Нанесение эмали: Нанесение и обжиг эмали | afgan-bazar.ru
Нанесение и обжиг эмали | afgan-bazar.ru
Емельянов А.Ю.
Нанесение и обжиг эмали
В этой статье рассматриваются аспекты процесса нанесения эмали на лицевую и обратную (контрэмаль) поверхность изделия перед обжигом, особенности обжига и сцепления эмали с металлом, фазы обжига эмалей.
Технологический процесс нанесения эмали.
Эмаль может наноситься на поверхность металла в виде порошка различными способами: насеиванием, напылением, в виде жидкого шликера, в виде мокрого порошка, ручным или машинным способом.
Однако, в случае перегородчатой эмали, целесообразнее всего наносить эмаль в виде порошка, смоченного водой с помощью шпателя. Эмаль закладывается в ячейки, образованные перегородками. Перед обжигом изделие необходимо тщательно просушить. Вследствие высокой вязкости эмали, обжиг изделий происходит, как правило, неоднократно, так как в слое эмалевого покрытия могут образовываться газовые пузыри, поры,недоливы и т.
Контрэмаль. При нанесении эмали только на одну сторону металлической пластины в системе металл – эмаль неизбежно возникают напряжения сжатия и растяжения, которые могут привести к деформации изделия и снижению прочности эмалевого покрытия вплоть до его разрушения.
Для предотвращения деформации эмалированных изделий (в случае эмалирования металлических пластин толщиной 1мм и менее) применяют покрытие эмалью с обеих сторон, для того, чтобы они испытывали одинаковые напряжения растяжения с обеих сторон и оставались бы устойчивыми к деформациям.
При изготовлении изделий в технике перегородчатой эмали, если перегородки ставятся только на одну сторону изделия, обратная сторону покрывается слоемконтрэмали.
Для изделий, обратная сторона которых остается невидимой, или несет второстепенное художественное значение, контрэмаль представляет собой смесь эмалей нескольких цветов. Кроме того, в состав контрэмали целесообразно добавлять смывки эмалей (мелкодисперсный осадок, образующийся при отмучивании эмалей). Это делается для того, чтобы сделать свойства контрэмали более универсальными. Контрэмаль содержит тонко измельченные фракции многих видов эмалей и, следовательно, объединяет в себе их свойства. Кроме того, это выгодно, так как позволяет использовать отходы и делает контрэмаль более пластичной.
В случае, если необходимо декорировать изделие с обеих сторон, перегородки устанавливают поочередно с обеих сторон, либо контрэмаль покрывается тонким слоем более легкоплавкой эмали для придания ей требуемого декоративного эффекта.
Обжиг и сцепление эмалей
После обжига изделий, покрытых эмалью, на металле получается прочно связанное с ним покрытие. Силу, которую необходимо применить для отрыва эмалевого слоя от поверхности металла, называют прочностью сцепления эмали с металлом. Практикой эмалирования, а также большим числом исследовательских работ установлена зависимость прочности сцепления от ряда факторов.
Обязательным условием для сцепления является хорошее смачивание поверхности металла эмалевым расплавом. Поверхность металла должна быть свободной от загрязнений любого характера. Поверхностное натяжение эмалевого расплава не должно быть слишком большим. Известно, что совершенно чистые, не окисленные поверхности стеклом не смачиваются. Для растекания грунта по металлу на поверхности последнего должна присутствовать тонкая пленка окисла. При обжиге грунта на предварительно не окисленной стали в восстановительной среде или в вакууме сцепление не достигается. Играет роль структура поверхности металла. На разрыхленной поверхности эмаль держится крепче, чем на гладкой.
Для развития сцепления большое значение имеет состав эмали, определяющий поверхностное натяжение и коэффициент термического расширения [1].
Фазы обжига эмали на медной подложке. При температурах от 700 до 900ºС эмалевый порошок, нанесенный на металл, взаимодействует с ним и образует гладкое блестящее прочно соединенное с металлом покрытие, причем эмаль размягчается в определенном интервале температур, а не при определенной температуре плавления. При нагреве изделия в печи от комнатной температуры до температуры обжига происходит оплавление эмали, которое можно подразделить на несколько фаз (см. рис в начале статьи [2] ).
1-я фаза. При загрузке образца в разогретую печь кислород воздуха беспрепятственно проникает через эмалевый порошок к поверхности металла и окисляет его. На поверхности металла (меди) образуется оксидный слой.
2-я фаза. Частицы эмали спекаются, но покрытие остается еще пористым, газопроницаемым. Окислы меди взаимодействуют на поверхности раздела со стеклообразующими компонентами эмали, особенно с B2O3 с образованием солей меди. В основном металле вследствие диффузии происходит внутреннее окисление: под слоем меди (CuO) образуется зона закиси меди (Cu 2O). Образование окислов меди приводит к некоторому сближению на поверхности раздела свойств таких различных материалов, как металл и эмаль.
3-я фаза. При дальнейшем нагревании пограничное поверхностное напряжение между все более размягчающейся эмалью и твердой медью снижается настолько, что эмаль растекается по поверхности металла, т.е. начинает «плавиться». Поры пекшейся эмали закрываются, образуется сплошное покрытие, поверхность которого пока еще остается неровной. Образовавшееся покрытие препятствует дальнейшему доступу кислорода к границе эмаль-металл.
4-я фаза. Изделие нагревается до температуры плавления эмали. Поверхностное натяжение уменьшается настолько, что поверхность эмалевого расплава становится гладкой, все неровности исчезают.
5-я фаза. Поверхность эмалевого покрытия должна быть раскаленной докрасна и иметь зеркальный блеск.
6-я фаза. Если оптимальная продолжительность обжига превышена, это приводит к дальнейшему взаимодействию между компонентами эмали и металла, причем изменяется цвет и прозрачность эмали, пограничный слой отходит от краев металла.
Читать еще о художественном эмалировании
Литература:
Эмалирование металлических изделий. Под ред. В.В. Варгина. Изд. 2-е, Л., 1972.
Э. Бреполь Художественное эмалирование Л. «Машиностроение» 1986 — 127 с.
Нанесение эмали
Для нанесения эмалевого покрытия на стальную подложку применяются следующие способы:
- напыление распылителем;
- погружение или поливка эмалевым шликером;
- нанесение кисточкой;
- насеивание.
Нанесение пистолетом-распылителем применяется для изделий большого формата. Наиболее распространенным методом является нанесение шликера окунанием или обливанием. Перед использованием шликер процеживается, чтобы удалить остатки гранул. Подложку окунают в шликер, который имеет густоту сметаны, и держат лист под таким наклоном, чтобы избыток шликера стекал с одного угла. Окунание применяют чаще всего для нанесения грунтовой эмали, причем надо следить за тем, чтобы металлические части покрывались со всех сторон.
Покровные эмали чаще всего наносятся обливанием. Этот метод предоставляет своеобразные художественные возможности, которые недоступны при использовании ювелирных эмалей. Лист устанавливается под наклоном и из черпака обливается шликером. При этом достигается равномерное распределение эмали, избыточная эмаль стекает. Мелкие детали обливают из ложки. Избыток шликера с краев листа удаляют руками.
Разнообразных эффектов в этой технике добиваются, регулируя текучесть шликера разными способами: можно варьировать зернистость эмали, добавлять в шликер воды, кроме того, можно влиять на процесс стекания посредством встряхивания листа. Если желаемое качество покрытия достигнуто, лист ставят на просушку. Большие окантованные листы устанавливают на трехгранные полосы, гладкие пластины—на подставки для обжига, описанные в Подставки для обжига эмали.
Нанесение грунтовой эмали. Металлическая подложка всегда с двух сторон покрывается черно-коричневой или иссиня черной грунтовой эмалью. Эта грунтовка всегда является началом работы по эмалированию стали.
Нанесение покровной эмали. На грунтовую эмаль наиболее часто наносят белую эмаль. Особенно хорошо зарекомендовали себя для художественного эмалирования стали белые эмали, заглушённые сурьмой. Чтобы получить высокую кроющую способность, можно глушить эмаль окисью олова. Сурьмяные эмали отличаются хорошей совместимостью с другими эмалевыми фриттами, кроме того, они при относительно высокой для стального эмалирования толщине слоя прочно сцепляются с грунтовой эмалью. Просвечивающая сквозь полу заглушённую белую эмаль грунтовая эмаль в зависимости от толщины слоя покровной эмали придает покрытию различные оттенки от серого до белого.
Припудриванием майоликовой эмалью белых грунтовых эмалей можно получить интересные цветовые эффекты. Можно наносить майоликовые эмали, ювелирные эмали или окрашенную красящими веществами прозрачную эмаль и получать живую структурированную поверхность.
Обязательным для всех случаев условием является наложение грунтового слоя белой эмали!
Нанесение рисунка по шаблону, как это практикуется при эмалировании табличек, предоставляет большие возможности. Шаблон накладывают на полностью просохший эмалевый слой. Не очень жесткой щеткой разрыхляется открытая эмалевая поверхность, затем эмаль удаляется мягкой кисточкой или сдувается. Просохшие эмалевые поверхности могут также прорезаться (прочерчиваться) деревянной палочкой и обрабатываться шабером по принципу техники графитти. При серийном изготовлении изделий рекомендуется нанесение эмали с помощью трафаретной печати.
Нанесение слоя фольги. При последнем обжиге в качестве особого художественного приема может применяться вплавление золотой и серебряной фольги. Технически это осуществляется точно так же, как описано в разделе Использование фольги в качестве подложки для эмали.
Похожие записи
Как осуществляется нанесение эмали на ювелирные изделия
Декорирование ювелирных изделий при помощи эмали – очень древняя технология. Ее использовали еще римляне и египтяне. За счет нанесения такого материала можно создавать очень красивые разноцветные украшения с оригинальным рисунком.
Ювелирная эмаль – это тип легкоплавкого стекла, которым можно покрывать различные металлы (серебро, золото). Состав такого материала многокомпонентный, в него входят диоксид кремния, борный ангидрид, оксиды титана и алюминия, свинца, цинка, щелочных металлов, фториды и так далее. Нанесение эмали – довольно сложная и потому дорогостоящая процедура. Покрывать ею можно серьги, кольца, браслеты, подвески, запонки и многое другое.
Все многообразие технологий нанесение эмали можно разделить на две группы: горячий и холодный способ. Первый – самый древний и наиболее сложный. При горячей обработке в муфельных печах изделие с нанесенным составом нагревают до 800 градусов, при этом цветное покрытие припекается к поверхности металла. После этого изделие шлифуется.
Сейчас большим спросом пользуется холодная эмаль. Ее еще именуют стеклопластиком.
Она бывает трех видов:
- Двухкомпонентная. Для получения смесь готовится в необходимых пропорциях, заливается на поверхность изделия. После определенного времени, состав твердеет при комнатных условиях.
- Теплоотверждаемая. Она не совсем холодная, но и не горячая, поскольку для ее получения нужна температура плавления до 160 градусов. Минус такой эмали – низкая прочность. На ней легко остаются царапины и вмятины, поэтому она не очень широко применяется.
- Светоотверждаемая.
Она немного напоминает фотополимерные пломбы, поскольку для отверждения такого покрытия используют облучение ультрафиолетовыми лампами. Покрытие получается достаточно прочным.
Особенности технологии двухкомпонентой эмали
Двухкомпонентные холодные эмали на эпоксидной основе находят широкое применение, поскольку их нанесение не вызывает сложностей. Этот процесс можно сравнить с работой художника, когда из красок разного цвета формируется рисунок. Изделие оставляется на 48 часов при комнатной температуре. Готовое покрытие похоже на керамику.
Для получения различных оттенков эмали можно смешивать между собой. Готовое покрытие не нуждается ни в какой финишной отделке и не требует применение дополнительного оборудования. Такие эмали можно наносить на любой металл.
УФ эмаль
В состав светоотверждаемой эмали входят такие компоненты:
- диметилакрилаты;
- керамика и другие неорганические компоненты;
- инициаторы для фотополимеризации;
- стабилизаторы для предотвращения выпадения осадка;
- пигменты для придания необходимого цвета.
Для нанесения эмали поверхность изделия не требует специфической подготовки, ее можно накладывать на любой металл. Большой плюс такого материала в том, что сколы или иные ее дефекты поддаются реставрации.
Как накладывается УФ эмаль
Технология получения покрытия такова:
- Чтобы эмаль лучше фиксировалась на поверхности, лучше, чтобы она была шероховатая. В этом случае минимизируется вероятность сдвига. Поверхность обезжиривается, просушивается.
- Небольшой объем эмали наносится на стеклянную плитку для перемешивания, в процессе соединения она нагревается до 80 градусов. При помощи специальной иглы (штанги) удаляются все пузырьки, частички пыли. Они просматриваются под увеличительным стеклом.
- На поверхность украшения наносится небольшой слой связующей основы, он высушивается в течение 5 минут. После него накладывается эмаль. Весь процесс не должен занимать более 1 часа. Покрытие еще раз проверяется на наличие пузырьков.
- Эмаль облучается УФ-лампой и отвержается.
Далее наносится состав слой за слоем с постоянной обработкой УФ-лампой.
Если необходимо удалить эмаль, то ее срезают либо выжигают. После полного отверждения покрытия его можно подвергать дальнейшей отделке: шлифовке, полированию, обработке в пескоструйных установках для придания матовости и зернистости. В случае высокого разрешения оборудования на поверхности допустима гравировка.
УФ-эмаль – это полимер, который не требует смешивания с отвердителем. Время облучения лампой определяется толщиной слоя и количеством пигмента, оно варьируется от 10 секунд до 10 минут. Слои можно наносить тонкими, без длительной выдержки, в отличие от двухкомпонентной эмали, поэтому цвет получается чистый, прозрачный.
Похожие статьи
[pt_view id=»971a14bn4p»]Сложности в нанесении термостойких эмалей
Термостойкие кремнийорганические эмали являются поистине уникальным материалом. они оптимально подходят для случаев, когда мы желаем получить высокую антикоррозионную защиту металла и покрытие, стойкое к воздействию высокой (до 750ºС) и низкой (–60ºС) температур, повышенной влажности воздуха и действия агрессивных сред.
