроводные системы и магистрали;
- канализационные сети;
- нефте- и газопроводы.
Также такой вид изделий как стеклопластиковая трубка используют при производстве высоковольтной аппаратуры.
Основное преимущество применения продукции из стеклопластика заключается в том, что затраты на прокладку трубопровода окупаются в кратчайшие сроки, поскольку эксплуатационные расходы снижаются почти вдвое.
Виды стеклопластиковых труб
Изделия, произведенные из стеклопластика, бывают двух типов:
- Однослойными. Композитный материал для их изготовления состоит из двух компонентов. Производство основано на технологии мокрой намотки. В составе материала для труб присутствуют стеклянные пряди и связывающее вещество, которым являются эпоксидные смолы. Эти изделия имеют низкое сопротивление передвигающемуся потоку и устойчивость к химическим воздействиям.
- Многослойными. Такие стеклопластиковые трубы покрыты дополнительными оболочками из полиэтилена. Для связки слоев применяют процесс высокотемпературной полимеризации. Такое покрытие способствует повышению устойчивости продукции к различным воздействиям.
Многослойные стеклопластиковые трубы большого диаметра применяют при прокладке магистральных газопроводов в особо неблагоприятных климатических условиях.
Физические характеристики труб из стеклопластика
Поскольку изделия отличаются незначительным весом, затраты на прокладку магистралей из них снижаются. Например, стеклопластиковая труба со спиральной намоткой отличается плотностью 1,8-1,9 т/м³, а произведенная по непрерывной технологии имеет показатель 1,6-1,7 т/ м³.
Обладание большим ресурсом жесткости позволяет им выдерживать существенные нагрузки, оказываемые давлением грунта.
Стеклопластиковые трубы сертифицированы по стандартам ISO и соответствуют определенным классам жесткости:
- SN 2500 – для таких изделий рабочее давление не должно превышать 0,4 Мпа;
- SN 5000 - для них предел данного параметра составляет 1 Мпа;
- SN 10000 - в данном случае предельный показатель рабочего давления 2,5 Мпа.
Большую прочность изделиям обеспечивает спиральная намотка.
Варианты соединения элементов трубопровода
Существует несколько способов прокладки систем из стеклопластиковых труб:
- Применение раструбного изделия отличается простотой проведения работ – это вариант последовательного монтажа, при котором одну трубу помещают в раструб другой.
- При использовании фланцевого соединения стеклопластиковая трубная продукция имеет на торцах фланец (специальное кольцо) с отверстиями, предназначенными под крепежные детали.
- Монтаж стеклопластиковых труб при помощи муфтовых соединений предусматривает прокладку трубопроводов с применением съемных и неразъемных элементов. К последнему виду относится муфта, которую фиксируют клеящими составами.
- Бугельное соединение считается разновидностью муфтового, но оно разъемное и его после монтажа стягивают болтами.
Кроме вышеперечисленных способов для стыковки стеклопластиковых труб задействуют резьбовые и винтовые элементы.
Маркировка защитных покрытий
Производители труб из стеклопластика в соответствии с особенностями защитного покрытия, от которого зависит назначение изделий, применяют определенные буквенные обозначения:
- П – продукция предназначена для прокладки водопроводных сетей, в том числе подающих питьевую воду;
- Г – означает, что такие трубы можно использовать при обустройстве систем горячего водоснабжения. Максимальная температура теплоносителя не должна превышать 75 градусов;
- Х – изделия предназначаются для перемещения химически активных газов и жидкостей;
- А – по таким трубам разрешается перекачка смесей, содержащих абразивные компоненты;
- С – таким символом обозначают универсальные изделия, которые можно использовать практически для любой цели, поскольку они устойчивы даже к жидкостям с повышенной кислотностью.
В процессе производства стеклопластиковых труб слой защитного покрытия может достигать 3-х миллиметров.
Возможность выполнять монтаж стеклопластиковых труб без применения сварочного оборудования и другие их достоинства делают данную трубную продукцию очень перспективным материалом. В последние годы объем ее реализации постоянно возрастает. Важную роль при этом играет невысокая стоимость содержания и технического обслуживания трубопроводов, изготовленных из стеклопластика.
trubaspec.com
видео-инструкция по монтажу своими руками, особенности производства, изделий большого диаметра, для отопления, ГОСТ, диаметры, цена, фото
Как выглядит производство труб из стеклопластика? Какими должны быть стеклопластиковые трубы по ГОСТу? Насколько привлекательны их характеристики на фоне альтернативных решений? Давайте попробуем ответить на эти вопросы.
