Присадка для воды при обработке стекла: смазочно-охлаждающая жидкость для обработки стекла — патент РФ 2495096
смазочно-охлаждающая жидкость для обработки стекла — патент РФ 2495096
Настоящее изобретение относится к смазочно-охлаждающей жидкости для алмазной обработки стекла, включающей воду и соль полимерных производных аминогуанидинов, отличающейся тем, что она дополнительно содержит арабиногалактан при следующем соотношении компонентов, мас.%: соль полимерных производных аминогуанидинов — 0,1-0,3; арабиногалактан — 1.0-1.1; вода — остальное. Техническим результатом настоящего изобретения является повышение производительности за счет отсутствия операций по механическому удалению отлагающейся на поверхности трудноудаляемой суспензии стекла, а также обеспечение повышение качества обработки за счет уменьшения образования царапин при механическом удалении ошлифованного стекла. 1 табл.
Формула изобретения
Смазочно-охлаждающая жидкость для алмазной обработки стекла, включающая воду и соль полимерных производных аминогуанидинов, отличающаяся тем, что она дополнительно содержит арабиногалактан при следующем соотношении компонентов, мас.%:
Соль полимерных производных аминогуанидинов | 0,1-0,3 |
Арабиногалактан | 1.0-1.1 |
Вода | Остальное |
Описание изобретения к патенту
Изобретение относится к технологиям обработки стекла, в частности к составам смазочно-охлаждающих жидкостей (СОЖ), и может быть использовано при его шлифовке.
При обработке фацета стекол (кромки стекла) убираются сколы и микротрещины на кромке, что повышает безопасность в работе и увеличивает прочность стекла.
Выбор состава СОЖ часто определяет режим обработки стекла и эффективность процесса: производительность, износ и стойкость инструмента, очистку обработанной поверхности от остатков стекла.
Известны смазочно-охлаждающие жидкости, включающие полимерные добавки на основе полиэтиленполиамина (АС СССР № 1074895, Патент РФ № 2055862, Патент РФ № 2062293, Патент РФ № 2168539). Такие СОЖ используются при получистовом и чистовом шлифовании изделий из стекла алмазным инструментом.Однако данные составы СОЖ имеет следующие недостатки и ограничения — вредные условия труда, как в производстве, так и при использовании СОЖ органических соединений: полиэтиленполиамина, формалина и солей тяжелых металлов, что делает их экологически вредными. Невозможность длительного использования и хранения таких СОЖ из-за образования грибков. Также применение данных СОЖ имеет низкую эффективность при использовании алмазного инструмента на органической связке вызванную структурированием высокоосмоленных продуктов (инструмент засаливается).
Наиболее близкими по технической сущности и достигаемому результату к предлагаемому изобретению являются составы СОЖ для механической обработки стекла, включающие в качестве полимерных добавок соли полимерных производных аминогуанидинов (ПОАГ) (Патент РФ № 2182593). Данные СОЖ на основе ПОАГов эффективно работают как с алмазным инструментом на металлических связках, так и с инструментом на органических связках, показывают достаточно высокую производительность и качество обработанной поверхности, а также позволяет исключить образование и рост грибков при использовании и хранении смазочно-охлаждающей жидкости.
Недостатками данных СОЖ является то, что они не обеспечивают необходимую производству производительность процесса из-за низкой эффективности при очистке трудноудаляемой суспензии стекла (мелких остатков стекла) с поверхности обработанного стекла. Это требует дополнительного ее механического удаления, что приводит к образованию царапин на поверхности ошлифованного стекла.
Предлагаемое изобретение направлено на устранение вышеуказанных недостатков.
Технический результат — повышение производительности процесса за счет высокой эффективности предлагаемой СОЖ при очистке поверхности стекла от загрязнения суспензией стекла.
Технический результат достигается предлагаемой СОЖ, которая имеет следующий состав, мас.%: соль полимерных производных аминогуанидинов 0,1-0,3, арабиногалактан 1-1.1 вода остальное.
Арабиногалактан (АГ) природный полисахарид и благодаря хорошим поверхностно-активным свойствам может применяться, как стабилизатор эмульсий (Антонова Г.Ф., Тюкавкина Н.А. Водорастворимые вещества лиственницы и возможности их использования // Химия древесины. 1983. № 2. С.89-96).
Также АГ при добавлении к СОЖ играет роль стабилизатора коллоидной системы при взаимодействии с солями металлов (Kokai M., Nagasaki H. Readily dispersible powder as thickening stabilizer // Pat. 2000014335 A2 Japan 2000. CA 2000. V.132, 63487). Адсорбция АГ к катионам частиц сошлифованного стекла приводит к их агрегации с образованием полимерной стабилизирующей матрицы, что эффективно снижает прочность и повышает пластичность обрабатываемого материала и облегчает его удаление из СОЖ при регенерации.
За счет вышеназванных свойств АГ обеспечивает удаление частиц стекла из зоны обработки и с поверхности инструмента за счет гидрофильного характера полисахарида на границе раздела стекло — агрегат, делает их инактивными (не способными к адсорбции). Это существенно повышает производительность технологического процесса за счет уменьшения времени на очистку частиц сошлифованного стекла с обрабатываемых деталей и повышает качество обработанных поверхностей по сравнению с известными технологиями. Этому способствуют такие его свойства, как высокая растворимость в воде, уникально низкая вязкость растворов, узкое молекулярно-массовое распределение, а также биоразлагаемость.
АГ — является нетоксичным продуктом и рекомендуется к использованию в пищевой промышленности (А.Б. Мулин. Разработка технологии мучных кондитерских изделий с использованием арабиногалактана. Автореферат дисс. на соиск. уч. степени канд. техн. наук, Москва, 1998).
Для проверки эффективности заявляемого состава СОЖ выполнены экспериментальные работы. В таблице приведены составы СОЖ, которые были использованы в экспериментах.
Сравнение моющих свойств (по удалению осколков суспензии стекла из зоны обработки) предлагаемой СОЖ и прототипа при тонком (1 проход) шлифовании представлено в таблице, проводилось на девятишпиндельном станке, предназначенном для обработки еврокромки SZ 9.325. Для отмывки использовалась вертикальная моечная машина YH 1500 LC. Каждый состав СОЖ испытывался при шлифовании не менее 100 штук заготовок.