Эти эмали считаются экономически выгодным материалом, так как, во-первых, имеют небольшой расход при нанесении, имея высокие показатели укрывистости: рекомендуемая толщина покрытия для изделий, подвергающихся воздействию высоких температур составляет всего 25-25 мкм.
Во-вторых, нанесение эмали не требует предварительного грунтования металла антикоррозионными грунтовками. в данном случае пристальное внимание следует уделить эмалям серебристого и серебристо-серого цвета. Они являются “фаворитами” антикоррозионной защиты среди кремнийорганических эмалей благодаря особенностям пигмента — алюминиевой пудры. Пластинчатая структура алюминиевой пудры создает высокую кроющую способность пигмента и защитный барьер покрытия к воздействию среды и коррозионно-активных агентов.
Однако при нанесении здесь есть свои нюансы.
Важным этапом перед нанесением эмали на металлическую поверхность служит обезжиривание и и очистка поверхности:
-
Обезжиривание производится ветошью, смоченной ксилолом, толуолом либо одним из “номерных растворителей” марок Р-4, Р-5, 646.
Перед нанесением эмали поверхность необходимо высушить при температуре 20°C .
-
Очистка от ржавчины, прокатной окалины, слоев старой краски производится до степени 2 по ГОСТ 9.402-2004 (табл.9) или степени Sа2– Sа2,5 по ГОСТ Р ИСО 8501-1:2014.
В случае невозможности произвести абразивоструйную обработку на объекте допускается очистка поверхности металла до степени St 3 по ГОСТ Р ИСО 8501-1-2014 механизированным инструментом. После очистки поверхности абразивоструйным методом обезжиривание не производится.
Подготовленная поверхность должна быть окрашена в течение 6 часов при хранении на открытом воздухе и в течение 24 часов при работе внутри помещения. Подобные цифры считаются весьма усредненными, главное, чтобы за время, прошедшее между обезжириванием и очисткой, поверхность должна оставаться чистой и сухой.
Получить требуемую термостойкость и адгезию возможно только при неукоснительном исполнении подготовки поверхности.
Термостойкие эмали благодаря своему уникальному составу могут наноситься при температуре окружающего воздуха и подложки от -30°С до +40°С.
Металлоконструкции окрашиваются не менее чем в 2 слоя «мокрый по мокрому» с промежуточной выдержкой в течение 5-7 мин. при температуре (20±2)ºС. Второй слой эмали сушат при температуре (150±2)ºС в течение 30 мин или при температуре (20±2)ºС в течение 2 ч.
Допускается сушка обоих слоев и при “комнатной” температуре и даже в уличных условиях, но само назначение эмалей как термостойких покрытий указывает, что наибольший эффект от окрашивания данными эмалями достигается при “горячей” сушке, так как в таком случае эмаль как бы “запекается” и лучше схватывается с поверхностью.
При окрашивании оборудования, которое будет работать при температуре выше 100°C и (или) в условиях агрессивной среды (бензин, солевой туман, минеральное масло) обязательным условием является постепенный нагрев оборудования до температуры эксплуатации — таким образом происходит горячее отверждение покрытия.
Для этого нанесенное покрытие выдерживается около 1 часа при температуре (20±2)ºС, далее производится подъем температуры до температуры эксплуатации со скоростью не более 5°C в минуту и затем при данной температуре выдерживается не менее 3 часов.
Толщина покрытия по сухому слою на поверхностях, эксплуатируемых в условиях повышенных температур от 100°C до 750°C должна составлять 25-35 мкм.
При эксплуатации покрытия в атмосферных условиях при повышенной влажности и при температуре до 100°C сушка финишного слоя до степени 3 составляет 2 часа при 20°C. Рекомендуемая толщина покрытия по сухому слою в этом случае может составлять 50-100 мкм. Покрытие набирает оптимальные свойства при выдержке 72 часа при температуре (20±2)ºС. После этого возможна транспортировка и монтаж окрашенных изделий.
Теоретический расход эмали на покрытие толщиной по сухому слою 25-35 мкм составляет 100-120 г/м².
При окрашивании термостойкими эмалями строительных поверхностей возникает сложность с тем, что происходит увеличение расхода эмали, так как подобные материалы обладают большей впитываемостью.
Решить эту проблему можно либо увеличением количества слоев эмали с двух до трех: в таком случае первый слой идет в качестве пропитки, второй — грунтовки, и лишь третий — в качестве финишного покрытия.
Теоретический расход эмали при таком раскладе при толщине 60-80 мкм по сухой пленке будет составлять свыше 450 г/м².
Либо на окрашиваемую поверхность предварительно наносится лак КО-85, в качестве пропитывающего материала, и только затем поверхность окрашивается в 2 слоя эмалью. Такой подход выгоден в случаях, когда цена на лак оказывается ниже цены на эмаль.
Фактический расход эмали может значительно отличаться от теоретического и зависит от характера окрашиваемой поверхности, от ее конфигурации и пористости, метода нанесения и др .
Важно помнить, что испарения, образующиеся при высыхании являются высокотоксичными, что обуславливает ужесточение мер безопасности во время и после нанесения эмалей.
Другие публикации
Эпоксидные грунтовки – ЛКМ на основе эпоксидных смол (ЭС).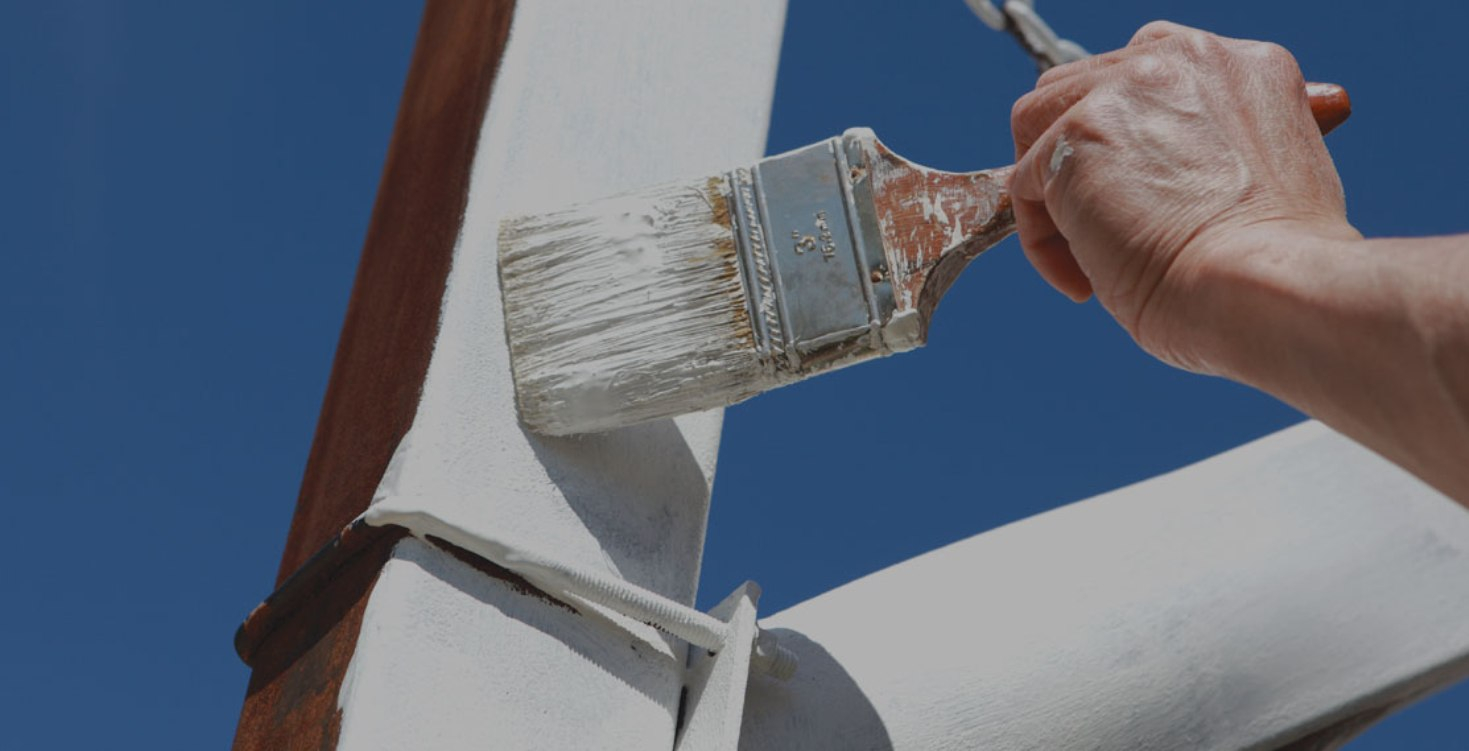
17.05.2021
Эпоксидные грунтовки – ЛКМ на основе эпоксидных смол (ЭС).
Эпоксиэфирные грунтовки21.04.2021
Термостойкая и антикоррозионная эмаль “SHIHRAN”20.12.2019
Высококачественная кремнийорганическая эмаль, обладающая термостойкостью до 900°С
ЛКМ для поверхностей из металла и бетона в банках18.11.2019
Баночная продукция НПФ «Эмаль»
Зимний преобразователь ржавчины25.10.2019
Преобразователь ржавчины «НЕНС» для защиты металлических изделий от коррозии и с возможностью нанесения при минусовых температурах
Термостойкие ЛКМ с электроизоляционными свойствами20.08.2019
О материалах с повышенной термостойкостью и электроизоляционными свойствами
Эпоксидные эмали и лаки19.08.2019
Преимущества, особенности, виды
Термостойкая эмаль КО-810129.05.2019
Антикоррозионная эмаль с термостойкостью до 600 градусов
Грунтовки по металлу29.05.2019
Грунтовки по металлу в качестве первого этапа антикоррозионной защиты поверхности
Грунт-эмаль по ржавчине ХВ-0278 29. 05.2019
Защитная грунт-эмаль по ржавчине от компании ООО НПФ ЭМАЛЬ
Технология нанесения горячих и холодных эмалей. Эксперимент-фотоочет.
Вот, как и обещала небольшой рассказ о эмалях. Сборная информация из статей в интернете и свои ощущения. Извините, что так не скоро… были технические затруднения с опытами.
Классический способ — эмаль горячего отжига:
Эмаль (не путать с эмалевыми красками) — тонкое стекловидное покрытие, получаемое высокотемпературной обработкой.
В художественной керамике эмалями иногда называют непрозрачные (глухие), обычно белые, блестящие глазури за их свойство перекрывать цвет керамического черепка.
В переносном смысле эмалями нередко называют практически все стекловидные покрытия по металлам, используемые в бытовых целях (эмалированная посуда, ванна и т. д.).
В Россию эмаль пришла из Византии одновременно с принятием христианства и уже в XII веке упоминается в летописях. Современная художественная эмаль пришла в Россию из Европы в конце XX века.
Первое упоминание о Русских перегородчатых и выемчатых эмалях встречается в Московской Ипатьевской Летописи 1175 года. В те времена все виды Русских художественных эмалей назывались «финифть» и только в XIX веке старинное название «финифть», сменилось на новый термин «эмаль». Эмаль представляет собой стекловидный порошок, получаемый измельчением стекловидных пластин до необходимой фракции. Измельченная в порошок эмаль смачивается водой до нужной консистенции и наносится в ячейки. Работа обжигается в печи или производится локальный обжиг эмали в каждой ячейке посредством газовой или бензиновой горелки. Разные виды и цвета эмали требуют и разную температуру обжига, которая колеблется в диапазоне от 700 до 900 градусов по Цельсию. После обжига, порошок эмали сплавляется в цветной стекловидный слой, в зависимости от типа эмали: прозрачный, или так называемый «глухой» — цветной непрозрачный слой эмали. Во время обжига эмалевый слой подвергается усадке, будучи насыпан до обжига по верхний край перегородки, он «опускается», становится ниже перегородки. Для полного заполнения ячейки, поэтому требуется неоднократный обжиг и пополнение обжигаемой эмали в ячейке. В зависимости от сложности композиции и задач, стоящих перед мастером, работа подвергается от 5 до ста обжигам. Мастер не имеет возможности вмешиваться во взаимодействие эмали и высокой температуры, он может лишь основываясь на опыте и интуиции регулировать время и температуру обжига. Именно это и формирует уникальность каждого произведения из эмали, повторить его не в силах даже автор. Каждое произведение существует лишь в одном экземпляре, оно уникально. В последние десятилетия ХХ века техника горячей эмали вышла за рамки традиционного круга своего применения. Соединяя в себе ювелирную драгоценность материала со свободой станковой живописи, этот вид искусства не имеет широкого распространения и является элитарным. Горячая эмаль сочетает в себе много различных техник и способов обработки, как металла, так и самой эмали, дающих возможность разнообразных решений, как декоративных, так и сложно-живописных.
Ручной способ наложения эмали заключается в следующем: размолотую эмаль размешивают с водой и в виде кашицы накладывают на изделие при помощи кистей или специального инструмента — узкого металлического шпателя. Для разравнивания слоя эмали изделие слегка встряхивают. Ручной способ обычно применяют при наложении эмали на небольшие поверхности сложных конфигураций и профилей, например, в ювелирном деле. Работу выполняют в следующем порядке.
Влажной кистью берут немного эмали из фарфоровой чашечки, наносят на металл и там ее распределяют. Степень влажности зависит от рода работы. Если эмаль слишком сырая, то добавляют немного эмалевого порошка; если она сухая, то добавляют немного воды — иначе ее не нанесешь на изделие.
Хорошо делать поверхность основы шероховатой, так как при этом повышается прочность сцепления металла и эмалей. Медь служит прекрасной основой для эмали, так как обладает благоприятными соотношениями теплового расширения и отличается высокой точкой плавления. Однако медь имеет ничтожную светящуюся силу, и некоторые эмали, светящиеся на золоте или серебре очень ярко, на меди выглядят темными и грязными. Томпак (медный сплав с цинком), на котором эмаль хорошо держится, имеет большую световую силу, чем медь.