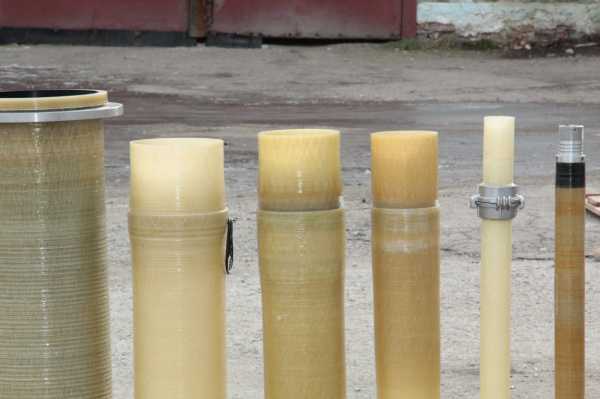
Образцы труб с соединениями разных типов.
Что это такое
Что представляет собой стеклопластик? Название, в общем-то, дает исчерпывающее представление о составе материала: связующее (эпоксидная или полиэфирная смола) армируется стекловолокном. Армирование обеспечивает устойчивость по отношению к нагрузкам на растяжение и изгиб; связующее гарантирует стойкость к ударным нагрузкам.
Обратите внимание: применяющиеся смолы — типичные реактопласты.При твердении в них происходят необратимые химические изменения; раз так — в отличие от термопластов, контактная сварка изделий невозможна.Для соединения труб применяются клей, фланцы под болты, резьбы и т.д.

Фланцевое соединение стеклопластикового трубопровода.
История
Технология производства зародилась в пятидесятых годах прошлого века, когда началось промышленное изготовление эпоксидных смол. Как и любая новая технология, на начальном этапе эта не пользовалась особой популярностью: отсутствие опыта использования стеклопластика дополняла невысокая цена на традиционные материалы (сталь, медь и алюминий).
Примерно к середине 60-х, однако, картина начала меняться.
Что произошло?
- Выросли цены на сталь и цветные металлы.
- Началась коммерческая разработка шельфовых месторождений нефти и газа. Стеклопластиковые трубы НКТ (насосно-компрессорные) выгодно отличались от металлических небольшим весом и, что еще важнее, коррозионной стойкостью: контакт с соленой водой не наносил им никакого ущерба, в отличие от конкурирующих продуктов.
- Наконец, сами технологии производства стеклопластика тоже не стояли на месте: он становился дешевле и прочнее.
Результат не заставил себя ждать: к концу 60-х американская компания Ameron вышла со своими стеклопластиковыми трубами высокого давления вначале на североамериканский, а затем и на ближневосточный рынок. К 80-годам подтянулись европейские и, чуть позже, советские (позже — российские) производители.
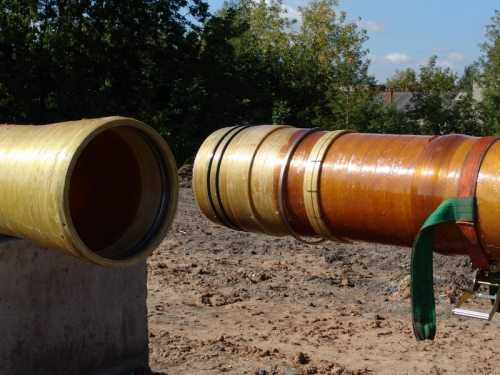
Продукция Ameron и сейчас востребована российским рынком, несмотря на наличие отечественных производителей.
Преимущества
Чем стеклопластик завоевал популярность?
Список его достоинств не слишком велик, но выглядит весьма убедительно.
- Весьма разумная на фоне высоколегированных и нержавеющих сталей стоимость.
- Стойкость к коррозии и агрессивным средам.
Полезно: при необходимости транспортировки особо агрессивных жидкостей элементы трубопроводов футеруются полиэтиленом высокого давления.
- Небольшой вес. Удельная прочность стеклопластика (прочность, отнесенная к плотности) в 3,5 раза выше, чем у стали; таким образом, равнопрочные конструкции из этих материалов будут различаться весом в несколько раз.