Таблица | |||
№ | Состав СОЖ, массовые % | Ширина несмываемой зоны, мкм | Качество отмывки |
1 | Вода | 80-180 | Резко выраженный контур капель |
2 | Вода + 0.25 АГ | 80-180 | Нет полной отмывки, контур капли размыт |
3 | Вода + 1.0 АГ | отсутствует | Полная отмывка, появление плесени на 6, 7 день на поверхности СОЖ |
4 | Вода + 0.3 ПОАГ | 100-300 | Нет полной отмывки, контур капли размыт |
5 | Вода + 1.0 ПОАГ | 200-300 | Нет полной отмывки, контур капли размыт |
6 | Вода + 3.0 ПОАГ | 200-300 | Нет полной отмывки, контур капли размыт |
7 | Вода + 1.0 АГ + 0.1 ПОАГ | отсутствует | Полная отмывка, отсутствие плесени в течение 40 дней |
8 | Вода + 1.0 АГ + 0.3 ПОАГ | отсутствует | Полная отмывка, отсутствие плесени в течение 40 дней |
Сравнение результатов (таблица) по применению состава № 3 с рекомендуемым в прототипе составом № 4 показывает, что этот состав хорошо удаляет остатки суспензии с ошлифованного стекла с поверхности стекла, но при хранении в течение 6-7 дней на поверхности состава наблюдается образование плесени. Хорошо отвечают предъявляемым требованиям составы № 7 и 8 стабильные к действию плесени и обеспечивающие высокую эффективность, а следовательно, и производительность при очистке трудноудаляемой суспензии стекла.
В таблице не приведены результаты испытаний составов СОЖ, содержание компонентов которых выходит за указанные в формуле изобретения пределы. Соответствующие параметры процессов шлифования с данными запредельными составами СОЖ были существенно хуже, чем результаты в таблице, либо имели более высокую себестоимость.
На основании результатов испытаний, представленных в таблице, можно сделать вывод, что новый состав СОЖ имеет перед составом СОЖ прототипа следующие преимущества:
— обеспечивает повышение производительности за счет отсутствия операции по механическому удалению отлагающейся на поверхности трудноудаляемой суспензии стекла;
— обеспечивает повышение качества обработки за счет уменьшения образования царапин при механическом удалении ошлифованного стекла на 25-30%.
Защитные покрытия для повышения эксплуатационной надежности стеклянной тары
Для изделий массового применения рекомендуется обработка поверхности разнообразными пленкообразующими веществами. В результате контакта этих веществ с поверхностью стекла создается защитное покрытие, исключающее наведение новых дефектов и уменьшающее разупрочняющее действие существующих на поверхности стекла микротрещин.
Разработаны различные способы формирования поверхностных пленок. Каждый из них позволяет осаждать разнообразные материалы, отличающиеся свойствами и назначением. Образование пленок происходит в результате химической реакции, химического осаждения из газовой среды, вакуумного испарения, катодного распыления или механическим нанесением.
Химическая реакция, происходящая между исходной поверхностью и средой, дает тонкий слой нового вещества на поверхности. Химическое осаждение из газовой фазы связано с химической реакцией между двумя или более веществами или с химическим разложением (пиролизом).
Вакуумное испарение вещества начинается при значительном снижении давления в камере (до 0,9 Па), при этом атомы или молекулы движутся прямолинейно, а величина средней длины свободного пробега этих частиц соизмерима с размерами камеры. Для большинства материалов при этом способе нанесения пленок требуется повышать температуру.
Катодное распыление производится с поверхности катода, бомбардируемого ионизированными частицами, которые отдают свою энергию атомам или молекулам катода и выбивают их. Выбитые частицы осаждаются на соседнюю поверхность и образуют на ней тонкую пленку.
Механическое нанесение является наиболее простым способом. После нанесения пленки изделие подвергают обработке, обеспечивающей однородность свойств пленки.
Из других методов пленкообразования следует отметить облучение органических молекул, адсорбированных поверхностью, термическое расщепление полимерных соединений с получением реактивных свободных радикалов, полимеризующихся вторично при соприкосновении с поверхностью, метод электрического разряда, метод электрохимического распыления.
Перечисленные методы в той или иной мере находят применение для упрочнения стеклянной тары.
Наиболее распространены способы создания на стеклянной таре пленок окиси олова и титана. Эти способы продолжают совершенствоваться. Например, предусматривается обработка бутылок сразу после формования при температуре 400-650° С 10%-ным раствором четыреххлористого олова в спирте, например изопропиловом. Присутствие около 0,5% четыреххлористого титана или бутилата титана в пленке повышает ее устойчивость к щелочам.
Если пары четыреххлористого олова с температурой 20° С и сухой воздух подавать под давлением на поверхность стекла, имеющего температуру около 700° С, то получающееся покрытие из окиси олова, по данным исследователей, вступает в реакцию с поверхностью стекла. При этой температуре трещины Гриффитса, возникающие при охлаждении стекла, не успевают образоваться.
По другому методу бутылки сразу же после формования покрывают 4%-ным раствором четыреххлористого олова в изопропиловом спирте. При прохождении через лер на них образуется диффузный слой окиси олова. Далее бутылки обрабатывают парами четыреххлористого олова или покрывают раствором окиси олова при температуре не ниже 450°, а затем водным раствором полиоксиэтиленгликоля или полиэтилена при температуре 80-180° С.
Для предотвращения электрохимической коррозии корончатых крышек, контактирующих с пленкой окиси олова, предлагается добавлять в обрабатывающий раствор, содержащий 5% олова, такие соединения, как ацетилацетонат марганца или хрома. Наличие этих соединений снижает способность материалов к химическому взаимодействию.
Обработка тонкостенной стеклянной тары производится в интервале между низшей температурой отжига и температурой размягчения стекла. При этом стекло подвергается воздействию кислого газа, например хлористого водорода, чтобы вывести из стекла ионы натрия. Соль натрия с поверхности изделия смывается или удаляется путем сублимации при определенных условиях. Затем стекло обрабатывают смесями, содержащими олово.
Такое стекло с внутренней стороны останется неизменным, затем будет идти слой высококремнеземистого стекла и, наконец, слой окиси олова. Общая толщина слоев около 10 мкм.
Применение четыреххлористого олова оказалось одним из наиболее эффективных методов упрочнения стеклянной тары в промышленных условиях. Этим процессом легко управлять, он недорог, его легко усовершенствовать для повышения эффективности. Такой метод широко применяется для упрочнения одноразовой и многократно используемой стеклянной тары во многих странах. Испытания бутылок, упрочненных четыреххлористым оловом, показали, что их гарантированная прочность увеличивается примерно на 196 кПа при проверке на внутреннее гидростатическое давление, причем такие бутылки демонстрируют высокую эксплуатационную надежность на линиях розлива.
Имеется опыт упрочнения облегченных бутылок вместимостью 0,33 л, массой 130 г, с толщиной стенки 1,8 мм. Непосредственно после формования поверхность бутылок подвергают обработке легкоиспаримой жидкостью четыреххлористого олова с точкой кипения 114° С. В сухой атмосфере пары SnCl4, взаимодействуя с горячей поверхностью стекла, образуют на ней термостойкий слой SnО2 толщиной 5-80 нм. Слой увеличивает способность поверхности стекла противодействовать нанесению царапин, т. е. повышает микротвердость стекла. За счет заполнения поверхностных дефектов и микротрещин поверхностного слоя увеличивается прочность и химическая устойчивость стеклоизделий. При оптимальных условиях прочность возрастает на 25-30%.