Обжиг эмали требует температуры нагрева 600— 800°. Для этого лучше всего применять электрические печи с открытыми спиралями. Такие печи очень производительны и экономичны. Мелкие ювелирные изделия помещают в обычные электрические муфели лабораторного типа с закрытой обмоткой. Для обжига эмали можно пользоваться газовым пламенем, и другими источниками тепла. Однако во всех случаях пламя не должно соприкасаться с эмалевой поверхностью, так как копоть, попадая в эмаль, может испортить изделие. Поэтому обычно при нагреве открытое пламя направляют на оборотную левую сторону изделия. Каждый предмет, который обжигают в печи, необходимо класть на специальную подставку, от качества которой во многом зависит успех обжига.
Отделка заканчивается отбеливанием металлических частей изделия (свободных от эмалевого слоя), которые в результате обжига покрываются окисями. Отбеливание производят в слабом растворе серной кислоты (не выше 15%), так как некоторые эмали нестойкие к кислотам, могут потускнеть и потерять яркость и блеск. В прошлом для отбеливания эмалей с большим содержанием свинца применяли органические вещества, не действующие на эмаль (квас, клюкву и др.).
Опыт: опыту подверглись несколько предметов, самым наглядным оказался вот этот крестик. В ближайшее время добуду еще пластики (а конкретно хочу именно створку складня), и опыт повторю. т.к. здесь конечно результат не очень, но реш
ила показать пока так, суть ясна.
Берем сухой готовый порошок эмали синего цвета, и разводим его водой:
Берем крестик, и конечно нужно было взять штихеля, и вручную, аккуратно, прорезать канавки, но особенная аккуратность не перследовалась. Я просто взяла бор машинку с жестким абразивным диском, и обработала поверхность, а потом бором «выбрала» все канавки. Извините, что так топорно. Но был бы крестик в состоянии чуть получше, то может и запарилась бы. … В выемки закладываем эмаль. Лучше не торопится, и дать выпарится влаге самостоятельно, но можно и подогреть немного изделие, но очень аккуратно. Если сразу начинать интенсивно греть, то вода закипит, и в последствие эмаль ляжет не ровно.
После выпаривания воды, начинаем греть газовой горелкой. Подробно процесс не сфотографирован, всвязи с техникой безопасности и наличием всего 2 рук).
Держа крестик пинцетом за ушко, нагрев ведется с обратной стороны изделия, дабы копоть не оседала на эмали. Крестик маленький и тонкий — греть пришлось недолго. Эмаль расплавилась и сильно осела. После остывания на воздухе (резко остужать нельзя, иначе эмаль растрескается) накладываем второй слой. И процедура повторяется. Таких слоев может быть очень много, в зависимости от глубины наших канавок. В данном случае двух слоев вполне хватило.
После нагревания металл окислился. Можно оставить как есть, если не появилось каких-либо пятен и т. д… но я решила что этот образец можно и добить, отполировав его…
Современный метод. Холодные эмали (синтетические):
Жидкие двухкомпонентные эмали используются для проведения декоративных работ путем нанесения на поверхность цветных и драгоценных металлов. При смешивании 10 частей эмали и 4 частей катализатора (пропорция 2,5 : 1) смесь прочно закрепляется при комнатной температуре в течение 48 часов, при температуре 100 С — за 45 минут, и выглядит как керамическое покрытие. Для получения различных цветов и оттенков эмали различного цвета могут смешиваться.
У каждого вида эмали есть свои достоинства и недостатки, и ниже мы попытаемся их вкратце перечислить. К достоинствам эпоксидных и фотоотверждающих «холодных» эмалей можно отнести простоту и технологичность их применения. Они практически не требуется оборудования, а также специфической подготовки поверхности изделия. Отлично закладываются на любые сплавы не только золота, но даже и на не металлические поверхности. Требуют минимальных профессиональных навыков от мастера, сроки обучения технике закладки таких эмалей исчисляются днями — неделями. Эти эмали, как правило, пластичны и редко скалываются, обладают хорошей ремонтопригодностью. Дефекты и сколы появляющиеся со временем на таких эмалевых покрытиях достаточно легко устраняются.
Из недостатков «холодных» эмалей следует отметить их подчас невысокие декоративные свойства – ощущение пластмассы, а также низкая твердость.
Низкая твердость «холодных» эмалей со временем приводит к потускнению, первоначально блестящего, эмалевого покрытия.
На наш взгляд применение этих эмалей вполне оправдано в бижутерии и дешевых ювелирных изделиях массового производства, но в дорогих, эксклюзивных золотых украшениях, несомненно, более достойно выглядит благородная «горячая» ювелирная эмаль.
Изделия с холодной эмалью могут быть покрыты полимерной смолой для предохранения эмали от царапин и в декоративных целях.
Опыт: опыту подверглась створочка складня.
Поверхность предварительно была вымыта щеткой с мылом. Углубления, предназначенные для эмали, зачищены шабером и нанесены риски, для большей поверхности соединения металла с эмалью. Поверхность обезжирена.
Просчитана пропорция компонентов, компоненты взвешены, и соединены. Запаха практически никакого нет (если принюхаться, то пахнет чем-то полиэтеленовым). По виду и консистенции напоминает акриловую краску. Легоко наносится, и легко убираются излишки. Высыхает в течении 48 часов, так что времени на работу предостаточно. К сожалению цвет выбрала темноватый. плохо видно саму эмаль на снимках.
Начинаем иголочкой наносить…
Ну вот! работа окончена!
После высыхания: На вид и восприятие тактильное — выглядит, как настоящая эмаль. К сожалению, иголкой царапается .
Выводы:
В целом мне очень понравилась «холодная эмаль». не портит изделие (его не надо греть, ее всегда можно удалить), проста в наложении, не требует сложного доп. материала и умений. Очень легко смешиваются цвета, получить можно любой оттенок, т.к. смешиваешь только основные компоненты, а когда получаешь нужный цвет — уже добавляешь отвердитель. можно использовать 2 цвета одновременно и они практически не будут смешиваться в изделие (нужно только их замешать с интервалом в полчаса). Но для устойчивости рекомендую покрывать сверху специальным лаком.
Горячая эмаль конечно лучше смотрится, не царапается, лучше блестит… но изделие после наложения такой эмали выглядит «новым». Можно патинировать и прочее, но это уже отдельная история. Более трудоемкая и непредсказуемо могут себя повести при нагревании различные изделия, особенно, если металл в «усталом» (как у меня на образце) состоянии.
Ну что, продолжим? Вот попробовала более крупную деталь и с эмалями разного цвета.
Вывод:
1. разноцветные эмали совершенно разные по свойствам, по температуре плавления.
2. и еще… это изменение цвета эмали. У меня был желтенький порошек, (симпотичненький цвет — см. фото «ДО» и «после») но когда эмаль остыла, то стала грязно-зеленая… не красивая. И расплавилась как-то плохо, хотя образец нагрела целиком до красна. Синяя и белая, прямо очень хорошо растеклись, а желтая так и осталась бякой какой-то. Больше не буду ее использовать. Может сама эмаль такая попалась. Если делать чистовую и ответственную работу, эмали надо проверять на образцах.
3. минимум два слоя требуется для нанесения. Первый слой сколько не пробовала, корявый какой-то, а второй очень даже гуд.
Выбор образца, зачистка лунок:
Нанесение эмали-порошка:
После прогрева:
Шлифовка бормашинкой с резиновым кругом:
Вот, очередной эксперимент.
Берем обломок средника. Ну, или то, что от него осталось. Анализируем возможности.
Прокаливаем и удаляем старую эмаль. Она совершенно никакого вида. В принципе, я когда прокалила — старая эмаль, там, где сохранилась получше расплавилась и растеклась заново. Предполагаю, что если вещь с частично своими эмалями (вполне устраивающими) их можно легко оставить, и просто довести новые, а старые практически не изменятся (но это если эмаль не сыпится как порошок).
Спиливаем петельки и выравниваем обломанный верхний край. К сожалению, она сильно деформирована, и свести трещину не удалось. При сведении трещины сама плашка становится сильно выпуклой. Это просто уже произошла деформация (растяжение). Возможно и можно было как-то свести, но у меня не получилось.
А дальше все, как обычно: накладываем эмаль, сушим и отжигаем первый слой эмали.
Далее на нашу трещину, снизу, подпаиваю медную пластинку. Полученную выемку буду заполнять эмалью, вместе со вторым и третим слоем основной эмали.
Конечно я надеялась залить трещину припоем, но очень уж большая трещина, и нет возможности грамотно обработать трещину. Решила заливать, как есть.
К сожалению промежуточные фотографии этого этапа мистически пропали, но принцип тот же.
После залития эмалью подложку аккуратно сняла, конечно эмаль очень хрупкая, и мне пришлось прибегнуть к хитрости. Участок трещины «горло святого» — все равно эмалью не зальешь, и его нужно было как-то восстанавливать. Тут на помощь пришла «холодная сварка — супер бронза». Ею я замазала трещину, и сделала усиление по всей обратке. С обратки — не красиво, но что сделаешь. Плашка предполагается для оформления в деревянную раму. Эта эпоксидка хорошо застыла, дав жесткость всей конструкции, она отлично обрабатывается и полируется. Вид у нее не бронзовый немного, но для заделывания мелких дефектов, я считаю, очень подходит. В целом участок «горла» получился очень неплохо. Фото конечно всего не передает.
В результате аж 5 полных прогреваний плашки, на поверхности образовался достаточно приличный окисел. Мною было принято решение шлифовки и полировки. Все равно изделие на вид «новое». Но через год, стоя на полке — оно наберет уже постепенно патинку, можно ускорить процесс в парах аммиака (сейчас не хочу возиться). Пусть стоит так, в питерском климате быстро потемнеет.
Я считаю, что это стала вполне самостоятельная вещь, имеющая право на жизнь! Вскоре она получит деревянную рамку (под размер — сама вырежу) займет достойное место, и будет служить мне по прямому назначению.
Простите за последние фото, но полированные вещи очень сложно снимать (а возиться с фотиком сейчас некогда). Спасибо всем за внимание.
По материалам интернет-форума piterklad.ru:
http://piterklad.ru/viewtopic.php?t=14888&highlight=
Нанесение эмали ХВ-518 защитной: проблемы и особенности.
Почему военную технику окрашивают эмалью ХВ-518? Это связано с целым рядом достоинств данного материала:
1. В первую очередь малое время высыхания – до степени 3 эмаль должна высыхать не более 4 часов (фактически – в пределах часа – полутора).
2. Второе преимущество – высокая укрывистость, особенно для эмалей защитного цвета – не более 80 г/м2 (фактическая укрывистость находится в пределах 50-60 г м2).
3. Также стоит упомянуть высокие физико-механические свойства эмали, такие как адгезия, твердость пленки эмали, эластичность при изгибе и прочность покрытия при ударном воздействии.
С какими особенностями может столкнуться потребитель при использовании эмали ХВ-518?
Цвет покрытия эмали.
Таких нюансов несколько, и первый из них – это цвет покрытия эмали. Как бы это странно ни казалось, но понятие «защитный цвет» включает в себя множество оттенков от почти песочного до болотного темно-зеленого. Мы производим эмаль ХВ-518 по 13-ти эталонам цвета, согласованным с конкретными потребителями.
Поэтому, заказывая у изготовителя эмаль ХВ-518 защитную, потребитель должен четко представлять, какого защитного цвета будет «его» эмаль. Во избежание недоразумений, связанных с отклонениями покрытия эмали по цвету, потребитель должен либо иметь свой собственный эталон цвета, согласованный и подписанный обеими сторонами (производителем и потребителем), либо определиться, по какому из уже имеющихся у производителя эталонов цвета производить заказ эмали. Причем желательно, чтобы выбранный потребителем при заказе эмали эталон цвета был зафиксирован документально. Если для потребителя разрабатывался конкретный эталон цвета эмали, то подписанные обеими сторонами экземпляры эталона цвета должны находиться как у производителя эмали, так и у потребителя.
Внешний вид покрытия эмали.
Второй момент, с которым периодически приходится сталкиваться потребителю – неудовлетворительный внешний вид покрытия.
Причин здесь может быть две:
1. Неправильная подготовка поверхности под окраску (в первую очередь — отсутствие обезжиривания, обеспыливания), и ошибки при подготовке лакокрасочного материала (неправильно подобранный растворитель для разбавления эмали до рабочей вязкости, либо неправильно подобранная рабочая вязкость материала – слишком высокая, или наоборот, низкая). Для разбавления эмали перед нанесением используется растворитель Р-4.
2. Ошибки при нанесении эмали на окрашиваемую поверхность (неправильно подобранное давление в краскопульте или при выборе диаметра сопла, а также неверно выбранное расстояние от краскопульта до окрашиваемой поверхности).
По вопросу подготовки поверхности можем адресовать к ГОСТ Р ИСО 8501-1-2014 «Подготовка стальной поверхности перед нанесением лакокрасочных материалов и относящихся к ним продуктов. Визуальная оценка чистоты поверхности». Согласно требованиям этого ГОСТ, степень чистоты поверхности при абразивной струйной очистке должна быть не ниже Sa2, при ручной механической очистке – не ниже St2.
Избыточное давление в краскопульте, как и малое расстояние от краскопульта до окрашиваемой поверхности приводит к нанесению эмали чрезмерно толстым слоем и, как следствие, образованию потеков и перерасходу материала.
При избыточном расстоянии от краскопульта до поверхности эмаль, вылетает из сопла в виде капель в потоке воздуха. Однако в процессе преодоления этого расстояния она теряет значительное количество растворителя (который банально испаряется) и долетает до поверхности уже не в виде капель жидкости, а почти высохшими сгустками, которые прилипают к поверхности, не растекаясь и не образуя сплошного однородного покрытия. Такой дефект лакокрасочники называют «переопылом». Эти засохшие и непрочно держащиеся на поверхности частицы краски и дают видимость белесости покрытия, так называемого эффекта «меления».
Эксплуатация покрытия эмали ХВ-518.