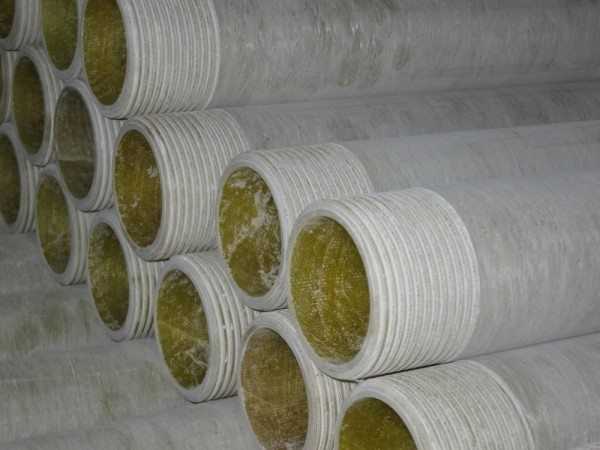
При такой же толщине стенок, как у стальной трубы, стеклопластиковая уступает ей в прочности весьма незначительно.
- Возможность получения материала с заданными механическими свойствами благодаря определенной схеме армирования. Например, спирально-кольцевая намотка стекловолокна обеспечивает высочайшую устойчивость к внутреннему давлению.
Производство
Как выглядит производство стеклопластиковых труб?
К настоящему времени можно выделить четыре основных технологии их изготовления.
Название | Описание |
Экструзия | Смола смешивается с отвердителем и рубленым стекловолокном, после чего продавливается экструдером через кольцевое отверстие. Производство дешево, технологично, однако отсутствие регулярного армирующего каркаса сказывается на итоговой прочности изделий. |
Пултрузия | Труба формируется между внутренней и наружной оправками. Обе поверхности получаются идеальными; однако ряд технологических ограничений не позволяет производить таким образом трубы больших диаметров и с высоким рабочим давлением. |
Центробежное формование | Армирование представляет собой готовый рукав из стеклоткани, который прижимается к поверхности вращающейся формы центробежными силами. Они же способствуют равномерному распределению смолы по будущим стенкам. Основное достоинство технологии — возможность получить гладкую наружную поверхность; основной недостаток — энергоемкость и, соответственно, дороговизна. |
Намотка | Пропитанное связующим стекловолокно (нить, лента или ткань) наматывается на цилиндрическую оправку. Оборудование для производства стеклопластиковых труб методом намотки наиболее распространено благодаря относительной простоте и высокой производительности. |
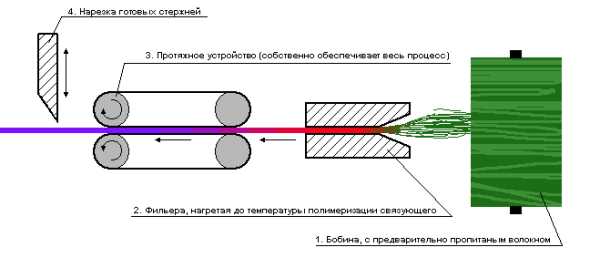
Схема производства методом пултрузии.
У последнего метода производства есть несколько, так сказать, подвидов. Давайте познакомимся с ними.
Спирально-кольцевая намотка
Укладчик — кольцо с несколькими механизмами подачи пропитанной нити — совершает возвратно-поступательные движения вдоль вращающейся оправки. При каждом проходе укладывается слой волокон с постоянным шагом; кольцевая схема укладки, как мы помним, позволяет добиться максимальной прочности трубы на разрыв.
Любопытно: предварительное натяжение нити тоже благоприятно сказывается на итоговой прочности изделия, предотвращая появление трещин при изгибающих нагрузках.
Методом спирально-кольцевой намотки изготавливаются насосно-компрессорные трубы, рассчитанные на высокие рабочие давления, несущие конструктивные элементы (в том числе композитные опоры ЛЭП) и даже… корпуса ракетных двигателей.
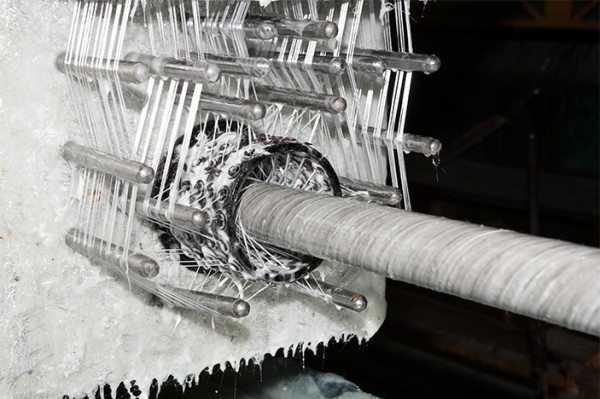
Изготовление НКТ спирально-кольцевой намоткой.