После нанесения окиснометаллического покрытия и отжига на поверхность бутылки напыляют 0,1-0,5%-ные водные растворы или эмульсии органических веществ. В виде водных растворов применяют стеараты, в виде эмульсий — полиэтилен, олеиновую кислоту, озокерит. Напыление производят при температуре 100-150° С. В результате на поверхности образовывалась нерастворимая маслянистая пленка.
Для холодных покрытий применяются также различные смолы, щелок, сложные эфиры монтановой кислоты с этандиолом или 1,3-бутандиолом, щелочные соли олеиновой кислоты, глицериновый моноацетат, синтетические тяжелые парафины, полиэтилен, полипропилен и полиолефины с малой молекулярной массой, полиэтиленгликоль, содержащий максимум 0,2% моноэтиленгликоля, сложные полимеры на основе эфиров акриловой кислоты с одновалентными алифатическими насыщенными спиртами, акриловая кислота, акрилонитрил (цианистый винил) и стирол, смачивающие реагенты на основе полингликолевого эфира; в качестве добавок используются олеиновая и стеариновая кислоты, гидроокись калия, сорбированный калий (до 0,05%) и особые эмульгаторы.
Вещества, применяемые в качестве холодного покрытия, не должны оказывать влияния на вкусовые качества и запах пищевых продуктов.
Во многих случаях рекомендуется наносить окиснометаллические покрытия из органических растворов. В частности, пленка окиси олова образуется при напылении на поверхность бутылок после формования и отжига растворов хлористого олова в органическом растворителе, причем в растворе должны быть также тетра-н-бутоксид титана, трихлорид висмута, тетрахлорид титана или растворов четыреххлористого олова с н-бутилацетатом.
Широко используются металлоорганические соединения. Для создания надежного покрытия на стекле применяют титансодержащие органические соединения, железоорганические соединения, неводный инертный раствор титансодержащего эфира, гидролизуемый органический титанат и др.
Органические соединения наносят на поверхность стеклянной тары для предотвращения повреждения ее поверхности и сохранения высокой природной прочности стекла. В качестве таких пленкообразующих растворов используют водный раствор винилалкоксисилана, малеиновой кислоты и винилового эфира жирной кислоты, рН которого регулируется добавкой гидроокиси алюминия до рН 6, и др. Смесь, растворенная в кипящей воде, наносится погружением или напылением на поверхность стеклоизделия, нагретого до 49-66° С.
Органические покрытия чаще всего наносят методом погружения. Бутылки, закрепленные за горло, подаются конвейером в ванну с пленкообразующим раствором, затем бутылки переворачиваются и перемещаются в зону, где снимается избыток раствора, и далее следуют в зону сушки. Избыток раствора снимают обтирочным элементом, содержащим растворитель.
Одними из самых первых пленкообразующих растворов служили кремнийорганические соединения, которые не потеряли своего значения и до настоящего времени. Для упрочнения стеклянной тары применяют различные кремнийорганические жидкости, которые распыляют на изделия при температурах около 200° С. В качестве таких веществ применяют дисперсию гидролизуемого эфира кремнекислоты и дисперсию силиконового масла; полиорганосилоксановые соединения; смесь диметилдихлорсилана, метилтрихлорсилана и коллоидного кремнезема и др.
Водостойкие покрытия на поверхности стекла, характеризующиеся повышенным сопротивлением царапанию и длительным сроком службы, получают в результате обработки водным раствором (NH4)3ZrOH(СО3)3 и низкомолекулярного полиэтилена (молекулярная масса 1200-2000) с дисперсностью коллоида. Обработку проводят погружением или пульверизацией после выхода изделий из печи отжига при температуре 60-120° С.
Однако особенно эффективным оказалось двухстадийное нанесение защитных покрытий. Наиболее часто употребляется сочетание обработки неорганическими или органическими солями металлов при высоких температурах (сразу же после формования) и последующего нанесения органических защитных пленок.
Такие двухслойные покрытия получаются при последовательном нанесении оловосодержащих соединений и смазывающих органических соединений; титансодержащего пиролизующегося при температурах 370-670° С соединения и органической пленки; двуокиси олова или титана и продукта реакции поливинилового спирта и моностеарата полиоксиэтилена; соединений титана, циркония, олова, ванадия и органического полиизоционата и др.
Для повышения стойкости к механическим повреждениям и химической устойчивости рекомендуется на поверхность бутылок при температурах 560-700° С наносить из паровой фазы неорганические соединения олова — хлориды и фториды — или органические соединения олова — диэтилизобутил, двухбромистое, диизопропил, а после отжига при температуре около 120° С распылением создать органическую пленку полиэтилена, моностеарата полиоксиэтилена, стеарата триэтаноламина или их смеси.
Иногда рекомендуется сочетание двух пленок на основе органических соединений. Например, на изделие наносят тонкий слой моностеарата полиоксиэтилена, а затем все изделие или его отдельные части защищают полиорганосилоксановой смолой.
Устойчивое покрытие на бутылках, противодействующее высоковлажностным условиям, формируют из грунтовки, состоящей из смеси аминоалкилалкоксисилана, неэтерифицированной эпоксидной смолы и полиметилметакрилата (силан в смеси — не менее 0,05%), и упругого покрытия из виниловой смолы.
Имеются предложения по упрочнению стеклянных банок и бутылок трехслойными покрытиями. Бутылки или банки упрочняются при распылении на них непосредственно после выхода из стеклоформующей машины металлоорганических соединений (продуктов взаимодействия хлоридов олова или титана с органическими соединениями), при последующей термообработке при температуре примерно на 20° С выше верхней температуры отжига и нанесении хлоридов олова или титана при температуре около 450° С путем распыления или испарения, образующих упрочняющие окисные пленки. Затем при температурах 80-180° С изделия покрывают тонким защитным слоем полиэтиленгликоля, моностеарата полиэтиленгликоля или полиэтиленовых эмульсий.
Хотя технологические процессы упрочнения стеклянной тары защитными покрытиями в общем улучшают те или иные ее свойства (повышается прочность, улучшается степень скольжения бутылок), возможно возникновение нежелательных эффектов.
К возможным недостаткам упрочненных бутылок относят ухудшение внешнего вида поверхности стекла, ухудшение адгезии клея при этикетировке и интенсификацию нежелательных электрохимических процессов в поверхностном слое стекла.
Ухудшение внешнего вида поверхности может происходить при горячей обработке тары соединениями олова или титана в результате повышенной отражательной способности поверхности стекла по сравнению с необработанным стеклом. Если подвергнутая обработке оловом поверхность затем полируется открытым пламенем, то поверхность может помутнеть. Ранее считалось, что такое помутнение связано с изменением пленочного покрытия. Однако было установлено, что основная причина этого — выщелачивание поверхности стекла.