И, наконец, последний типичный и наиболее распространенный момент, с которой сталкивается потребитель, связана с эксплуатацией уже нанесенного и сформированного покрытия на основе эмали ХВ-518. Покрытие, подвергшееся воздействию осадков, меняет свой цвет – становится белесым, на нем выступают пятна, разводы. Причиной этого, вероятнее всего, является несоответствие эмали требованиям одного из показателей нормативной документации – «Стойкость к статическому воздействию воды». Производитель эмали при разработке и изготовлении эмали обязан проводить проверку материала на соответствие данному показателю и обеспечивать стойкость покрытия эмали к воздействию воды в течение 24 ч.
Испытания эмали ХВ-518.
Рассмотрим пример испытания эмали ХВ-518 производства ООО ПО «Химтэк-Яр».
Для проверки соответствия цвета необходимо нанести пневмораспылением предварительно разбавленную до рабочей вязкости (18-22 с) эмаль
ХВ-518 на металлическую пластинку и оставлить ее на высыхание в наклонном положении в течение 4 часов при температуре (20±2)°С. По истечении 4 часов сравнить полученное покрытие с требуемым эталоном цвета.
Следует отметить, что способ нанесения эмали существенно влияем на цвет покрытия. Эта разница заметна при сравнении двух выкрасов эмали ХВ-518, нанесенных разными способами – пневмораспылением и наливом. Для проверки цвета покрытия при входном контроле эмаль следует наносить методом пневматического распыления.
Разумеется, кроме соответствия цвета и внешнего вида покрытия эмали эталону, проверяются такие показатели как:
· условная вязкость по вискозиметру ВЗ-246 с дивметром сопла 4 мм при температуре (20±0,5) оС – 20-40 с;
· массовая доля нелетучих веществ – 24-34%
· время высыхания покрытия до степени 3 при температуре (20±2) оС – не более 4 часов;
· укрывистость высушенной пленки – не более 80 г/м2;
а также физико-механические свойства покрытия эмали ХВ-518:
· адгезия покрытия – не более 2 баллов;
· твердость пленки эмали по прибору типа ТМЛ – не
менее 0,09 отн. ед.;
· эластичность пленки при изгибе – не более 1 мм;
· прочность пленки при ударе – не более 50 см.
Эмаль ХВ-518 защитная производства ООО ПО «Химтэк-Яр» соответствует всем перечисленным требованиям.
Для испытания стойкости покрытия эмали ХВ-518 к статическому воздействию воды металлическая пластинка с заранее нанесенным покрытием эмали помещается в емкость с дистиллированной водой на 24 часа. Спустя указанное время пластинка с нанесенной на нее эмалью извлекается, высушивается при температуре 20 оС в течение 2 часов. После этого производим визуальный осмотр пластинки. Покрытие эмали должно быть без изменений, при этом допускается незначительное посветление пленки. Для эмали ХВ-518 защитная производства ООО ПО «Химтэк-Яр» визуальное различие в цвете исходного покрытия и покрытия, подвергшегося воздействию воды практически отсутствует.
При проверке покрытия эмали на спектрофотометре «Пульсар» в соответствии с ГОСТ Р 52662-2006 «Материалы лакокрасочные. Колориметрия. Измерение цвета» было установлено, что полное цветовое различие ∆Е исходного покрытия и покрытия, подвергшегося воздействию воды составляет 0,3. Т.е. различие в цвете для покрытия, подвергшегося воздействию воды и исходного покрытия практически неотличимо человеческим глазом.
Таким образом, эмаль ХВ-518 защитная производства ООО ПО «Химтэк-Яр» соответствует требованиям нормативной документации.
Вместе с этим читают:
Типичные проблемы потребителей при использовании ЛКМ (на примере ПФ-115, ХВ-16)
Дефекты лакокрасочного покрытия.
Нанесение эмали на медали, знаки, значки
Технология нанесения эмали на изделия из металла уходит корнями в седую древность. Многие века насчитывает использование таких способов нанесения как финифть или техника перегородчатой эмали, которые благополучно дожили до наших дней и сегодня успешно применяются при изготовлении медалей, знаков, значков и ювелирных изделий
Виды эмали и технологии нанесения
Технология нанесения эмали на знаки и другие изделия в каждом конкретном случае своя.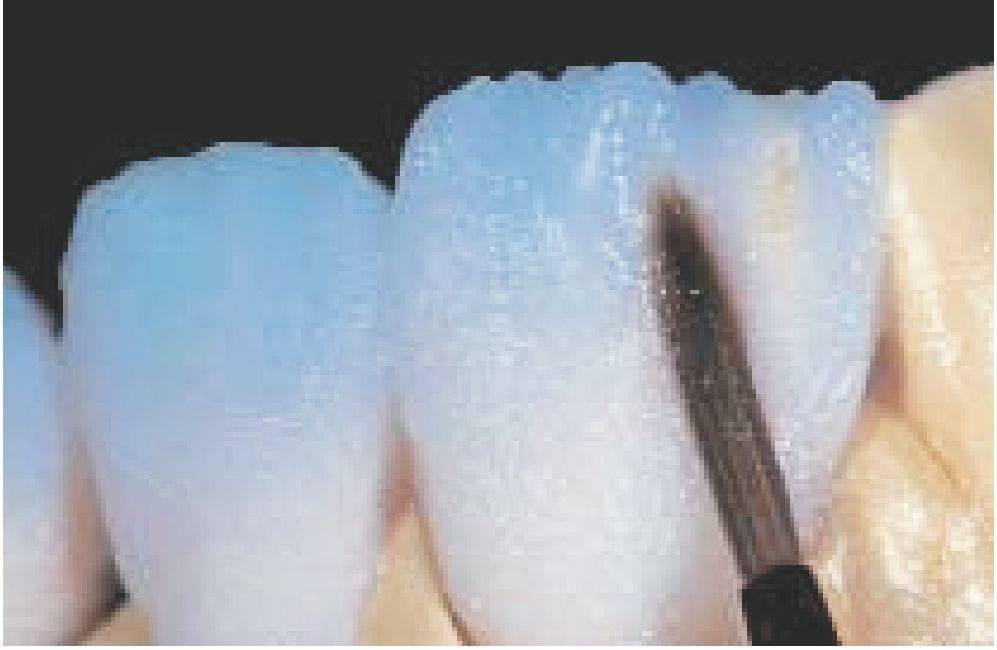
- Холодные (жидкие / мягкие) эмали
- Полиэпола
- Эпола
- Клуазон (горячая эмаль)
Холодная эмаль для ювелирных изделий, медалей и знаков
Чаще всего из-за доступности и простоты применения используют холодные эмали (их еще называют мягкими эмалями). Технология нанесения холодных эмалей проста: их заливают тонким слоем в различные, отделенные друг от друга перегородками детали рельефа изделия, а затем подсушивают при невысокой температуре. Часто, для того чтобы придать изделию дополнительный объем и выразительность, а также защитить его от царапин и повреждений, поверх холодных эмалей наносят эпоксидную смолу.Полиэпола
Еще одна технология украшения эмалью — полиэпола. Фактически полиэпола представляет собой ту же холодную эмаль, но за счет густой консистенции наносится на изделие более толстым слоем, заполняя детали рельефа почти на всю высоту их перегородок.
Эпола
Эмаль на основе эпоксидной смолы, обладающая еще более густой консистенцией. Ее в углубления изделия не заливают, а втирают специальным шпателем. После нанесения эмали изделие сушат в печи, а затем полируют, чтобы поверхность его выступающих металлических перегородок полностью сровнялась с поверхностью эмали.Ювелирные горячие эмали: клуазон
Такую же ровную поверхность на готовом изделии обеспечивает и нанесение эмали горячей. Из всех технологий нанесения эмали клуазон — самая древняя, красивая и дорогостоящая. Именно изделия горячей эмали имеют наиболее глубокие и богатые оттенки цвета. Технику горячих эмалей чаще всего используют при изготовлении государственных наград.Холодная и горячая эмаль: различия
В основе горячих эмалей типа клуазон — натуральные силикатные пасты на основе кварцевого песка. Подобно эполе такие пасты затираются в углубления изделия, заполняя их на всю высоту перегородок. При обжиге клуазон расплавляется и заполняет углубления рельефа изделия на всю высоту перегородок.
Высокая себестоимость медалей, знаков и значков с горячей эмалью объясняется не только тем, что каждый цвет клуазона обжигается отдельно. Также из всех способов нанесения эмалей — клуазон самый кропотливый и непредсказуемый, так как она часто трескается при обжиге и дает самый высокий процент брака среди всех технологий нанесения эмали.
Недостаток — это достоинство
Даже на идеальном изделии с нанесением горячей ювелирной эмали после обжига часто остаются небольшие царапины и трещины. Их наличие не является дефектом и даже напротив, высоко ценится у знатоков, красноречиво доказывая, что клуазон на данном изделии подлинный.При производстве медалей, знаков, сувенирной и наградной атрибутики, компания «Фабрика Наград» использует любые известные технологии нанесения эмали.
Нанесение эмали En Plein
Нанесение эмали En Plein
За 30 лет работы по эмалированию и созданию предметов искусства и ювелирных изделий я обнаружил много полезной информации, а также дезинформации относительно нанесения эмали en Plein. По мере того как многие секреты прошлого исчезают, преобладает дезинформация. Время Карла Фаберже представляет собой эпоху эмалирования, практически не имеющую себе равных с середины 18 века. В странах Европы, таких как Швейцария, Германия, Франция и Австрия, если не упоминать, были величайшие из когда-либо известных ювелиров и эмальеров.Примеры работ великих художников, таких как Жозеф-Этьен Блерзи, Мельхиор-Рене Барре, Фридрих Фирвальд, Дж. Г. Шарфф и Кирстенштейн, можно увидеть в книге А. К. Сноумена «Золотые ящики Европы восемнадцатого века», Фабер и Фабер. Согласно тексту Снеговика, «термин en plein означает, что эмаль была нанесена непосредственно на корпус шкатулки, а не на панели (плакетки), нанесенные на более позднем этапе». Разница в качестве мастеров и большей части выполняемой сегодня работы заключается в нанесении и подготовке поверхности к эмалированию.После этого все зависит от температуры и продолжительности.
- Настройка поперечного хода для прямой машины.
Эмаль обычно закупается в гранулированном виде. Гранулированная форма называется фриттой. Фритту можно приобрести с разной степенью измельчения или сита, от 60 до 200 меш. Оксид окраски имеет мало общего со способом нанесения на некоторые эмали, но не на все.
Самая большая проблема, с которой сталкивается эмалист, — это кислород.Металлы при нагревании до определенных температур при контакте с кислородом окисляются. Количество кислорода, присутствующего между поверхностью металла и основой эмали, а также время, необходимое для расплавления эмали, определяют степень окисления металла. Чем меньше окисления, тем чище и точнее цвет эмали. Таким образом, повторяемость результатов заключается в том, что чем тоньше покрытие, тем лучше.
- Проверка вертикального выравнивания фрезы по отношению к панели.
Посещая великие музеи Европы, я всегда стараюсь посетить великие коллекции ювелиров. Следует отметить следующие коллекции: Дворец Питти во Флоренции, Виктория и Альберт в Лондоне, Коллекция Фрика в Нью-Йорке, Метрополитен-музей в Нью-Йорке, Лувр в Париже, а также многие другие замечательные коллекции, которые у меня есть. не посещал. Наблюдение за великим искусством жизненно важно для образования любого художника. Я узнал, что худоба является фактором приложения во время посещения Лувра.Я ездил в Париж специально, чтобы увидеть их великое собрание табакерок 18 века из золота, эмали и драгоценных камней. Все работы на выставке были строго сдержаны. Эмали были преимущественно тонкими, но при этом имели интенсивную насыщенность цвета и чистоту. В большинстве случаев для достижения глубокого цвета требуется более толстый слой; однако в данном случае это определенно не соответствовало действительности. Под толстым я подразумеваю все, что больше 5-8 тысячных дюйма. Часто эмаль составляет около 20 тысячных.
- Выполняется первая серия рисунка гребешка.
Я предлагаю отшлифовать эмаль до размера не менее 200 меш для розового и красного цветов при нанесении на всю поверхность, которая была гильоширована для этой цели. Эмаль следует смешать с полуденатурированным спиртом и водой. Я использую 10% Klyr Fire ™ и водный раствор от Thompson Enamel, если поверхность имеет куполообразную форму. Нанести кистью, высушить и быстро обжечь при температуре, соответствующей используемой эмали.
- Измерение для размещения отверстий под орнамент.
Улавливание кислорода: может помочь следующая аналогия. Допустим, вы идете по каменистому пляжу, окруженному множеством огромных валунов, и наталкиваетесь на два огромных валуна, прислонившихся друг к другу. Проем настолько велик, что через него можно пройти. В таком случае представьте, сколько кислорода находится в отверстии. Теперь представьте, что вы идете между двумя песчинками, это невозможно, но теперь представьте, насколько меньше кислорода между песчинками, чем между двумя огромными валунами. Думайте о зернах эмали как о валунах и песчинках, и вы начнете понимать.Чем меньше кислорода, тем лучше. Еще одно преимущество — время для стрельбы. Тонкий слой эмали загорится намного быстрее, чем толстый слой крупных кристаллов, что решает проблему продолжительности. Этот метод потребует практики.
- Нанесение встречной эмали методом просеивания.
Промывка эмали важна. После шлифовки слейте молочную воду и дайте эмали отстояться в течение 2–3 минут. Этот метод позволил получить насыщенный розовый цвет, а также красный рубин, который постоянно производился непосредственно на стерлинговом серебре без флюса.Еще лучшие результаты были достигнуты по золоту 18 карат. С 14кт не экспериментировал.
Таким образом, очень тонкий слой (на данный момент я работаю с сеткой 325 меш и меньше) для первого обжига, быстрого и горячего первого обжига. Обжиг, возможно, придется проводить на глаз, а не по времени, поскольку большинство эмалей обжигаются при разных температурах и потому, что детали редко бывают одинакового размера и плотности. Моя печь настроена на 1500 ° F +, чтобы обеспечить время восстановления и выдержку при нагревании. К тому времени, как я открываю дверь и вставляю предмет, температура упала на 80-100 градусов по Фаренгейту. Опыт научит, когда нужно вытаскивать предмет в нужный момент.