Спирально-ленточная намотка
Разница с предыдущим методом — лишь в том, что за один проход укладчик формирует узкую ленту в десяток-другой волокон. Соответственно, для формирования сплошного армирования требуется куда больше проходов; само армирования получается несколько менее плотным. Главное достоинство метода — куда более простое и, соответственно, дешевое оборудование.
Продольно-поперечная намотка
Принципиальное отличие от предыдущих схем — в том, что намотка делается непрерывной: укладчик одновременно укладывает продольные и поперечные нити. Казалось бы, это должно упростить и удешевить технологию; однако здесь есть сугубо механическая проблема.
Оправка, на которой наматывается будущая труба, вращается; раз так — должны вращаться и катушки, с которых разматывается нить продольного армирования. Причем чем больше диаметр трубы, тем больше должно быть катушек.

Продольно-поперечный намотчик.
Косослойная поперечно-продольная намотка
Это решение было разработано еще при жизни Советского Союза в Харькове и первоначально применялось при производстве корпусов реактивных снарядов. Позже оно получило распространение на всем постсоветском пространстве.
В чем суть метода?
- Укладчик формирует широкую ленту параллельных пропитанных связующим волокон.
- Лента перед намоткой на оправку предварительно обматывается нитью без пропитки, впоследствии образующей осевую арматуру. Сами же собранные в ленту нити образуют, соответственно, арматуру поперечную: лента укладывается поперек оси оправки.
- После укладки каждый слой прокатывается валиками, уплотняющими армирование и вытесняющими лишнее связующее.
Чем выгодна такая схема?
- Возможностью непрерывного производства. За один проход можно сформировать сколь угодно толстые стенки, просто меняя нахлест ленты.
- Высокой производительностью.
- Возможностью производить стеклопластиковые трубы большого диаметра (в теории — без каких-либо ограничений максимального размера). Габариты ограничены только размером оправки.
- Чрезвычайно высоким содержанием стекловолокна в готовом материале. Оно доходит до 85% против 45-65% при альтернативных способах. Это влияет как на итоговую прочность, так и на горючесть продукции.
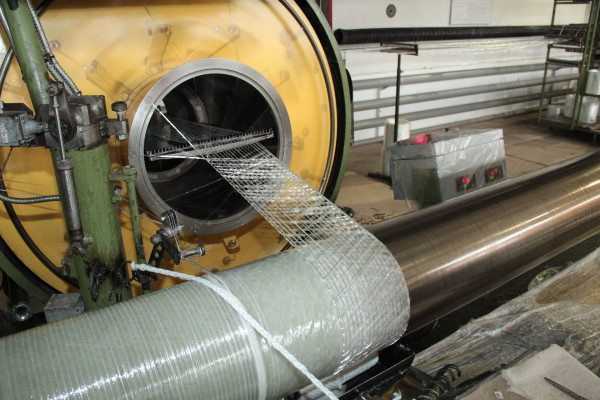
Косослойная поперечно — продольная намотка.
Стандарты
Производство интересующих нас изделий регламентируется двумя нормативными документами:
- ГОСТ Р 53201-2008 содержит техусловия для изготовления труб диаметром 50-200 мм на резьбовых соединениях.
- Разработанный при участии ООО НТТ (Новые Трубные Технологии) ГОСТ Р 54560-2011 описывает детали трубопроводов из «реактопластов, армированных стекловолокном».
Изучим основные положения документов.
ГОСТ Р 53201-2008
Предусмотренный стандартом режим эксплуатации труб выглядит так:
- Температура — от -60 до +60С.
- Относительная влажность — до 100%.
- Температура транспортируемой жидкости — до +110С.
- Рабочее давление — от 3,5 до 27,6 МПа.
Предусматриваются следующие варианты использования описанных стандартом изделий:
- Транспортировка нефти и газового конденсата.
- Транспортировка растворов солей (включая морскую воду).
- Сооружение лифтовых колонн.
- Крепление скважин различного назначения.