При обработке стеклянной тары четыреххлористым оловом увеличивается гидрофобность поверхности стекла, что может ухудшить условия этикетировки в случае применения водорастворимых клеев.
Электрохимические эффекты обусловлены токопроводящими свойствами пленки олова. При практикуемой интенсивности обработки это обычно не имеет значения. Тем не менее, если стеклянная тара укупоривается металлическими крышками, в точках плотного контакта укупорочного изделия со стеклом могут возникнуть триады Sn-О-Fe-стекло. В присутствии воды при высоких температурах, например при стерилизации или пастеризации в автоклаве, могут активно протекать электрохимические процессы. В результате на стекле осаждаются окислы железа, появляются ржавые пятна. Для борьбы с этим явлением применяют специальные присадки, используемые для поверхностной обработки. Не ухудшая полезных свойств покрытия, присадки тормозят электрохимические процессы.
Некоторые производители оборудования применяли для упрочнения бутылок покрытие, которое, однако, смывалось каустиком и горячей водой при мойке перед наливом. В дальнейшем они использовали усовершенствованное покрытие, которое предотвращало износ многократно используемых бутылок и было устойчиво к действию щелочей и горячей воды. Однако это покрытие не рекомендуется применять для упрочнения бутылок, предназначенных для розлива и стерилизации соков и пива, так как пленка нарушается при действии повышенных температур.
Опыт упрочнения стеклянной тары накоплен во многих странах.
Так, установлено, что уменьшение массы бутылок снижает их стоимость, одновременно увеличивая производительность стеклоформующего оборудования. При уменьшении массы изделий на 10% выпуск бутылок на том же оборудовании увеличивается, как показал опыт, на 5%.
При экономии стекломассы, однако, происходит снижение толщины стенок бутылок. С уменьшением толщины, естественно, увеличивается способность бутылок выдерживать резкие смены температур при нагреве и охлаждении, т. е. термостойкость тары повышается. Вместе с тем прочность бутылок при уменьшении толщины стенок снижается. Опыт показывает, что уменьшение толщины стенки для изделий одинаковой формы за счет снижения ее массы в критической зоне на 10 г приводит к снижению сопротивления внутреннему давлению на 0,3 МПа. Изменение толщины дна при тех же условиях вызывает падение прочности бутылок на 0,4 МПа.
При изменении массы бутылок изменяется также высота центра их тяжести, что следует учитывать при оценке инерционной устойчивости тары в условиях эксплуатации.
Компенсация потери прочности в результате снижения массы и толщины стенок стеклянной тары достигается главным образом путем применения специальных методов упрочнения ее поверхности. В некоторых странах бутылки после формования подвергают обработке на горячем конвейере солями олова или титана, при этом их прочность повышается на 30%. В холодной части лера бутылки при температуре 80-100° С обрабатывают стеаратом в основном для уменьшения коэффициента трения стеклянной тары.
До определенного времени для повышения эксплуатационной надежности стеклянной тары в нашей стране использовались пленкообразующие растворы гидрофобизирующей кремнийорганической жидкости.
Силиконовая пленка образовывалась на поверхности бутылок и банок распылением водного раствора 1,5-2,0%-ной концентрации с помощью форсунок, установленных в холодной части печи отжига. Температура изделий при нанесении составляла около 200° С.
По данным исследователей, бой бутылок при транспортировке снижается в 2-3 раза, при мойке — в 2-6 раз, при розливе — в 3 раза; бой упрочненных банок снижается в целом в 4,4 раза.
В некоторых зарубежных странах обработка бутылок силиконами производится после нанесения защитного абразивостойкого покрытия. В других странах с этой целью используют покрытия на другой химической основе.
Кремнийорганические пленки имеют небольшую толщину, легко царапаются и поэтому не могут длительное время сохранять прочность стеклоизделий, особенно в условиях активного воздействия абразивных частиц или при контактировании с другими твердыми телами.
В нашей стране были проведены углубленные исследования процессов пленкообразования, определена эффективность упрочнения стекол и разнообразных стеклотарных изделий при обработке органическими и неорганическими соединениями.
Для нанесения на поверхность стекла использовались эпоксидные смолы ЭД-5, Э-41, Э-181, ЭД-П и кремнийорганический лак К-47К. Покрытия наносились методами погружения, напыления на холодную или нагретую поверхность и струйного распределения. Наилучшее качество пленок на поверхности изделий, как выяснилось, достигается при их погружении в раствор пленкообразователя. При напылении и струйном распределении покрытия имели повышенное светорассеяние, рельефность, натеки. Растворителями служили ацетон, ксилол и их смеси.
Окиснометаллические покрытия создавались на поверхности стеклоизделий путем аэрозольного нанесения на нагретую до 500-700° С поверхность водных и спиртовых растворов хлористых солей олова, железа, титана. Пленки окиси олова на стекле получали также при обработке изделий парами безводного четыреххлористого олова.
Все исследованные покрытия повышают гидрофобность стекла. Наиболее эффективен в этом отношении лак К-47К. Гидрофобизирующее влияние эпоксидных смол снижается с уменьшением содержания эпоксидных групп в смолах. Гидрофобность окиснометаллических пленок ниже, чем у органических.
Истираемость, или абразивная устойчивость, органических пленок оказалась ниже, чем у обычного стекла. Напротив, окиснометаллические пленки повышают сопротивление истираемости поверхности стекла.
Толщина органических пленок превышает толщину окиснометаллических покрытий в 50-100 раз.
Механизм упрочняющего влияния защитных покрытий заключается в следующем:
во-первых, покрытия повышают водоотталкивающую способность поверхности стекла.
Такая гидрофобизация стекла снижает разупрочняющее действие поверхностно-активных сред и прежде всего, влаги воздуха;
во-вторых, поверхность стеклоизделий предохраняется пленками от наведения очагов хрупкого разрушения — микротрещин, т. е. консервируется поверхность стекла;
в-третьих, покрытие уменьшает концентрацию напряжений при разрушающих механических нагрузках, т. е. действует как протектор.
Кремнийорганические покрытия имеют высокую гидрофобизирующую способность, низкую консервационную способность и обеспечивают низкую протекторную защиту поверхности. Такие пленки абразивонестойкие и тонкие.
Органические покрытия упрочняют обычное стекло в 2-3 раза. Однако такие покрытия неэффективно применять для стеклянной тары многократного использования, так как они неустойчивы к механическим и химическим воздействиям. Их вполне успешно можно применять для флаконов и бутылок одноразового использования.
При этом могут быть получены покрытия с высоким светопропусканием, а также пленки, создающие эффект матирования («мороза»), и окрашенные покрытия.
Окиснометаллические покрытия отличаются высокой устойчивостью к абразивному повреждению и к химическим воздействиям. Такие пленки повышают прочность изделий на 20-50%.
Сравнение свойств стекла с пленками окислов олова, титана и железа показывает, что наиболее эффективно для упрочнения применение газообразных четыреххлористого олова и титана.