- Готовый проект.
Эмаль En Plein может потребовать точности, но именно от этого зависит красота этой техники. Большая гильошированная поверхность зависит от мастерства гильошировщика. Результат готового изделия зависит от навыков и рассудительности эмалиста, его знания каждого цвета, который будет обжигаться, и того, как они различаются от детали к детали, а также от того, как они реагируют на различные сплавы.Эмаль En Plein — это элегантный метод украшения самых разных предметов, а также ювелирных украшений. Часто после обжига гильошированной поверхности основным цветом художники часто рисовали различные сцены, портреты и мотивы с помощью эмали, которая была настолько тонко измельчена, что при смешивании с маслом лаванды она имела консистенцию покрасить. Затем объект был снова обожжен и покрыт тонким слоем прозрачной эмали для защиты.
Порядок проведения процедуры: Евгений Фаберже, сын Карла Фаберже, рассказал о встречах между различными техническими специалистами. Они назывались «круглыми столами». Они будут состоять из управляющего магазином эмали, ювелира, ювелира (если нужно установить какие-то камни), дизайнеров и, конечно же, господина Фаберже. Самая важная причина встреч заключалась в том, чтобы определить, в каком порядке следует применять каждое ремесло. Этот порядок имеет решающее значение для успешного исхода любого произведения, особенно в целом.
Сегодня мы должны объединить все эти навыки в одном лице, поскольку отдельные специалисты практически исчезли.Это делает нашу работу более сложной, но тем не менее полезной. Если у вас есть какие-либо вопросы, напишите мне на адрес robert @ robertwhiteside. com или посетите www.robertwhiteside.com.
Ссылка
Снеговик, А. Кеннет. Золотые ящики Европы восемнадцатого века. Faber & Faber Ltd., 1966. Стр. 81.
Применение и подготовка эмали — Сообщество производителей ювелирных изделий «Ганоксин»
Уже более двух тысяч лет ювелиры наплавляют свои изделия из стекла для обогащения цвета. Замечательные эмалированные работы можно найти во многих древних культурах, они представляют собой знакомые символы технического мастерства и эстетической чувствительности их создателей.
В нашем собственном столетии эмалировка стала успешной благодаря научным и промышленным исследованиям, и благодаря этому она превратилась из всего лишь одного элемента ювелирного искусства в самостоятельную выдающуюся позицию. Достаточно подумать об эмалированной посуде, архитектурной отделке и утилитарных предметах, чтобы понять важность эмалирования в нашем обществе.
Для полного описания эмали читатель может обратиться к книгам, специально посвященным этой теме, таким как Kunsthandwerkliches Emaillieren Эрхарда Бреполя, третье издание, VEB Fachbuchverlag, Лейпциг, 1983. Но даже те, кто не намерен использовать эмаль в своей работе как у первичного элемента должно быть понимание исторической важности эмалирования и общее представление о процессе. Следующие страницы включены сюда именно для этих людей.
Эмалирование — это простой процесс, требующий очень небольшого количества специализированного оборудования.Электрическая печь, в которой металл нагревается до температуры, является самым дорогим оборудованием, и даже это имеет то преимущество, что может использоваться в студии для нескольких других целей. Гораздо более важна и требует большего мастерства подготовка изделия перед эмалированием. Без продуманного дизайна и правильной работы по ювелирному делу эмалированные изделия представляют собой просто цветные кусочки металла.
Применение эмали
Cloisonné
В этом популярном процессе тонкие сплющенные проволоки, обычно из чистого серебра, сгибаются в определенные формы и устанавливаются на кромку для создания рисунка.Проволоки выглядят как серебряные линии на готовом изделии и служат для создания небольших отсеков (по-французски — перегородки) для хранения эмали. Полоски иногда припаяны, но чаще они закрепляются в слое прозрачной эмали, называемом флюсом, до тех пор, пока последний слой эмали не сможет закрепить их. Перегородки заполняются, обжигаются и при необходимости повторно заполняются, а затем после обжига измельчаются для получения плоской поверхности.
Champlevé
Углубления вырезаются на толстую металлическую пластину путем гравировки, долбления, травления, точения, опиливания или заусенцев; Эти области затем заполняются эмалевым порошком, который обжигается, чтобы закрепить его на месте.Хотя это и менее распространено, можно сделать выемки путем пайки вместе проколотых слоев в процессе, известном как наложение.
Затонувшая эмаль
Этот процесс представляет собой комбинацию выемки и перегородки. Относительно тонкий лист драгоценного металла формируется в углубление. Проволоки перегородчатой эмали сгибаются в соответствии с конструкцией и помещаются в эту область, затем заполняются эмалевым порошком и обжигаются обычным способом. Это также называется ложной выемкой.
Plique-à-jour Enamel
В этом довольно специализированном методе эмаль изготавливается для заполнения отверстий, открытых с обеих сторон, что делает ее похожей на витраж. Структура вырезается из листа, изготавливается из проволоки или отливается, затем покрывается фольгой или помещается на слюду для удержания эмалевого порошка во время обжига. После заполнения камер подложка удаляется, и поверхности шлифуются заподлицо. Подобно витражам, такая работа становится особенно яркой, когда сквозь нее падает свет.
Basse Taille Enamel
В этом процессе углубления выполняются путем гравировки, фрезерования или резки долотом. Глубине и фактуре углублений уделяется особое внимание, затем изделие заполняется прозрачной эмалью.Относительные глубины будут отображаться с помощью различных оттенков цвета, так же как вода в бассейне или озере будет выглядеть иначе по мере того, как дно будет уходить. Более глубокие пятна кажутся темнее из-за более толстой эмали, возвышенные — ярче, потому что они лежат близко к поверхности эмали.
Enameling en Rond Bosse (3D Enameling)
Этот термин относится к использованию эмали для покрытия металлических скульптур со всех сторон. Это может быть цельнолитая миниатюрная скульптура или полая из листового металла.
Лиможская эмаль
В 15-16 веках техника эмалирования была доведена до высокой степени совершенства в городе Лимож, Франция. С тех пор процесс получил название города. В процессе Лиможа основа из черной эмали обжигается поверх объекта. Затем поверх основы наносится белая эмаль, создавая различные оттенки серого и белого в зависимости от их толщины. и выстрелил, чтобы создать изображение. Вариант под названием гризайль начинается со слоя черной эмали, который покрывается порошковой белой эмалью.Белый цвет отводится кистью, чтобы показать черную линию.
Эмаль
Портретные миниатюры написаны так же, как гончар рисует на фарфоре. Краски из оксидов металлов наносятся на базовое покрытие из белой непрозрачной эмали. Они наносятся тонкой кистью и могут не уступать по точности и детализации масляной краске. После сплавления эмалей они покрываются прозрачной эмалью — помадкой.
Обзор техники эмалирования в ювелирном деле | |
a) Плоские провода сгибаются, укладываются на кромку и припаяны. б) контуры эмалированной проволоки образованы загнутой и припаянной круглой проволокой; цветная эмаль вплавляется в углубления. c) Эмалированные стены с филигранной эмалью формируются скрученной филигранной проволокой, в остальном процедура аналогична проволочной эмалировке. г) Эмалирование с использованием прямой перегородчатой проволоки, согнутой и припаянной; эмаль вливается в углубления. e) Перегородчатая эмаль, аналогичная d), но перегородчатая эмаль заполнена доверху и залита камнями. f) Согнутая и закрепленная перегородчатой проволокой, отверстия заполнены и проплавлены эмалью, плоско облицовано камнями. г) Утопленная эмаль на тонком листе основы, который был вдавлен, устроена перегородчатая проволока и ячейки заполнены эмалью h) Выемки в основании в толстом листе выполнены и заполнены эмалью, которая наплавляется и наплавляется камнями. |
Материалы и оборудование
Эмали
Эмали приобретаются в виде порошков или комков, которые при необходимости измельчаются до частиц. В основном они состоят из фритты, оксидов и, в некоторых случаях, глушителей. Фритта составляет основу эмали и состоит из кварца, полевого шпата, борной кислоты, соды, поташа и оксида свинца. Цвет достигается за счет добавления оксидов металлов; другие ингредиенты могут быть добавлены для создания специальных эффектов.
Эмали можно приобрести у специализированных дистрибьюторов; беглый взгляд на каталог ослепит начинающий список эмали широким спектром доступных цветов. Необходимое количество, конечно, будет зависеть от выполняемой работы, но для первого эмалиста разумно ограничить свой выбор примерно десятью цветами.Это обеспечит понимание этих эмалей и обеспечит основу, на которой могут быть приобретены дополнительные цвета. Хранить эмали следует в прозрачных стеклянных банках с широким горлышком.
Поскольку цвет порошка эмали отличается от эффекта при обжиге, необходимо создать образец каждого цвета, желательно показать, как он будет выглядеть в нескольких различных применениях. Очистите кусок меди размером примерно 6 x 15 см (3 x 6 дюймов) и нанесите вертикальные полосы одинаковой ширины из белого, слоновой кости и прозрачного флюса высокого обжига.Также включите ленту из флюса, в которую вы наплавили пластину из тонкой серебряной фольги.
Нанесите каждый из ваших цветов на эти полосы под прямым углом. Это покажет эффект каждого цвета на различных фонах. Держите тестовую панель под рукой для справки при выборе эмали для конкретных проектов и создавайте новые тестовые панели по мере увеличения вашего выбора эмалей.
Нанесите каждый из ваших цветов на эти полосы под прямым углом. Это покажет эффект каждого цвета на различных фонах.Держите тестовую панель под рукой для справки при выборе эмали для конкретных проектов и создавайте новые тестовые панели по мере увеличения вашего выбора эмалей.
Печь
Эмалирование можно проводить в пламени, и в древние времена это делалось на очаге, но в настоящее время считается стандартной практикой работа в электрической печи. Вам понадобится устройство, способное поддерживать температуру до 1000 ° C (1830 ° F). Печь с небольшой камерой подходит для большинства ювелирных работ; но, конечно же, для других приложений потребуются блоки большего размера.Печь должна быть оборудована термостатом — устройством, которое будет регулировать температуру для поддержания постоянного уровня. Точность важна, но она не должна быть такой же точной (или дорогостоящей), как те, которые используются в научных лабораториях.
Опоры для обжига
Объекты, покрываемые эмалью, должны опираться на пол печи, пока эмаль тает. Это достигается за счет размещения изделия в металлической конструкции, называемой подставкой. Они доступны в различных формах и могут быть изготовлены из стали, нержавеющей стали, титана или некоторых других экзотических сплавов.Требования к опоре для обжига заключаются в том, чтобы она выдерживала нагрев без усадки, чтобы не образовывались оксиды (они могут отрываться и загрязнять эмаль), чтобы она имела лишь ограниченный контакт с заготовкой. Асбест не следует использовать из соображений безопасности и здоровья.
Точка соприкосновения изделия с опорой не будет иметь гладкого эмалевого покрытия, поэтому эти точки следует свести к минимуму и расположить так, чтобы они падали в местах, где они не испортят дизайн. На рис. 10.5 показана простая, но надежная опора, позволяющая достичь этой цели, но имейте в виду, что обычные опоры, возможно, потребуется изменить для конкретных деталей.
10.5- Простая установка с эмалевым элементом для обжига в печи |
Рабочее место
Чистота имеет решающее значение для успешного эмалирования. Грязь, пыль, жир и любые загрязнения повлияют на эмаль и могут превратить насыщенную прозрачную пленку в мутную пленку или превратить блестящий оттенок в мутный тон. Зона, используемую для шлифовки и полировки, должна быть удалена от места, где наносится эмаль, с соответствующей вентиляцией, чтобы не допустить попадания пыли в воздух. Ювелир, который склоняет свои инструменты в сторону с мыслью о нанесении эмали на своем верстаке, явно не понимает важности этого предупреждения.
Лучше всего обозначить конкретную рабочую зону для эмалирования. Идеально подойдет чистая, хорошо освещенная, водонепроницаемая столешница. Инструменты будут включать чистую ткань, несколько акварельных кистей и посуду с чистой водой. Провода сгибаются тонкими плоскогубцами и накладываются пинцетом. Фарфоровая ступка и пестик используются для измельчения кусков стекла в порошок — процесс, который в идеале будет выполняться в раковине.Порошки переливаются в фарфоровые или пластиковые емкости, из которых они применяются в работе. Порошок трагакантовой камеди смешивают с водой, чтобы получить пасту, которая используется для приклеивания перегородчатой проволоки к их основе. Маленькие сита используются для напыления порошка на металл.
Для обжига необходимы опоры, вилка с длинной ручкой или аналогичный инструмент используется для помещения работы в печь и ее извлечения, когда она будет завершена. Область вокруг печи должна быть облицована огнеупорным кирпичом или аналогичной поверхностью, которая обеспечит место для проведения горячих работ.Вам понадобятся термостойкие перчатки и фартук, а также темные очки, чтобы защитить глаза, когда вы смотрите в светящуюся камеру. Для отделочных работ требуются камни и прутки из карбида кремния, а также обычный набор абразивной бумаги.
Металлы для эмалирования
Поскольку для эмалирования требуется минимальная температура 800 ° C (1470 ° F), металлическая основа может быть изготовлена из высокократного золота, чистого серебра, меди и латунных сплавов с содержанием цинка минимум 5%. . Золото лишь немного расширяется при нагревании, что помогает закрепить стеклянный слой на металлической основе.Кроме того, богатый цвет золота создает подходящую визуальную среду для цветного стекла. Вряд ли случайно в наших музеях можно найти столько прекрасных образцов эмали на золоте.
Чистое серебро — хорошая основа для эмалей, но сплавы чистотой менее 950 Ag не рекомендуются, особенно для прозрачных эмалей, где оксиды вызывают помутнение. Стерлинг при 925 Ag не рекомендуется. При нанесении эмали на серебро полезно сделать поверхность шероховатой.Этот улучшенный механический захват поможет закрепить эмаль на металле.