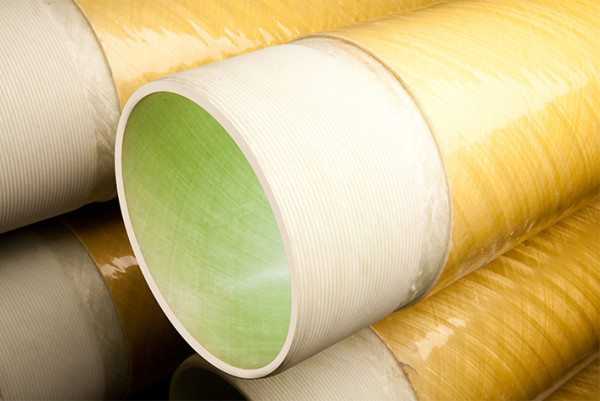
Разобранная обсадная колонна.
- Поддержание пластового давления при разработке подземных месторождений.
- Техническое и питьевое водоснабжение.
Стандарт выделяет три типа труб:
Обозначение | Расшифровка |
НК | Насосно-компрессорные |
О | Обсадные |
Л | Линейные |
Какими могут быть диаметры стеклопластиковых труб, произведенных по ГОСТ Р 53201-2008, и прочие их характеристики?
Насосно-компрессорные, обсадные
Внутренний диаметр, мм | Номинальное давление, МПа | Минимальная толщина стенки, мм | Масса погонного метра, кг |
50 | 6,9 — 27,6 | 4,3 — 8,4 | 1,6 — 3,3 |
63 | 6,9 — 27,6 | 4,6 — 10,7 | 2,2 — 5,5 |
100 | 10,3 — 17,2 | 8,1 — 12,2 | 5,8 — 8,2 |
150 | 10,3 — 17,2 | 13,5 — 15,0 | 14,0 — 14,9 |
200 | 10,3 | 13,6 | 16,5 |
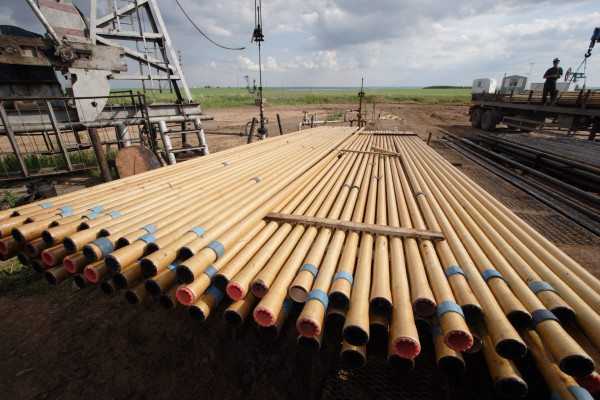
На фото — стеклопластиковые НКТ высокого давления.
Линейные
Внутренний диаметр, мм | Номинальное давление, МПа | Минимальная толщина стенки, мм | Масса погонного метра, кг |
50 | 10,3 — 27,6 | 2,79 — 8,10 | 1,2 — 3,1 |
63 | 8,6 — 27,6 | 2,80 — 9,90 | 1,4 — 5,2 |
100 | 5,5 — 27,6 | 2,80 — 16,00 | 2,3 — 12,8 |
150 | 5,5 — 13,8 | 4,57 — 11,20 | 5,1 — 12,2 |
200 | 5,5 — 13,8 | 5,84 — 14,70 | 8,6 — 22,6 |
Кроме типоразмеров труб, в документе содержится детальная инструкция по изготовлению фитингов с указанием базовых размеров, требования к внешнему виду, максимальным допускам и маркировке всех изделий.
ГОСТ Р 54560-2011
Стандарт описывает трубопроводы, эксплуатирующиеся в куда более мягких по сравнению с описанными выше условиях:
- Рабочее давление — до 3,2 МПа;
- Температура среды — до 35С;
- Транспортируемые жидкости — вода, водные растворы и стоки (бытовые и промышленные).
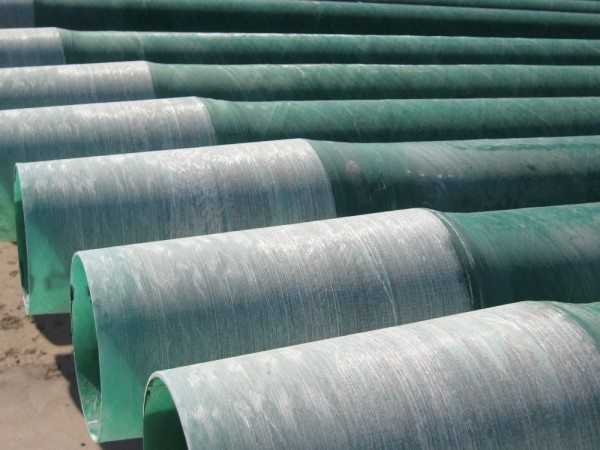
Мягкие требования к прочности позволяют обойтись стенками невысокой толщины.