Хлорид железа хотя и дает толстую пленку, но из-за ее островной структуры не обеспечивает существенного увеличения гидрофобности и прочности поверхности стекла.
Напротив, пленка окиси олова значительно повышает прочность изделий (бутылок для сладких газированных напитков) при статических и динамических нагрузках. Так, при одинаковом внутреннем давлении и ударе с заданной энергией число бутылок, выдержавших испытания, увеличивается на 40% после их обработки четыреххлористым оловом.
Сравнительные динамические испытания неупрочненных и упрочненных бутылок для безалкогольных напитков и парфюмерных флаконов показали, что наивероятная прочность при ударе после нанесения покрытия ЭД-5 возрастает более чем в 4 раза. Такое покрытие обеспечивает более высокую прочность изделий и после многократных ударных воздействий, и в том случае, когда тара наполнена водой, и после длительного пребывания в моечной машине. Окиснометаллические пленки также повышают прочность бутылок при ударе.
Была разработана конструкция установки для нанесения на бутылки защитного покрытия окиси олова из паровой фазы.
Установка содержит осушитель воздуха, парообразователь, узел рециркуляции паровоздушной смеси и камеру напыления. С целью создания равномерного упрочняющего покрытия и уменьшения расхода реактива камера имеет щелевидные нагнетательные раструбы с заслонками.
Установка работает следующим образом. Сжатый воздух от заводского компрессора через ресивер подается шлангом в осушитель, наполненный цеолитом (или силикагелем). Осушенный воздух по трубопроводу под давлением 0,15-0,4 МПа поступает в парообразователь, наполненный через штуцер жидким четыреххлористым безводным оловом.
Воздух барботирует через жидкое четыреххлористое олово, образуя газообразное четыреххлористое олово, которое под давлением направляется в систему рециркуляции, включающую нагнетательный и отсасывающий трубопроводы, вентилятор и электромотор. Паровоздушная смесь через раструбы с заслонками поступает в камеру напыления, установленную на конвейере, транспортирующем бутылки от стеклоформующей машины к отжигательной печи. По направлению движения в камере напыления устроены входное и выходное отверстия, размеры которых соответствуют габаритам обрабатываемых изделий.
Непрореагировавшая паровоздушная смесь отсасывается из камеры и снова подается через рециркуляционную систему в камеру с добавлением к паровоздушной смеси необходимого количества SnCl4.
Чтобы исключить попадание паров четыреххлористого олова в атмосферу цеха, вблизи торцевых отверстий на крышке камеры установлены отсасывающие трубы регулируемой принудительной вытяжной вентиляции. Для улучшения гидродинамики потоков газов в камере устанавливаются зонт-отражатель и отсекатель. Обязательным условием успешной эксплуатации установки является герметичность всех ее узлов и соединений.
Стендовые и сравнительные промышленные (при транспортировке и на линии розлива) испытания показали, что бутылки, обработанные на горячем конвейере парами четыреххлористого олова, имеют более высокую, чем у исходных бутылок, прочность при внутреннем давлении и при ударе, высокую термостойкость. При транспортировке и на производстве потери упрочненных бутылок снижаются в 4 раза, а на линии розлива — в 3,5 раза по сравнению с потерями обычных неупрочненных бутылок того же завода.
В нашей стране были выполнены комплексные работы по созданию технологии, оборудования и подготовке к промышленному внедрению технологии повышения эксплуатационной надежности стеклянной тары.
В частности, была разработана оригинальная конструкция установки НОМ для упрочнения стеклянной тары окиснометаллическими покрытиями.
Как показали стендовые испытания бутылок, обработанных сухими парами четыреххлористого олова с помощью установки НОМ-2, гарантированная прочность пивных бутылок при внутреннем давлении составляет 1,2 МПа, термостойкость повышается с 35 до 45° С, вероятность разрушения при ударе уменьшается на 50%.
Бутылки для шампанского, покрытые пленкой окиси олова, выдерживают внутреннее давление 2,1-2,3 МПа и перепад температур при испытании на термостойкость 40° С. Такие же бутылки без пленки выдерживают внутреннее давление 1,4 МПа и перепад температур 35° С.
На некоторых предприятиях было осуществлено промышленное внедрение технологии упрочнения парфюмерных флаконов путем их обработки парами четыреххлористого олова. С этой целью была использована установка простейшей конструкции, в камеру которой сухие пары SnCl4 поступают по двум перфорированным трубкам, расположенным вдоль ленты горячего конвейера.
Парфюмерные флаконы с пленкой окиси олова имеют высокую прочность при статических и динамических нагрузках, улучшенный товарный вид за счет повышенной отражательной способности их поверхности.
Технология упрочнения стеклянной тары окиснометаллическими покрытиями успешно внедряется на ряде заводов страны. Одновременно для осуществления такой технологии создаются и другие кoнcтpукции установок.
Интересно сочетание пленкообразования и ионного обмена. Бутылки после формования обрабатывают олово-, титан-, цирконийсодержащими веществами, а затем наносят распылением водный раствор соли калия. Изделие выдерживают при температуре, близкой к температуре его пластической деформации, в течение времени, достаточного для замещения ионов натрия на ионы калия. Далее изделия охлаждают, промывают для удаления солей калия и распылением на поверхность наносят слой полимера.
Возможны сочетания закалки и последующего травления, травления и последующей закалки, травления и нанесения защитных покрытий и др.
Хорошие результаты получены при упрочнении бутылок сначала парами четыреххлористого олова с целью создания защитного абразивостойкого покрытия, затем ионообменной обработкой солями калия через нанесенное покрытие и обработкой поверхности органическими соединениями. Бутылки после такой обработки сохраняют эффект упрочнения после неоднократного промывания в 5%-ном щелочном растворе.
Улучшение эксплуатационных свойств стеклянной тары способствует повышению производительности оборудования пищевых производств, снижению потерь стеклянной тары и расфасовываемых в нее пищевых продуктов, улучшению сохранности пищевых продуктов при повышенной химической устойчивости и оптимизации светозащитных свойств стекла, улучшению товарного вида продукции, уменьшению массы стеклотарных изделий и повышению производительности стеклоформующего оборудования.
Значительный вклад в совершенствование стеклянной тары вносит повышение ее прочностных свойств. Работы по упрочнению всевозможных видов стеклянной тары различаются преследуемыми целями. Парфюмерные флаконы подвергаются дополнительной обработке с целью снижения боя при транспортировке, уменьшения толщины стенок и массы, изменения коэффициента отражения поверхности.
Флаконы являются тapoй одноразового использования, поэтому для них могут применяться не только абразивостойкие неорганические покрытия, но и разнообразные органические соединения, создающие декоративный эффект матирования, или «мороза».