особенно хороша для эмалирования не только из-за ее низкой стоимости, но и из-за того, что скорость расширения и усадки, а также высокая температура плавления делают ее надежной практически для любой эмали. Конечно, медь легко образует оксиды, и из-за этого цвета не будут такими яркими, особенно с прозрачными эмалями.
Латунные сплавы с содержанием цинка менее 5% являются отличными поверхностями для эмалирования. Они обладают преимуществами меди и, кроме того, обладают несколько более высокой прочностью на разрыв.Латунь с повышенным содержанием цинка абсолютно непригодна для эмалирования, потому что обожженные эмали отрываются при остывании металла.
Champlevé
Углубления, которые будут содержать эмаль, вырезают на относительно толстый лист с помощью резцов, долот или механического оборудования. Эта техника особенно подходит для прозрачных эмалей, потому что разная глубина проявляется в более темных оттенках цвета. Этот аспект выемки не может быть хорошо использован для меди, поскольку прозрачные эмали не переносят оксидов, выделяемых этим металлом.Углубления можно протравить, при этом механическое усилие заменяется химической коррозией. Нижняя поверхность выемки сделана шероховатой для увеличения сцепления эмали с металлом. Стенки разреза должны быть вертикальными или могут слегка наклоняться наружу. Здесь следует избегать подрезов, которые были бы предпочтительнее в случае металлической вставки, поскольку это приведет к растрескиванию под напряжением. При изготовлении многослойной детали для эмалирования металлические перегородки, разделяющие каждую секцию, можно легко сделать разной и переменной ширины, что является отличительной особенностью, которая мгновенно идентифицирует этот процесс как отличный от перегородчатой эмали (рис.10.8).
10.![]() |
Cloisonné
Поскольку перегородчатая проволока тонкая, важно построить изделие в прочном металлическом каркасе, чтобы обеспечить его прочность. Помните, что эмаль не только должна поддерживаться в ее окончательном состоянии, но до этого она должна выдерживать нагрузки обжига и отшлифовки.Эта рама припаивается к листу металла с помощью IT-припоя и должна быть достаточно толстой, чтобы противостоять деформации при обжиге и охлаждении.
Пожалуй, больше, чем другие техники эмалирования, перегородчатую перегородку можно рассматривать как графический процесс из-за важности линий. Каждый кусок проволоки представляет собой линию, и, как рисунок карандашом, каждый может добавить характер части. Поместите рисунок под стекло или пластик, чтобы защитить его во время работы. Типично рисовать дизайн аккуратно и правильного размера на бумаге, а провода изгибать прямо на чертеже, чтобы гарантировать их точность.
Хотя иногда бывает необходимо использовать один прямой кусок проволоки, гораздо чаще конструкцию разбивают на части, которые можно сгибать таким образом, чтобы они могли встать сами по себе. Подумайте о том, чтобы установить букву «V» в положение, в отличие от установки двух отрезков проволоки одной длины, и вы почувствуете точку.
Обычно (хотя и не обязательно) начинают с покрытия листового металла слоем прозрачного флюса, материала, который по сути представляет собой бесцветную эмаль. Затем поверх нее приклеиваются провода с помощью трагакантовой камеди, временной опоры, которая не даст им сдвинуться с места при нанесении эмалевого порошка на место с помощью кисти.Когда изделие обжигается, плавленое стекло приклеится к нижнему слою и к проволокам и скрепит все вместе.
Подготовка металла
Эмаль может прилипать только к металлу, который был очищен и обезжирен. Иногда можно нагреть металл в эмалировочной печи до температуры, при которой сгорают остатки жира, но необходимо следить за тем, чтобы не достичь температуры, при которой образуются оксиды.
Подготовка эмали
Лучшие эмали продаются в виде кусков гравия, которые необходимо измельчить перед использованием.Первый шаг в этом — использовать стальную ступку и пестик, как показано на рисунке 10.10. В этом случае пест плотно прилегает к цилиндру, что предотвращает соскальзывание кусков. Хотя это не является абсолютно необходимым, это устройство обеспечивает быстрое измельчение крупных деталей и предотвращает чрезмерный износ более деликатного раствора.
Мелкие кусочки переносят в фарфоровую ступку с пестиком, где их измельчают до более мелкого порошка. Добавьте немного воды, чтобы зерна не выпрыгнули из миски.Если в вашем водопроводе много химикатов, используйте бутилированную или дистиллированную воду. Непрозрачные эмали измельчают до мелкого порошка, но прозрачные эмали будут иметь самый яркий цвет, если их оставить немного больше.
10.10 — Ступка и пестик (Кресс-секция) |
После измельчения эмалевый порошок промывают, помещая его в неглубокую посуду и перемешивая в чистой воде. Слейте мутную воду и добавьте свежую, повторив процесс несколько раз.В случае опакеров вы можете прекратить их использование после нескольких полосканий, но прозрачные пленки требуют промывки до тех пор, пока сточные воды не станут прозрачными. Несмотря на то, что автор хорошо разбирается в водопроводной воде, эмалисты, работающие в других условиях, могут счесть необходимым использовать дистиллированную или бутилированную воду, чтобы предотвратить загрязнение эмалей минералами.
Очищенная эмаль переносится на небольшую стеклянную посуду, которая, в свою очередь, маркируется номером цвета. В течение рабочего дня они хранятся под колпаком, чтобы свести к минимуму их высыхание и защитить от пыли.Порошки, оставшиеся в конце сеанса, снова кладут в банку и смешивают с большим количеством воды, чтобы они оставались свежими. При следующем запуске сливают воду и несколько раз промывают эмаль.
Нанесение эмали
Стекло дает усадку при охлаждении, это означает, что панель с эмалью только с одной стороны скручивается, когда ее вынимают из печи. Чтобы предотвратить это и уравнять напряжения по всему изделию, очень важно нанести эмаль на обе стороны изделия.Обратная сторона, называемая контрэмалью, часто представляет собой не что иное, как слой одного цвета без рисунка, но ее важность нельзя недооценивать. Нанесение контрэмали — это первый шаг, который необходимо предпринять.
После очистки и придания шероховатости металлу нанесите тонкий слой трагакантовой камеди. Также можно добавить в эмаль немного порошка трагакантовой камеди. Посыпьте им лист равномерно через латунное сито. Нанесите эмаль на инструмент в виде ложки и встряхните ее на несколько дюймов над тарелкой.Дайте эмали высохнуть, осторожно переверните ее и установите в подставку для обжига, а затем нанесите эмаль кистью на перегородку.
Возьмите немного влажной эмали смоченной кистью и нанесите ее на подготовленную заготовку. Степень сырости зависит от выполняемой работы. Если эмаль будет слишком влажной, она выйдет из строя и может смешаться с ранее нанесенными красками. Если он слишком сухой, он не потечет в камеры.
В случае перегородчатой эмали и выемчатой эмали обычно лучше всего наращивать эмаль в несколько слоев, потому что некоторые эмали становятся молочными, если их наносить слишком густо сразу.Полная высота обычно достигается за два-четыре выстрела.
Обжиг эмали
Как упоминалось выше, порошок эмали смешивается с водой, чтобы помочь ему течь в полость, которая должна его содержать. Однако, как только порошковое стекло находится на месте, вода становится ненужной, и поэтому необходимо дать ей испариться. Поместите изделие на эмалировочную печь, которая к этому времени предварительно нагревается для подготовки к использованию. В большинстве случаев это займет всего несколько минут.
Если часть эмали выпадает во время сушки или когда изделие помещается в печь, не наносите свежую влажную эмаль.Будет облачно. Вместо этого либо заполните область сухим порошком, либо устраните потерю при следующем обжиге, либо удалите всю эмаль с этой секции и снова заполните ее свежим влажным порошком.
Когда печь нагревается до заданной температуры, опора для обжига, удерживающая изделие, устанавливается в печь. Производители часто предоставляют информацию об идеальных температурах обжига своими цветами, и, хотя к ним следует прислушиваться, никакое чтение или планирование не могут заменить интуитивного понимания того, что представляет собой правильный обжиг.Каждая ситуация в некоторой степени зависит от толщины и размера металлического объекта, других присутствующих эмалей, толщины эмали, точности печи и других субъективных факторов.
Обычно операция термозакрепления состоит из трех фаз. Сначала порошок эмали спекается в пастообразную массу. Если бы можно было прикоснуться к ней (не надо — она горячая!), Она бы рассыпалась. Затем он тает в липкую массу, все еще неровную на поверхности. В этот момент масса обычно выглядит красной. При продолжительном нагревании эмалевая масса станет ярко-красным и выровняется на гладкую ровную поверхность.Это означает, что деталь готова к удалению. Избегайте перегрева, так как это может изменить цвет эмали.
Изделие снимается и кладется на огнеупорный кирпич или аналогичную жаропрочную поверхность рядом с печью. Если деталь покоробилась, ее следует немедленно расплющить, пока она еще не остыла. Поднимите изделие с опоры для стрельбы и установите на стальную пластину. Надавите на него жестким шпателем — шпатель каменщика пригодится.
Финишная эмаль
Шлифовка
Традиционно, особенно в случае выемчатой и перегородчатой эмали, финиширует изделие до ровной поверхности.Это подчеркивает графичность дизайна и позволяет хорошо видеть провода. Это делается с помощью брусков и стержней из карбида кремния в процессе, называемом камнями.
После того, как обжиг закончен и работа остынет до комнатной температуры, ее устанавливают на доску в раковине или поперек нее так, чтобы струйка воды могла постоянно течь по ней. Камень подходящей формы растирают с сильным давлением взад и вперед по поверхности, пока поверхность не станет полностью заподлицо. Хотя этого можно добиться с помощью мокрой шлифовальной машины, в большинстве студийных ситуаций эмали продолжают обрабатывать камнями вручную.
Промывка
После шлифовки на поверхности эмали появляется много пор, возникающих в результате образования пузырьков воздуха в расплавленном стекле. В процессе побивания камнями эти пузыри разрезаются и остаются на поверхности в виде крошечных ямок. Остатки абразивов застревают в этих отверстиях и могут испортить готовую деталь в виде серых пятен, если их не удалить. Готовую работу энергично потрите щеткой для стекла под проточной водой, а затем снова протрите с мылом и зубной щеткой. Осмотрите поверхность с помощью лупы, чтобы убедиться, что все следы мусора смыты.Большие ямки очищают иглой, заливают свежей эмалью и обжигают.
Flash Firing
Если изделие должно иметь матовую поверхность, последним процессом является побивание камнями. Когда предполагается, что эмаль будет блестящей, работа возвращается в печь для последнего обжига после того, как поверхность отшлифована и очищена. Обжиговую печь нагревают до высокой температуры и деталь помещают в нее на несколько секунд — ровно настолько, чтобы поверхность расплавилась и стала гладкой. Чем горячее печь на этом этапе, тем ярче получаются цвета, но необходимо следить за тем, чтобы работа не перегревалась.
Полировка
Металл вокруг эмалированной области можно полировать обычными составами, если вы будете осторожны, чтобы не оставлять полировку слишком долго на одном месте. Компаунды не изнашивают стекло, поэтому длительное воздействие может привести к образованию неровной поверхности при удалении металла. Как правило, этого легко избежать. Достаточно легкого прикосновения к бафу, чтобы металл приобрел яркий блеск.
Таблица 10.1 показывает некоторые возможности ошибок при эмалировании.
Проблема | Причина | Средство устранения |
Металлические детали расплавлены | Килин был слишком горячим | Уменьшить температуру килина |
Проволока Клуазона 901 оплавить проволоку | с эмалью 901 используйте меньше припоя||
Белый становится пятнистым с зеленым | эмаль реагирует с медью | используйте более толстый слой эмали |
Белый становится пятнистым с желтым | эмаль реагирует с серебром | избегает контакта с серебром |
Черные пятна на эмали | Возможно, на эмаль попала железная пыль или опилки | очистите элементы и камеру килина |
потертости на эмали | могут быть остатки полировальных составов | очистите работу полностью после обработки камнями или полировкой |
Пористая эмаль 9 0120 | эмаль могла быть перегрета; использование неподходящего металла в качестве основы для эмали | снижает температуру килина; используйте другой металл |
Обесцвечивающая пленка на эмали | эмаль была недостаточно очищена | очистить эмаль более тщательно |
Пузырьки в эмали | эмаль была загрязнена | очистить эмаль | более | Мутные пятна и края | вода могла попасть на пробу эмалевый порошок | равномерно увлажнить эмаль |
эмаль показывает трещины | неравномерное тепловое расширение соседних эмалированных участков; неравномерный нагрев эмали и металла; неправильная толщина металла; недостаточно контрэмали | Перейти на эмали с аналогичными свойствами; используйте больше контрэмали |
прозрачная эмаль становится мутной | слишком мелко измельченная; недостаточно очищены; слишком густой намаз, слишком высокая температура в килине | используйте фритту более крупного помола; хорошо вымыть; огонь при более умеренной температуре |
металлическая деформация | неправильная огневая база; недостаточная контрэмаль | выбрать в качестве основы другой металл; используйте больше контрэмали |
Porcelain Enamel Powder в 21 веке> Powder Coated Tough
Технические основы
Фарфоровая эмаль производится из натурального неорганического сырья. Это не только исключительно прочная отделка, но и полностью пригодная для вторичной переработки, а потому экологически чистый продукт. Смесь минералов плавится почти так же, как обычное оконное или тарное стекло; это начало процесса. Как только все ингредиенты полностью расплавятся — при температуре более 2000 градусов по Фаренгейту — расплавленная смесь выливается из плавильного завода и закаливается между охлаждаемыми водой валками. Этот процесс известен как «спекание». Затем быстроохлаждаемая стеклянная лента разбивается на хлопья или фритту.Химический состав фритты / стекла адаптирован к эксплуатационным характеристикам конечного продукта и используемой металлической подложке.
При составлении рецептуры фритты эмалевое покрытие должно выполнять несколько ключевых задач. Для грунтовочного покрытия первый слой стекла на металле, фарфорово-эмалевое стекло должно 1) прилегать к металлу (связка), 2) соответствовать тепловому расширению металлической подложки и 3) иметь гладкую, бездефектную поверхность. Для второго слоя, покровного слоя, эмаль должна 1) иметь желаемый цвет и текстуру поверхности и 2) иметь соответствующую химическую стойкость для предполагаемого использования.В особых случаях все это должно быть выполнено одним слоем эмали, а в других случаях требуется три слоя эмали. Таблица 1 показывает общий диапазон химического состава как грунтовочных, так и покровных эмалей, а также основные функции химических компонентов.