Важно: действие ГОСТ не распространяется на трубопроводы для внутренних водопроводов и канализации.
В рамках документа продукция классифицируется по следующим признакам:
- Диаметру (DN). Диапазон значений — от 300 до 3000 миллиметров.
- Номинальному давлению (PN). Для безнапорных труб само понятие PN довольно условно и берется равным 0,1 — 0,4 МПа; для напорных оно принимает значения 0,6, 1,0, 1,6, 2,0, 2,5 и 3,2 МПа.
- Номинальной жесткости (SN). Она тоже измеряется в мегапаскалях и может быть равной 1250, 2500, 5000 и 10000.
Обратите внимание: при прокладке стеклопластиковой системы канализации своими руками стоит учитывать, что трубы SN 1250 не рекомендованы для подземной прокладки в принципе, а SN 2500 рекомендуется прокладывать в лотках.
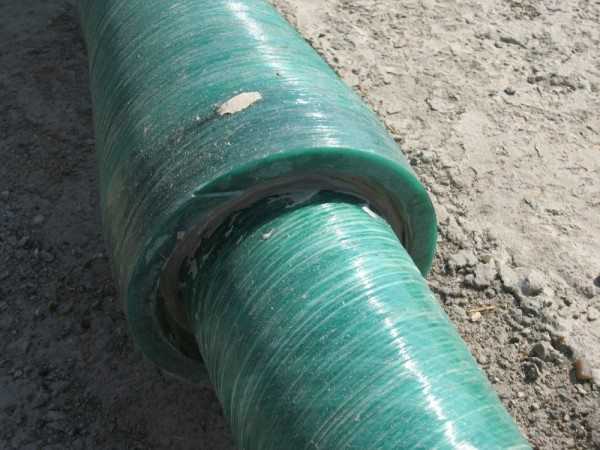
Для подземной укладки используются толстостенные трубы высокой жесткости.
Документ, как и предыдущий, перечисляет основные размеры всех видов фитингов и требования к их внешнему виду, прочности, маркировке и методам армирования.
Заключение
Разумеется, в нашем материале мы коснулись лишь небольшой части весьма обширной темы использования стеклопластика. Мы не выяснили, можно ли применять стеклопластиковые трубы для отопления или бытовой канализации, насколько они хороши на фоне металлополимерных или полностью пластиковых изделий. Часть из этих вопросов затрагивает видео в этой статье. Успехов!
gidroguru.com
Инструкция по монтажу и ремонту трубы из стеклопластика
1. Введение
1.1. Данная памятка определяет:
- последовательность и порядок осуществления мероприятий по соединению трубопроводов из стеклопластика;
- ряд манипуляций по ликвидации дефектов различного типа в зависимости от метода проложения труб и характера неисправностей.
1.2. Руководство обозначает разновидности неполадок, возникающие в ходе использования сетей.
1.3. Представленные правила являются актуальными для изделий сложной формы и труб (d от 60 до 500 миллиметров) при расчетном эксплуатационном давлении не более 10 атмосфер. Монтаж и транспортировку частей необходимо осуществлять при температуре не выше 30°С.
2. Требования безопасности
2.1. При монтаже системы и проведении наладочных манипуляций оптимальная температура воздуха должна находиться в пределах от -10 до +40 градусов.
2.2. В соответствии со СНиП Ш-4-80 нужно придерживаться основных правил технической безопасности и санитарно-гигиенических норм, установленных Министерством Здравоохранения РФ.
2.1. Деятельность, в которой используются полимерные или стекловолоконные материалы, требует соблюдения определенных предписаний:
2.1.1.Необходимо закрывать дыхательные пути с помощью респираторов типа «Лепесток» или РУ-60М.
2.1.2. Для сохранения здоровья глаз и предотвращения попадания в них посторонних частиц необходимо использовать защитные устройства (например, очки марки ЗН4-72) ГОСТ 12.4.013-85Е. Оправа очков должна плотно прилегать к голове и лицу.
2.1.3. Руки необходимо защищать при помощи хлопчатобумажных перчаток (по ГОСТ 5007-87). Для выкладки и пропиточных манипуляций нужно использовать перчатки из резинового материала.
2.1.4. На протяжении всех работ необходимо, чтобы одежда была плотно застегнута.