Бутылки пивные обрабатываются с целью повышения их прочности на внутреннее давление и удар, а также термостойкости при перепадах температур 40-45° С вместо 35° С. Для внедрения технологии упрочнения пивных бутылок важным фактором является возможность снижения их массы. Это позволит увеличить выпуск таких бутылок на действующем стеклоформующем оборудовании и снизить их себестоимость. Покрытия на таких бутылках должны быть абразивостойкими и служить в течение многократного обращения изделий.
Главной задачей дополнительной обработки бутылок для шампанского является повышение их прочности на внутреннее гидростатическое давление до 1,96-2,45 МПа (20-25 кгс/см2) вместо 1,37-1,66 МПа (14-17 кгс/см2), принятых в стандарте. Эффект упрочнения бутылок должен сохраняться, по крайней мере, на всех этапах первого цикла обращения — от момента отгрузки со стеклозавода до использования их потребителем.
Такие бутылки повторно используются для розлива тихих вин, что не требует столь высоких прочностных показателей бутылок. Бутылки других типов для пищевых жидкостей и банки для консервов целесообразно упрочнять с целью снижения их боя при транспортировке и на производстве, необходимо повышать прежде всего их прочность при ударе, а также термическую устойчивость.
пропорции и инструкция по применению
Жидкое стекло — это химическое вещество, разработанное для добавления в бетон или обработки его поверхности. Как и другие подобные средства, оно используется для улучшения характеристик монолитных конструкций.
С помощью этой присадки можно влиять на скорость схватывания бетонной смеси, а также свести к минимуму разрушительное действие внешней среды.
Отвечая на вопрос, зачем в бетон добавляют жидкое стекло, прежде всего необходимо разобраться в том, что представляет собой эта добавка.
Что такое жидкое стекло для бетона
Термин «жидкое стекло», который часто используют строители, знаком многим. Однако у большинства людей имеются лишь самые приблизительные сведения о составе и способах его применения.


Средство в расфасовке от 1кг до 200 литров можно найти в магазинах строительных материалов. На вид это тягучая светлая жидкость, иногда имеющая желтоватый или зеленоватый оттенок. По химическому составу добавка представляет собой раствор щелочных силикатов. Отличие жидкого стекла от обычного заключается в том, что при его синтезе не вводится кальций, который заставляет сплав быстро отвердевать. Полученную при высокой температуре смесь кремния и щелочного металла разбавляют водой, что позволяет веществу оставаться в текучем состоянии, пока оно хранится в закрытой таре. На воздухе влага испаряется из смеси, в результате чего она твердеет.
Свойства добавки и область ее применения зависят от металла, который входит в химическую формулу вещества. Известны следующие виды силикатных средств:
- Натриевое. Хорошо себя зарекомендовало как гидроизоляционный материал для подземных бетонных конструкций. Применяется как антисептическое, противокоррозийное средство, помогает склеивать части конструкций, устранять трещины.
- Калиевое. Подходит для защиты бетона от кислотного воздействия, придает ему огнеупорные свойства. Используется как клей для плитки, добавляется в строительные растворы, смеси для наружной отделки здания.
- Литиевое. В строительстве используется редко, подходит для защиты поверхностей от высоких температур.
- Смешанное. Включает в себя калиевую и натриевую составляющие. Свойства зависят от пропорций смеси.
Все виды ЖС не имеют запаха, нетоксичны. В качестве растворителя используется вода.
Для чего добавляют жидкое стекло в бетон
Для изменения свойств бетона с помощью силикатов существует два метода:
- добавление жидкого стекла в бетонный раствор на этапе его замешивания;
- нанесение вещества на поверхность готовых конструкций.
После укрепления жидким стеклом бетон приобретает следующие свойства:
- защиту от воздействия воды. Силикатная добавка заполняет все пустоты внутри монолитной конструкции, препятствуя проникновению влаги;
- термостойкость. Вещество не разрушается при высокой температуре и предохраняет от нее обработанную поверхность. Поэтому цементный раствор с этой присадкой подходит для выкладывания печей и каминов;
- ускоренное застывание. Время отвердевания зависит от того, сколько стекла содержится в растворе бетона. Для быстрой заделки отверстий применяют высокую концентрацию ЖС;
- устойчивость к кислотам. Агрессивное воздействие различных кислот на бетонные конструкции снижается, если поверхность обработана силикатным раствором.
При изготовлении модифицированного бетона с применением жидкого стекла крайне важно соблюдать пропорции ингредиентов.
Способы применения жидкого стекла для бетона
Для гидроизоляции монолитных конструкций жидким стеклом используют наружный и внутренний метод его введения. Выбор делают с учетом того, какие характеристики должен приобрести материал. Кроме этого, приминают во внимание условия его дальнейшей эксплуатации.
Внешняя обработка
Жидкое стекло, нанесенное поверх бетона, пропитывает его наружные слои, оставаясь в мельчайших порах. После застывания силикат запечатывает все отверстия. Частицы влаги не могут проникнуть внутрь, поскольку после кристаллизации ЖС уже не растворяется водой. Таким образом, бетон за
Жидкое стекло для бетона и цементного раствора: для чего добавляют, пропорции
Содержание статьи:
Для улучшения эксплуатационных характеристик бетона в раствор включают различные пластификаторы и добавки. Использование жидкого стекла – один из способов увеличить влагостойкость цементной смеси.
Жидкое стекло для бетона и цементного раствора
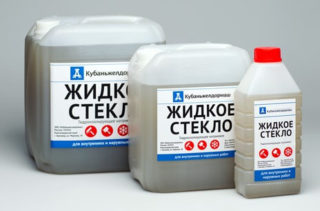
Жидкое стекло – это щелочной раствор силикатов натрия, калия или лития
Жидкое стекло (ЖС) – это щелочной раствор силикатов натрия, калия или лития. Состав хорошо известен как силикатный клей. Вязкая смесь при высыхании образует прозрачное влагонепроницаемое покрытие. Свойства добавки зависят от химического состава основы:
- Натрий – обеспечивает антикоррозийные, водоотталкивающие и антисептические характеристики.
- Калий – защищает бетон от воздействия кислот и открытого огня.
- Литий – используется для противодействия высокой температуре, применяются реже других металлов.
- Комбинированный состав натрия и калия в правильных пропорциях придает смеси положительные качества обоих веществ.
Бетонный раствор отличается прочностью, морозостойкостью и долговечностью. В процессе эксплуатации его прочностные характеристики ухудшаются из-за воздействия осадков и грунтовой влаги. По капиллярам, имеющимся в материале, вода поднимается вглубь. При замораживании она расширяется и создает трещины.
Чтобы предотвратить процесс, выполняется гидроизоляция конструкций. Обработка бетона жидким стеклом – один из способов защитить его от влаги. Состав заполняет поры, препятствует поглощению воды. Такой способ широко применяется при обработке стен и пола, расположенных ниже уровня земли, для оснований, подтопляемых грунтовыми водами.