Препарат для фарфоровой эмали
Чтобы подготовить фритту для нанесения на основу, ее комбинируют с другими материалами, которые могут включать огнеупоры, пигменты, глушители, глины и поверхностно-активные вещества.Эти ингредиенты смешиваются в виде сухого порошка или водной суспензии для нанесения на металлическую основу. Фритту и сырье обычно измельчают в шаровой мельнице для достижения как полного смешивания, так и надлежащего измельчения и распределения частиц. Сегодня большинство аппликаторов эмали покупают либо электростатическую сухую порошковую эмаль, готовую к распылению, либо готовую к использованию (RTU) порошковую эмаль, в которую добавляется вода для приготовления жидкой суспензии эмали.
Таблица 1: Диапазоны состава фритты
Нанесение порошковой эмали
С изобретением порошкового покрытия около 60 лет назад в лакокрасочной и отделочной промышленности началась большая работа по использованию этой новой технологии.Производство фарфоровой эмали было одним из первых, кто начал применять электростатическое порошковое покрытие, но требовалось много доработок как с точки зрения материалов, так и с точки зрения оборудования. К 1980-м годам порошковое покрытие фарфоровой эмалью имело место на многих заводах, в первую очередь для столовых приборов, но также и на нескольких линиях для полостей, таких как духовки и посудомоечные машины.
Физика порошкового покрытия порошковой фарфоровой эмали такая же, как и для традиционной порошковой краски, хотя есть некоторые различия в поведении и т. Д.Одним из наиболее заметных является эффективность передачи; Эффективность порошковой фарфоровой эмали составляет около 40 процентов, поэтому гораздо больше порошка проходит через систему восстановления по сравнению с традиционной порошковой краской. Кроме того, порошки фарфоровой эмали часто наносятся более толстой пленкой; обычно от шести до восьми мил. Почти все применение электростатической сухой порошковой фарфоровой эмали предназначено для крупных бытовых приборов; для наружных частей это обычно двухслойный / однообжиговый процесс, а для внутренних (неаккуратных) частей — один слой / один обжиг.При двухслойной / одной огневой обработке первый слой представляет собой специальную грунтовочную эмаль (предназначенную для прилипания к стали), которая наносится толщиной от одного до двух милов с последующим нанесением во второй камере нанесения покровного слоя (для окончательный цвет детали) толщиной от пяти до семи мил. Оба слоя плавятся / отверждаются при температуре около 1500 градусов по Фаренгейту за один проход через печь. Время обжига обычно зависит от толщины металла; для успешного нанесения эмалевого покрытия время достижения максимальной температуры составляет две-три минуты.
Для электростатической порошковой эмали преимущества аналогичны системам порошковой окраски. Они включают полное устранение избыточного распыления, контроль толщины покрытия, однородность пленки, лучшее покрытие кромок, блеск и гладкость отделки после обжига, а также преимущества автоматизации и контроля современных систем нанесения порошка. Основным ограничением для электростатической порошковой эмали является выбор цвета; это потому, что цвет должен быть растоплен во фритте. Использование фритты с пигментом проблематично из-за различий в размере частиц, плотности и параметрах электрического заряда — таким образом, переработка затруднена, поскольку различные компоненты применяются с разной скоростью.Смена цвета требует либо нескольких кабин, либо значительного времени на уборку.
В последнее время мы наблюдаем рост использования робототехники с применением порошков, что улучшает воспроизводимость и эффективность производства, а также снижает затраты. Исследования и разработки по химическим составам и технологиям шлифования электростатических порошковых эмалей также продолжаются с целью улучшения параметров нанесения и уменьшения дефектов.
Нанесение мокрой эмали
Для систем мокрой фарфоровой эмали типичное применение включает распыление или нанесение покрытия потоком.Однако существуют и другие методы нанесения для конкретных конечных продуктов, такие как рулонное покрытие непрерывной полосы для белых досок и гальваническое покрытие или электрофорез, которые обеспечивают очень гладкую однородную поверхность, а также наилучшее покрытие краев и отверстий, когда обе стороны подложки покрыты эмалью. Для декорирования эмалированных продуктов / поверхностей используется множество других процессов, включая трафаретную печать, прямую эмульсионную печать, цифровую струйную печать, переводы (например, переводные картинки с водяными слайдами) и ручную роспись.
Обжиг
Это этап процесса, на котором два материала, стекло и сталь, становятся одним. После нанесения покрытия детали должны быть обожжены при температуре около 1500 градусов по Фаренгейту, чтобы должным образом сплавить стеклянное покрытие и установить прочную химическую связь со сталью или другим металлическим субстратом.
Новые разработки
В настоящее время ведется ряд разработок во многих областях, включая новые применения фарфоровой эмали, улучшенные фритты и материалы, а также более совершенные системы и оборудование для нанесения эмали.
Одно из новых многообещающих применений фарфоровой эмали — это покрытие из реактивного стекла для армирования стали в бетоне, где покрытие фактически сцепляется с бетоном. Для гладких стальных деталей, таких как волокна, прочность на вырыв увеличивается в пять раз по сравнению с сталью без покрытия. Для деформированной арматуры повышение прочности на вырыв составляет около 15 процентов, что может быть значительным в областях скученности арматурных стержней, где длина развертки является проблемой. Не менее важно то, что покрытие из фарфоровой эмали также обеспечивает прочный барьер для коррозии.Процесс нанесения электростатического порошкового покрытия является многообещающим в этой развивающейся области. Кроме того, собственные разработки ведутся для нескольких рынков: возобновляемые источники энергии, добыча / транспортировка нефти и газа и высокотемпературные покрытия для металлов.
В области новых эмалевых материалов продолжаются исследования и разработки новых цветов, отделки поверхности и эффектов. Сюда входят металлические цвета, имитация полированных металлических поверхностей, текстурированных поверхностей (эмаль или стальная подложка), перфорированный металл и применение фарфоровой эмали в проектах общественного искусства.
Что касается прикладных систем, продолжаются разработки, направленные на повышение эффективности переноса порошка, улучшение подачи эмалевого порошка и новые технологии автоматизации управления. В настоящее время ведутся дополнительные работы по интеграции робототехники в системы нанесения порошковой и влажной керамической эмали.
Фарфоровая эмаль, уходящая корнями в 4000 лет назад, имеет долгую и постоянно развивающуюся историю. От ранних применений, найденных в артефактах, таких как ювелирные изделия и религиозная иконография, до промышленных применений, относящихся к концу 1800-х годов с эмалированием чугуна, эта технология продолжала изобретать себя заново, чтобы удовлетворить потребности современного производства.Несомненно, благодаря множеству разработок, фарфоровая эмаль будет оставаться актуальной технологией нанесения покрытий на многие годы вперед.
Как наносить эмалевую краску на дерево
Эмалевые краски очень практичны и обладают множеством преимуществ. Он подходит для окраски поверхностей, подверженных регулярному износу, или предметов мебели, предназначенных для использования на открытом воздухе. Нанесение эмалевой краски на дерево позволяет краске держаться дольше, придавая поверхности твердую, глянцевую и прочную отделку.Поскольку эмали доступны в широком спектре цветов и могут быть как на водной, так и на масляной основе, очень важно выбрать правильную смесь в соответствии с требованиями вашего проекта. В то время как с эмалями на водной основе легче работать и они быстрее сохнут, эмали на масляной основе служат дольше, придавая поверхности более гладкую светящуюся текстуру.
Мы в Индиго красок предлагаем вам широкий выбор высококачественных эмалевых красок на выбор. Если вы хотите отремонтировать свой дом или переделать старую деревянную мебель, новый слой эмалевой краски станет ключом к преобразованию.
Шаги по нанесению эмалевой краски на дерево.
Step 1
Чтобы добиться глянцевой отделки вашей мебели, очень важно тщательно подготовить деревянную поверхность. Вы должны начать с зачистки дерева мелкозернистой наждачной бумагой. Он сгладит края за счет загибов любых выступов или неровностей.
Step 2
Грунтовки — это уникальные лакокрасочные материалы, используемые в качестве базового покрытия, которое подготавливает поверхность перед нанесением верхнего покрытия.Слой грунтовки заполнит трещины или трещины на деревянной поверхности, давая краске относительно однородную поверхность для прилипания. Выберите цвет, который подходит к вашей эмалевой краске, и избегайте использования более темного оттенка по сравнению с выбором эмали.
Step 3
Использование правильной кисти очень важно для получения желаемой гладкой поверхности. Вы можете использовать кисть премиум-класса с натуральным ворсом, чтобы сохранить однородность ориентации и толщины каждого мазка.Желательно перед нанесением смочить кончик кисти нужным количеством краски. Штрихи должны исчезнуть, как только подшерсток начнет сохнуть.
Алкидная эмаль: все, что нужно знать
Эмалевая краска имеет глянцевую и прочную поверхность, которая отлично подходит для таких областей вашего дома, как отделка, кухонные шкафы и двери. Эмали хорошо подходят для использования, так как имеют твердую и устойчивую к царапинам поверхность
. Их часто используют на кухнях и в ванных комнатах, поскольку они водостойкие и пригодны для стирки.
Существует два различных типа обычно используемых эмалей: традиционные алкидные эмали и гибридные эмали. Традиционные эмали на масляной основе и гладкие. В гибридных эмалях используется водно-алкидная технология. Это дает им финиш масляной краски с легким нанесением краски на водной основе
.
Любой из этих типов подойдет для домашнего рисования своими руками, но вы должны знать плюсы и минусы каждого из них. Вот все, что вам нужно знать о том, что такое алкидная эмалевая краска и как ею пользоваться.
Традиционная алкидная эмаль
Обычная алкидная эмаль известна как краска на масляной основе. Традиционные алкидные эмали
невероятно глянцевые, самовечерние и гладкие. Их часто называют зеркальными, что делает их идеальными для шкафов.
Однако химические растворители выделяют высокие уровни ЛОС (летучих органических соединений), которые токсичны для людей и способствуют выбросам углекислого газа. Это делает их менее популярным выбором, чем некоторые варианты эмали на водной основе.
Алкидная эмаль изготовлена из алкидных смол в химическом растворителе. Он высыхает по мере испарения основы растворителя
, оставляя после себя алкидные смолы. Эти смолы затвердевают при высыхании и окислении на воздухе,
, что придает краске очень прочную и глянцевую поверхность.
Традиционные алкидные эмали можно использовать везде, где требуется прочная и глянцевая краска.
Шкафы, двери и обшивка часто окрашиваются алкидными эмалями. Хорошим вариантом для традиционной алкидной эмали является краска для дверей и отделки на масляной основе Valspar.
Плюсы обычной алкидной эмали:
- Высокий уровень ЛОС (летучих органических соединений), которые способствуют выбросу углекислого газа
- Может пожелтеть от тепла и старения, как и большинство масляных красок
- Требуется разбавитель для краски для очистки
Гибридная алкидная эмаль
Гибридные алкидные эмали объединяют лучшее из красок на водной основе с лучшими красками на масляной основе
.Они используют водную алкидную технологию, так что алкидные смолы суспендированы в водной основе
, а не в химическом растворителе.
Гибридные алкидные эмали обычно не имеют запаха, их можно мыть водой с мылом. Они по-прежнему обладают популярными характеристиками традиционных алкидных эмалей. Они гладкие, самовыравнивающиеся
с глянцевой и прочной поверхностью. Гибридные эмали обладают отличной адгезией и подходят для стирки.
В основном, все гибридные алкидные эмали обладают преимуществами формулы
как на масляной, так и на водной основе.Они имеют такое же применение и внешний вид, как и эмаль на масляной основе. Однако они
более экологичны из-за низкого содержания летучих органических соединений.
Часто встречаются гибридные эмали со смесью алкидных и акриловых или уретановых смол.
придает краске дополнительную твердость и снижает пожелтение. Не влияет на процесс нанесения краски
.
можно использовать так же, как и традиционные алкидные эмали. Они являются хорошим выбором для отделки
шкафов и дверей.Некоторые хорошие гибридные эмали включают акриловую алкидную эмаль ProClassic и гибридную уретановую алкидную эмаль
. Benjamin Moore Advance — отличный вариант для окраски кухонных шкафов
.
Плюсы гибридной эмали
Долговечность и износостойкость
Очень твердая и глянцевая отделка
Самовыравнивание и гладкость во время покраски, как у обычных алкидных эмалей
Моющиеся и водостойкие после отверждения
Низкое содержание летучих органических соединений по сравнению с традиционными алкидными эмалями
Очистка с мылом и водой
Минусы гибридной эмали
Иногда имеет менее твердую отделку, чем эмаль на масляной основе
Некоторые разновидности менее глянцевые, чем эмаль на масляной основе
Какую эмалевую краску использовать для
Эмалевые краски имеют прочное глянцевое покрытие, водостойкое.Это делает их отличным выбором
для окраски интенсивно используемых участков вашего дома. Попробуйте использовать эмалевую краску для следующих участков.
- Кухня и ванные комнаты
- Шкафы
- Отделка или плинтусы
- Окна и двери
- Мебель тяжелого назначения, такая как комоды или стулья
- Металлическая мебель или техника
Как наносить алкидную эмалевую краску
Эмалевая краска толще и более вязкая, чем большинство латексных красок для внутренних работ.Нанести
может быть непросто, если вы никогда не использовали его раньше.
Этот же процесс можно использовать для нанесения традиционных алкидных эмалей и для нанесения красок на основе гибридных эмалей
. Обе краски очень похожи на ощупь во время окраски и отделки, за исключением того, что гибридные эмали
легче поддаются очистке.
Материалы, необходимые для нанесения алкидной эмалевой краски
Вам нужно выбрать подходящие материалы для нанесения эмалевой краски. Решите, хотите ли вы использовать
гибридную эмаль или традиционную алкидную эмаль.При выборе материалов
помните о следующих советах.