2.1.5. По окончании работ нужно хорошо вымыть руки с использованием моющих средств и щетки, а также принять душ. Нельзя использовать для очищения кожи растворители. Допускается обработка кожных покровов смесью спирта с глицерином в пропорции 50Х50.
2.2. Любые типы ремонтных работ проводятся только после сбрасывания давления в трубопроводе либо удаления жидкости (устранения очага протечки при аварии).
3. Монтаж трубопровода
3.1. Для свободного доступа к системе, расположенной под землей, нужно вырыть траншею необходимого размера. Габаритные параметры должны позволять нормально работать как минимум двум людям. Между грунтом (в нижней части) и трубой нужно оставить промежуток не менее 300 миллиметров. Весь периметр очищается от грязи, пыли, промывается водой и хорошо высушивается тряпкой (примерно на 400мм в одну и другую сторону).
3.2. При монтировании проводящей системы в качестве неразъединимых клеевых связок используются два вида присоединения (согласно Приложению 4 к «Техническим требованиям по монтажу элементов из стеклопластика»).
3.3. Бандажное соединение
3.3.1. Нужно обеспечивать минимальный просвет между соединяемыми частями. Для этого торцевые части склеиваемых поверхностей, вставочные элементы обрабатываются специальным образом.
3.3.2. В точках соединения торцы зачищаются наждачной бумагой, шлифовальной машинкой или жесткой проволочной щеткой. Следует производить чистку на 150 миллиметров в обоих направлениях от точки стыковки. Любые пылевые загрязнения сразу удаляются.
3.3.3. Из стеклоткани (ГОСТ 19170-73) нарезаются полоски. Их длина должна обеспечить два свободных оборота вокруг поверхности трубы. Первая полоса должна иметь ширину 100 мм. Все следующие пласты будут шире нижележащих на 40 миллиметров. Необходимо также подготовить стеклоленту ЛЭСБ (ГОСТ 5937-81) не менее 30 миллиметровой ширины и обмотать ремонтируемую часть два раза.
3.3.4. Подготовленный отрезок обезжиривается ацетоном и просушивается. Нельзя касаться поверхности руками.
3.3.5. Далее тонким слоем при помощи шпателя наносится компаунд.
Он состоит из двухкомпонентной смолы ЭД-20 (или любого заменителя) и субстанции, обеспечивающей затвердевание (ПЭПА).
Порядок изготовления материала:
Соединить все составляющие в соотношении 100 в.ч. эпоксида к 10 в.ч. отвердителя. Перемешать три-пять минут до получения единой массы. До приготовления все составляющие разогреваются до t 20-25° градусов.
Важно! При температуре воздуха 20°С период реализации материала составляет около получаса.
3.3.6. Стыковочная часть обматывается заготовками, пропитанными клеевым составом. Наиболее узкую полоску нужно положить в первую очередь. Далее накладываются следующие полоски большей ширины в количестве не более 8. Необходимо следить, чтобы на заготовках не было пузырей, складок. Толщина обмоточного покрытия уменьшается от центра к краям. Это понижает концентрацию напряжений. Предварительно необходимо пропитать заготовки связующим веществом на твердом металлическом или деревянном листе (при помощи шпателя или валика). Нельзя допускать появления складок или пузырей. Чтобы закрепить слои, следует обмотать их стеклолентой. Далее производится пропитка связующим веществом. Величина бандажного слоя равняется толщине стенки патрубка.
3.3.7. Сегмент трубопроводной сети туго обматывается пленкой из фторопласта (Ф4). Концы завязываются или фиксируются скотчем.
3.3.8. Сверху устанавливается нагревательный прибор, подключенный к коробке управления, а она к электросети. Пример представлен на рисунке 1.
3.3.9. Выставляется рабочий режим на приборе (70-90°С). Клеящая основа будет отвердевать примерно от 30 до 45 минут.
3.3.10. Проведение сборки стекловолоконного трубопровода допустимо при t не ниже 20 °С. В таком случае на отвердевание клеевого слоя уйдет 24 часа. Требуется обеспечение неподвижности стыковочного сегмента на протяжении всего периода застывания.
3.3.11. Проводить контрольный пуск под давлением допустимо по прошествии суток после отвердения.
3.4. Муфтовое соединение
3.4.1. Сборка частей системы из стеклопластика может производиться с использованием:
- муфт, d которых должен быть сопоставим с наружным диаметром трубы;
- соединительных элементов конусообразной формы;
3.4.2. Следует провести зачистку и обезжиривание наружных частей трубы и муфты (см. п.3.3.2, 3.3.3).