Калиевая и комбинированная смесь добавляется для повышения устойчивости цементного раствора к тепловому воздействию. Модифицированный состав незаменим при кладке печей, каминов и дымоходов. Также жидкое стекло помогает противостоять разрушительной реакции при контакте с кислотной средой.
Сфера и особенности применения
Силикатный раствор применяют в строительных и ремонтных работах, производстве бетонных конструкций. Основная сфера использования:
- Гидроизоляция фундамента, перекрытий, пола, стыков стеновых конструкций.
- Ремонт и придание водоотталкивающих свойств поверхности бассейнов, канализационных сетей, колодцев.
- Добавление в цементный раствор при изготовлении искусственного камня для ускорения схватывания и повышения прочности.
- Оштукатуривание поверхностей, подвергающихся действию высокой температуры (камины, дымоходы).
Среди достоинств жидкого стекла:
- Отличная адгезия с различными стройматериалами (дерево, бетон). Получается гладкая поверхность с влагостойким свойствами.
- Добавление в состав бетонного раствора при устройстве монолита повышает прочность конструкции.
- Силикатная присадка обладает антисептическими свойствами, предотвращает развитие плесени.
- Доступная стоимость, состав дешевле полимерных добавок, применяемых для гидроизоляции фундамента и бетонных конструкций.
- Простота применения – силикатное стекло легко наносится на любую поверхность или добавляется в смесь.
Быстрое застывание требует ускорения рабочего процесса. Необходим точный расчет пропорций, иначе раствор не будет иметь желаемых качеств. При высокой концентрации жидкого стекла бетон становится хрупким.
Способы применения жидкого стекла
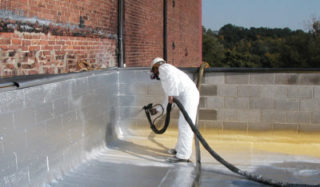
Внешняя обработка бетона жидким стеклом
Повысить влагостойкость и огнеупорность бетона можно двумя способами.
Внешняя обработка
Влагозащитный состав при нанесении на поверхность бетонной конструкции проникает в мельчайшие отверстия и кристаллизуется там. Он препятствует попаданию внутрь материала влаги, защищает от действия кислот и других агрессивных составов. Штукатурка с силикатной добавкой увеличивает теплоизоляционные характеристики стен. Антисептические качества ЖС не дают плесени и грибкам селится на стенах и полуподвальных помещений. Обрабатывать раствором силиката можно фундамент любого типа, бассейн из бетонной чаши, цоколь.
Добавление в состав бетона
Нанесение пропитки защищает наружную часть конструкции, чтобы улучшить гидрофобные характеристики всей массы бетона, жидкое стекло добавляют в раствор. Максимальное количество не должно превышать 10%. Избыток добавки приводит к скорому разрушению конструкции. Приготовление бетонного раствора с силикатами всегда происходит небольшими порциями, чтобы их можно было использовать до начала кристаллизации.
Предварительная подготовка и общие рекомендации
До нанесения гидроизоляционного слоя поверхность очищают от старого покрытия, устраняя шелушение и загрязнение. Процедура обеспечит более глубокое проникновение влагозащитного состава. Обнаруженные трещины следует заделать, выступы удалить. Рекомендуется предварительно прогрунтовать бетонное основание жидким стеклом, разбавленным водой 1:5. Если поверхность, которую изолируют, очень гладкая, для появления шероховатости ее обрабатывают металлической щеткой.
Одно из требований при гидроизоляционных работах – температура воздуха. Она не должна опускаться ниже 5°C. Силикатный состав хранят в емкости, в которую он разлит на заводе. Остаток тщательно закрывают.
При самостоятельном приготовлении раствора необходима информация, через какой промежуток времени схватится смесь. Пропорции жидкого стекла для бетона:
Содержание жидкого стекла | Начальное схватывание, мин | Окончательное застывание, ч |
2-3% | 40-45 | 22-24 |
5% | 25-30 | 13-15 |
10% | 5-7 | 3-4 |
Технология приготовления состава для гидроизоляции своими руками
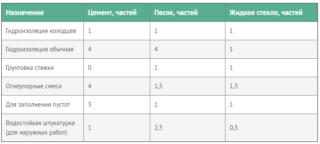
Пропорции цемента, песка и жидкого стекла
Для приготовления раствора потребуется:
- ведро;
- насадка миксер для перфоратора;
- валик или щетка;
- мерная емкость.
Смешивать силикатный и цементный раствор нужно в рекомендованных пропорциях. Чтобы не нарушить инструкцию, удобно пользоваться мерной емкостью. Консистенцию жидкого стекла регулируют добавлением холодной воды. В состав гидроизоляционной смеси также входит цемент и песок. Пропорция для обработки колодцев составляет 1:1:1 (цемент, песок ЖС), для других конструкций берется соотношение 1 л силиката на 10 л бетона.
Сначала замешивают сухие ингредиенты цементного раствора. Затем растворяют необходимое количество ЖС в воде, приготовленной для смеси. Раствор вливается в сухие компоненты при непрерывном размешивании миксером. Можно добавить готовый силикат в бетон, но первый способ обеспечивает более равномерное распределение гидрофобизатора.
Гидроизоляция наносится валиком или макловицей. Соседние полосы должны перекрывать друг друга. При обработке стен и перекрытий используют краскопульт. Им удобнее наносить состав на вертикальную поверхность. Получается равномерное покрытие.
Слой не должен быть толще 3 мм, при необходимости раствор наносится 2-3 раза. Важно дождаться полного высыхания поверхности, затем приступать к дальнейшей гидроизоляции.
Техника безопасности при работе
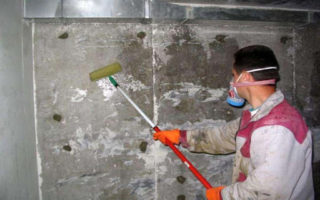
Работать нужно в перчатках и респираторе
Раствор силикатов натрия не является токсичным веществом, но при работе с ним необходимо соблюдать правила:
- Перед началом смешивания составов надевают перчатки и защитный костюм. Попадание каплей жидкого стекла на кожу может вызвать раздражение.
- Опасно соприкосновение состава со слизистыми оболочками. Необходимо избегать попадания в глаза и органы дыхания. В качестве защиты рекомендуются очки и респиратор. При попадании состава в глаза сразу промойте их проточной водой.
- Работы с силикатным клеем ведутся на улице или в хорошо проветриваемом помещении.
- Потеки от силикатной добавки лучше удалять сразу. Она быстро застывает и счищается с трудом. Инструменты тщательно моются после окончания работы.
Воздействие воды и кислоты разрушает бетонные конструкции. Жидкое стекло – эффективное и недорогое средство для гидроизоляции. Оно применимо для различных частей здания, внешней обработки и изменения характеристик цементных растворов.