- Гибридная эмалевая краска имеет меньше летучих органических соединений и прошла долгий путь, но алкидная эмалевая краска
- традиционно считается немного более долговечной.
- Выберите кисть с жесткой щетиной, которая может растекать густую эмалевую краску. Убедитесь, что щетка
- чистая.
- Выберите грунтовку, подходящую для используемого типа эмали. Грунтовки на масляной основе
- лучше всего работают с эмалевой краской, потому что они герметизируют древесину шкафов и отделки, поэтому эмаль
- может хорошо держаться.
Если вы красите шкафы, двери или отделку эмалевой краской, вам понадобятся следующие материалы.
- Кисти
- Грунтовка
- Наждачная бумага или шлифовальные губки
- Тряпки или старые листы
- Малярная лента
- Эмаль: акриловая алкидная эмаль ProClassic, алкидно-уретановая эмаль и масляная краска Valspar для дверей и отделки.
- Малярный респиратор
- Очищающие материалы: мыло и вода работают для гибридных эмалей, но вам понадобится растворитель для краски для масляной эмали.
Нанесение алкидной эмалевой краски
Независимо от того, красите ли вы шкафы, двери, отделку или что-то еще, процесс нанесения эмалевой краски
остается относительно одинаковым.
- Узнайте, сколько краски вам понадобится, и соберите все необходимые материалы.
- Выберите хорошо проветриваемое место, чтобы не вдыхать химические вещества и токсины. Это более важно для традиционных алкидных эмалей, чем для гибридных эмалей. Алкидные эмали имеют более высокий уровень содержания летучих органических соединений, поэтому при их нанесении вы можете использовать малярный респиратор.
- Положите тряпки или простыни, чтобы защитить область, которую вы рисуете. Обмотайте обмотку и плинтусы лентой
- Если на том, что вы красите, уже есть слой краски, удалите его с помощью средства для снятия краски.
- Подготовьте поверхность, которую вы будете красить. Отшлифуйте поверхность до более мелкой крупы. Очистите и прогрунтуйте поверхность.
- Для достижения наилучшего результата обычно следует нанести два слоя эмалевой краски. Если можете, дайте эмали полностью высохнуть между слоями.
- Если краска брызнула или пролилась, очистите ее как можно скорее.При высыхании удалить очень сложно.
- Обязательно утилизируйте остатки краски надлежащим образом.
Эмалевой краске обычно требуется 8-24 часа между слоями, чтобы она могла полностью высохнуть. На всякий случай подождите все 24 часа. Гибридные эмали на водной основе могут сохнуть немного быстрее. Старайтесь избегать интенсивного использования, пока краска полностью не затвердеет в течение одной-двух недель.
Как избежать следов кисти при использовании алкидной эмали
Если вы новичок в использовании эмалевой краски, вы можете задаться вопросом, как избежать следов кисти и выровнять краску.Есть несколько способов добиться этого.
Поскольку эмалевая краска имеет такую гладкую и глянцевую поверхность, она может привлечь внимание к дефектам окрашенной поверхности. Если вы красите деревянные шкафы или отделку, следите за естественной текстурой дерева. Вы можете использовать шпатлевку с текстурой дерева для получения идеально гладкой поверхности.
Вы также можете смешать красочную добавку, такую как Penetrol, с алкидной эмалевой краской. Это разбавит краску и даст вам больше времени для корректировки мазков кисти и проверки уровня краски.
Не забудьте смочить краску на последнем слое. Наклоните кисть и проведите ею по всей длине поверхности. Это поможет скрыть недостатки и свести к минимуму следы от кисти. Это особенно важно при окраске длинных поверхностей, например дверей.
Теперь вы узнали все необходимое, чтобы выбрать подходящую алкидную эмалевую краску для вашего проекта окраски. В следующий раз, когда вы будете использовать алкидную эмаль, запомните эти советы для получения идеальной отделки.
Эмаль(стекловидная) — обзор
2.2.5 Материалы для сжигания азота
Материалы для сжигания в азоте или инертной атмосфере должны быть стабильными при низких концентрациях кислорода, около 5–10 частей на миллион, и не должны восстанавливаться органическим носителем. Такие материалы, как оксиды драгоценных металлов, PbO и другие оксиды, которые легко восстанавливаются, должны быть заменены материалами, которые выдерживают обжиг в суровых условиях. Замена проводов и диэлектриков проще, поскольку они содержат один основной ингредиент, но намного сложнее для резисторов. Проводящие фазы RuO 2 , рутенат свинца, рутент висмута и стекло, содержащее свинец, необходимо заменить другими материалами.Для изготовления СКР использовались несколько типов проводящих материалов с безвинцовыми стеклами, которые можно обрабатывать в инертной или восстановительной атмосфере. Первая группа основана на боридах, нитридах и силицидах. Вторая группа основана на оксидах, таких как легированный SnO 2 , In 2 O 3 и рутенаты семейства перовскита, MRuO 3 ; третья группа основана на взаимодействии материалов во время обжига с образованием проводящей фазы; Примером этой группы является взаимодействие между Мо и МоО 3 с образованием МоО 2 , который представляет собой оксид металла.
Примеры проводящих материалов на основе смеси тугоплавкого карбида и тугоплавкого металла приведены Мерфи и Джанакирама-Рао (1965), которые описывают W и WC с боросиликатным стеклом бария, состоящим из 48% BaO, 8% CaO, 23% B. 2 O 3 и 21% SiO 2 . Смеси нитридов переходных элементов и переходных металлов и смеси карбид-металл, WC-W, описаны Маллиганом (1969). Маккензи (1974) описывает материал сопротивления на основе TaC и Ti и боросиликатного стекла щелочноземельного металла.Материал сопротивления стекловидной эмали, состоящий из стеклянной фритты и мелкодисперсного борида металла переходных элементов групп IV, V и VI периодической таблицы Менделеева, где боридом металла может быть CrB 2 , ZrB 2 , MoB 2 , TaB 2 или TiB 2 , обсуждается Хуангом и Мерцем (1970). Мерц и Шапиро (1980) описывают стойкий к стекловидной эмали материал, содержащий боросиликатное стекло бария, Ta и добавки Ti, B, Ta 2 O 5 , TiO, BaO 2 , ZrO 2 , WO 3 , Ta 2 N, MoSi 2 и MgSiO 3 .Шапиро и Мерц (1980) описывают стойкий к стекловидной эмали материал, содержащий Ta 2 N, стекло и добавки, выбранные из B, Ta, Si, ZrO 2 и MgSiO 3 . Мерц и Шапиро (1977) описывают композицию сопротивления, содержащую стекло и нитрид тантала или стекло, а также W и WC. Наир (1987a, 1987b, 1987c) обсуждает резистивные композиции на основе полупроводникового материала, состоящего по существу из карбида тугоплавкого металла, оксикарбида или их смесей и невосстанавливающего стекла; анионодефицитный полупроводниковый материал, состоящий по существу из нитрида тугоплавкого металла, оксинитрида или их смеси и невосстанавливающего стекла; и полупроводниковый материал, состоящий по существу из избыточного катионного твердого раствора и невосстанавливающего стекла.Куо (1987a) описывает резистивные композиции на основе силицидов TiSi 2 , Ti 5 Si 3 , Al 2 O 3 и щелочных боросиликатных стекол.
Донохью (1985, 1986a, 1986b) и Донохью и Маркус (1980) описывают огнеопасные азотом составы TFR, модификаторы TCR, подходящие составы стекла, термодинамические расчеты, касающиеся восстанавливаемости ингредиентов стекла, Ta 2 O 5 , содержащие стекла и Обзор литературы.Watanabe et al. (1991) описывают резистивную пасту, которая содержит гексаборид металла, стекловидное связующее, которое содержит определенное количество Nb 2 O 5 , и, кроме того, паста может содержать по меньшей мере один нитрид, выбранный из группы, состоящей из AlN и BN.
Диксод олова, SnO 2 , был использован для изготовления огнеупорного материала, чрезвычайно устойчивого к коррозионному воздействию расплавленного стекла (Hood, 1941). Позже Мохел (1949) обнаружил, что когда SnO 2 смешивают с усадочным агентом, содержащим соединения одного из Cu, Ag, Au, Mn, Fe, Co и Ni, и нагревают до 1200 ° C или выше, в результате получается спеченное тело имело высокую электропроводность.Легированный SnO 2 использовался для изготовления высоковольтных резисторов, проводящих глазурей и резисторов. Эти применения и другие свойства легированного SnO 2 были предметом обсуждения: Basu et al. (1974), Binns (1974), Burkett (1961), Dearden (1967), Gress et al. (1968) и Пауэлл (1974). Whalers и Merz (1977, 1980, 1981, 1982a, 1982b, 1983a, 1983b) описывают материал резистора из стекловидной эмали на основе SnO 2 , стекла, Ta 2 O 5 и других добавок.Эти патенты также обеспечивают предварительную обработку SnO 2 и добавки в восстановительной атмосфере и атмосфере азота. Hormadaly (1985a, 1985b, 1985c, 1985d, 1986a, 1987a, 1987b) описывает воспламеняемые азотом составы СКР на основе Sn (II) 2 – x Ta 2 – y
Sn (IV) y O 7 – x – y / 2 пирохлоры, SnO 2 , бессвинцовые составы стекла и модификаторы TCR. Куо (1987a, 1987b, 1987c, 1988) описывает составы TFR на основе SnO 2 , растворов резинатов, таких как резинаты переходных металлов, и термическую обработку покрытого резинатом SnO 2 в восстановительной атмосфере, Ta 2 O 5 стекло и добавки.Asada (1991) описывает резистивные композиции на основе SnO 2 , термообработанного порошка SnO 2 и Ta 2 O 5 , стекла и танталатов.
In 2 O 3 представляет собой полупроводник n-типа, который нашел применение в электрических контактах (Richardson and Swinehart, 1951) и светопропускающих электродах (Amans, 1966). Блок и Монс (1968) описывают состав резистора из оксида индия, метод и статью. Составы были составлены с бессвинцовым стеклом: 9.5 мас.% Al 2 O 3 , 49,4 мас.% SiO 2 , 10,4 мас.% B 2 O 3 , 30,3 мас.% BaO и 0,4 мас.% Нещелочных оксидов. Пасты можно обжигать на воздухе или в инертной атмосфере при температуре от 800 до 1200 ° C. Сжигание в инертной атмосфере снижает сопротивление и повышает TCR. Электропроводность In 2 O 3 может быть изменена путем добавления легирующих добавок. Добавками, увеличивающими проводимость, являются Sb, As, P, Nb, Ce, Si, Ta, Zr, Ti, Sn и Mo, а присадками, снижающими проводимость, являются Cu, Au, Ag, Pt, Pd и Li.Электропроводность также может быть увеличена за счет образования дефицитного по кислороду In 2 O 3 и за счет замены кислорода галогеном. Прабху и Ханг (1983a, 1984a) описывают состав резистора In 2 O 3 . Используемые легирующие добавки: MgO, V 2 O 3 , V 2 O 5 , оксид железа и состав стекла: (1) 20,21 мас.% SiO 2 , 15,62 мас.% B 2 O 3 , 51,59 мас.% BaO, 12,58 мас.% CaO, (2) 16,75 мас.% SiO 2 , 19.42 мас.% B 2 O 3 , 51,32 мас.% BaO, 12,51 мас.% CaO. Композиции обжигали в атмосфере азота при температуре от 850 до 950 ° C.
Hankey (1985) описывает замещенный перовскит рутения A ′ 1-x A ′ ′ x B ′ 1-y B ′ ′ y O 3 , где A′-Sr, A ′ ′ -Ba, La, Y, Ca и Na, B′-Ru и B ′ ′ — Ti, Cd, Zr, V, Co и боросиликатное стекло щелочноземельного металла. Стейнберг (1989) описывает тот же перовскит с такими добавками, как Ni, Cu и CuO.
Педдер (1982) объясняет способ сделать резисторы совместимыми с медным проводником.Композиция резистора представляет собой смесь Mo и MoO 3 , свинцово-цинк-боросиликатного стекла и таких добавок, как W и V 2 O 5 . Во время обжига в атмосфере азота оксид молибда восстанавливается Мо и органическим носителем до МоО 2 , который имеет высокую электропроводность и структуру рутила. Прабху и Ханг (1983b, 1984b) описывают низкокачественные резистивные чернила для металлических подложек с фарфоровым покрытием на основе смесей SnO-MoO 3 или Mo-MoO 3 , щелочноземельного боросатного стекла, органических носителей и модификаторов TCR CdO. и V 2 O 5 .Оксид молибда будет восстановлен SnO до смеси двух оксидов со структурой рутила SnO 2 и MoO 2 , которые могут образовывать твердый раствор.
Некоторые составы медных проводников описаны Martin (1997), Prabhu et al. (1988, 1989a, 1989b) и Siuta (1986, 1987).
Безлоскутное применение производной эмалевого матрикса при повторном лечении пародонта: многоцентровое рандомизированное технико-экономическое обоснование
Цель: Изучить потенциальную пользу производного эмалевого матрикса (EMD) в качестве дополнения к повторной обработке остаточных карманов, сохраняющихся после этапов 1 и 2 пародонтальной терапии.
Материал и методы: 44 взрослых пациента участвовали в многоцентровом рандомизированном клиническом исследовании с разделенным ртом. Они поступили на повторную оценку после первоначальной нехирургической пародонтальной терапии (этапы 1 и 2 пародонтальной терапии) по поводу генерализованного пародонтита с минимум 2 зубами с остаточной глубиной зондирующего кармана (PPD) ≥5 и ≤8 мм, с кровотечением при зондировании. (BOP).Два зуба с аналогичным PPD были рандомизированы для повторного использования инструментов с (тестовым) или без (контрольный) дополнительным безлоскутным введением EMD. Были проанализированы различия в изменениях PPD и BOP от исходного уровня до 6 и 12 месяцев, а также сравнивалась частота закрытия карманов (PPD ≤4 мм и без BOP).
Полученные результаты: Для основного результата «изменение среднего PPD через 6 месяцев» значимое дополнительное преимущество 0.