3.4.3. Стягивающая конструкция закрепляется сверху на трубе.
3.4.4. На подготовленные торцевые участки и внутреннюю часть фитингов наносится клеящий раствор, который готовится согласно п. 3.3.5 настоящего руководства. Чтобы предотвратить стекание клеевого слоя, в него вводят «Аэросил» (оксидное соединение кремния). В разогретую эпоксидную смолу (20-25 градусов) добавляется кремниевый оксид. Составляющие смешиваются до получения гомогенной смеси. Количество оксида зависит от условий внешней среды и составляет 5-30 в.ч. на 100 в.ч. мастики. Аэросил добавляется перед отверждающим веществом.
3.4.5. Муфтовая деталь ручным способом насаживается на трубу до упора и поворачивается относительно нее на угол 90 градусов. В противоположную часть помещается другая труба, поворот которой может составлять ± 90 °.
3.4.6. Отверстия для стягивающих стержней и крюков совмещаются между собой.
3.4.7. Оптимальное облегание стыков и соединительных элементов обеспечивается посредством стяжек. Расположение коллектора фиксируется относительно сцепления. Для этого применяются фитинги конусообразной формы.
3.4.8. Если d используемого фитинга совпадает с наружным d трубы, то на его концы надевается хомут (см. п.3.3).
3.4.9. Для обеспечения застывания клеящей смеси нужно применить нагревательный прибор аналогично п. 3.3.7-3.3.8 данной инструкции.
4. Виды неисправностей и способы их устранения
4.1. Возникновение неполадок и появление изъянов возможно по ряду причин:
- потеря целостности патрубка при перевозке и хранении;
- перегруженность сети;
- заводские дефекты;
- некорректное использование;
- несоблюдение технологии монтажа системы и отдельных ее частей.
Во время проведения ремонтной и монтажной деятельности важно уделить повышенное внимание очищению и осушению всех поверхностей. Неправильные подготовительные действия приводят к разрушению клеевых связей, запылению или замасливанию элементов.
4.2. Наладка прорывов, изломов патрубков или их соединений производится путем замены отдельных частей.
4.2.1. Испорченная часть удаляется ножовкой или торцевой машинкой с отрезным кругом.
4.2.2. Торцевые части отрезаются и зашкуриваются (в соответствии с частью 3.3.2).
4.2.3. Далее нужно приготовить специальный реставрационный элемент.
4.2.4. Важно производить монтаж так, чтобы промежуток между ней и трубой был незначительным.
4.2.5. Последующие ремонтные манипуляции необходимо проводить по аналогии с пунктами 3.1 и 3.2. Внутренний диаметральный показатель муфты должен соответствовать наружным габаритам коллектора.
4.3. Починка стеклопластиковых труб с нарушенной герметичностью без замещения испорченных участков (точечная или капельная утечка жидкости).
4.3.1. В экстренных случаях или для устранения протечки под давлением возможно временное наложение хомута с уплотнителем из спецрезины, устойчивой к химическим воздействиям (ГОСТ 7338-90). Ее толщина должна составлять 6-8 мм.
4.3.2. Постановка возможна при наличии сквозных отверстий или трещинах в стенках патрубков. Ширина хомутной накладки должна превышать размер повреждения на 60 и более миллиметров.
4.3.3. Раскрытая часть трубопровода ограждается, поблизости от него выставляются предупреждающие знаки. Засыпка трубопровода грунтом до окончательного завершения ремонта и после проведения временных мер по устранению аварийной ситуации не производится.
4.3.4. Устранение пробоины и уменьшение давления достигается при помощи резиновых, деревянных заглушек или путем полного прекращения подачи транспортируемых веществ.
4.3.5. Технология наложения бандажа (см. п.3.3).
Важно! Установленный хомут должен иметь такую же толщину, как и стенка ремонтируемой трубы, а его величина на 150 мм больше размера повреждения.
4.4. Починка пластмассовых систем без замены отдельных частей и нарушения герметичности.
Любые неисправности на трубах из стеклопластика устраняются в следующем последовательности:
- предварительно осуществляется заливание термосмолой имеющихся царапин, сколов;
- далее производится накладка бандажной ленты из стеклотекстолита, обработанного компаундом;
5. Введение в эксплуатацию отрегулированного участка системы необходимо производить не раньше, чем через 8 часов после завершения манипуляций по устранению дефектов. При температурных показателях ниже 0°С запуск системы можно производить только по прошествии суток.
www.fpipes.ru