виды, плюсы и минусы, пропорции, инструкция
В строительной отрасли применяются бетонные смеси, которые после твердения обладают повышенной прочностью. Для выполнения специальных задач в бетон добавляют различные добавки, изменяющие его характеристики. Одним из распространенных компонентов является жидкое стекло для бетона. Оно сокращает продолжительность застывания бетонной смеси, повышает стойкость монолита к воздействию влаги, кислот, повышенной температуре. Важно правильно смешать бетон и стекло, чтобы гарантированно обеспечить требуемые характеристики материала. Рассмотрим детально эту добавку.
Зачем добавлять жидкое стекло в бетонЗнакомимся с материалом
Многие слышали, что в строительной отрасли используют добавку, которая называется жидким стеклом. Однако далеко не все имеют представление, что она собой представляет. Рассматриваемый ингредиент – это растворенные в воде калиевые и натриевые силикаты, полученные из кремнезема. С водным раствором силикатов сталкивались практически все, используя в бытовых целях силикатный клей. Материал визуально воспринимается как вязкая жидкость, имеющая беловато-желтый оттенок. Остановимся на технологии изготовления, в соответствии с которой материал классифицируется по видам.
Общая классификация
Современная технология позволяет получить добавку различными методами. Компонент может производиться путем высокотемпературной обработки кремниевого сырья совместно с водным раствором натриевого гидроксида. Оборудование позволяет получить ингредиент с заданными свойствами путем спекания соды с кварцевыми частицами. Можно также использовать способ смешивания двуокиси кремния с раствором щелочей.
В зависимости от особенностей изготовления получают два вида ингредиентов:
- натриевую смесь, характеризующуюся повышенной адгезией, клеящими свойствами, стойкостью к влиянию атмосферных факторов;
- калиевый состав, отличающийся ускоренным высыханием, а также хорошей устойчивостью к воздействию повышенной температуры.
Добавка в бетон — жидкое стекло натриевоеЭксплуатационные характеристики обоих типов материалов идентичны, но натриевый состав отличается более низкой ценой.
Для чего добавляют жидкое стекло в бетон
Применение силикатного раствора, вводимого в бетонную смесь на этапе приготовления, а также наружная обработка бетонной поверхности изменяет свойства бетона.
После того как введено жидкое стекло, бетон приобретает дополнительные характеристики:
- стойкость к проникновению влаги. Благодаря повышенной водонепроницаемости, монолит, модифицированный специальной добавкой, востребован для фундаментных оснований, подземных сооружений;
- устойчивость к воздействию повышенной температуры. Это позволяет использовать модифицированный цементный состав для изготовления каминов и сооружения печей, кладка которых подвергаются воздействию открытого огня;
- способность застывать за ограниченное время. При повышенной концентрации натриевого силиката в рабочем растворе, бетонная смесь твердеет ускоренными темпами, что важно для заделки различных полостей;
- стойкость к влиянию кислот. Введение силикатного раствора в бетонный состав повышает стойкость к воздействию агрессивной среды, что актуально для использования бетона в химической промышленности.
Для обеспечения требуемых характеристик, смешивая бетон с жидким стеклом, пропорции следует неукоснительно соблюдать.
Жидкое стекло в бетоне – за и против
Так же, как и все строительные материалы, добавка имеет свои достоинства и недостатки.
Что дает при добавлении в бетон жидкое стеклоПреимущества присадки:
- небольшая цена стройматериала;
- незначительный расход присадки;
- устойчивость к атмосферным факторам;
- долговечность защитной пленки;
- простота применения при введении внутрь бетона и поверхностном нанесении;
- хорошая адгезия с минеральными основами.
Кроме того, силикатный компонент обладает:
- повышенными гидрофобизирующими свойствами. В результате создания водонепроницаемого слоя затрудняется впитывание влаги;
- высокими антисептическими характеристиками. Добавка препятствует развитию бактерий, затрудняет рост микроорганизмов;
- антистатическими свойствами. Характеристики силикатной присадки препятствуют накоплению статического электричества;
- способностью герметизировать трещины на поверхности. Это обеспечивает влагонепроницаемость массива;
- устойчивостью к воздействию открытого огня, кислот, повышенной температуры. Обработанный материал сохраняет структуру и свойства.
Наряду с достоинствами, имеются слабые стороны:
- ускоренная кристаллизация модифицированного состава при выполнении мероприятий по гидроизоляции фундаментных оснований;
- невозможность применения для обработки поверхностей зданий, изготовленных из кирпича;
- недостаточно высокие прочностные свойства защитной пленки, которая разрушается при механическом воздействии.
Несмотря на имеющиеся недостатки, присадка широко используется профессиональными строителями, частными застройщиками, домашними умельцами для решения расширенного круга задач.
Применение жидкого стекла в бетоне – области использования
Работники строительной отрасли, ремонтной сферы активно используют силикатные растворы на основе натрия и калия. Они повышают эксплуатационные характеристики монолита, что позволяет использовать его для различных целей.
Области применения силикатного модификатора:
- заделка трещин и полостей, через которые проникает влага;
- внешняя отделка стен здания для повышения их влагостойкости;
- гидроизоляция кладки цокольных помещений;
- влагозащита подвальных помещений, гидротехнических объектов;
- приготовление специальных составов для грунтовки бетонной поверхности;
- сооружение фундаментов для установки отопительного оборудования;
- производство на промышленных предприятиях специальных видов бетона;
- возведение фундаментных оснований различных объектов;
- защита стен жилых и подсобных помещений от развития плесени, грибковых колоний;
- обработка стыков и внутренних поверхностей колодезных колец.
По своим характеристикам компонент практически не имеет аналогов при выполнении работ, связанных с гидроизоляцией и пропиткой. Свойства силикатного материала позволяют обеспечить надежную защиту бетонных конструкций от влаги, повышенной температуры, агрессивной среды.
Сколько жидкого стекла добавлять в бетон – проверенные рецепты
Рассмотрим, какое количество силикатного компонента следует заливать в бетонную смесь для выполнения различных задач.
Для приготовления модифицированных цементных растворов и бетона используйте следующие рекомендации:
- кладочную смесь для сооружения каминов, печей готовят из портландцемента и мелкого песка, соблюдая соотношение один к трем. В песчано-цементную смесь следует залить 18–20% стекла от общего объема смешанных компонентов, после этого добавить воду. Остается все тщательно перемешать до однородного состояния, и готовый раствор можно использовать;
- для приготовления бетонной основы, обладающей влагостойкими свойствами, огнеупорными характеристиками и предназначенной для бытового использования, концентрация присадки не должна превышать одну десятую часть от общей массы. Такой состав также можно использовать для гидроизоляции домашних бассейнов;
- для гидроизоляции стыков колодезных колец и обработки внутренней поверхности готовится состав, состоящий из портландцемента, стекла, просеянного песка. Очень важно соблюдать пропорцию, добавляя ингредиенты в равных соотношениях. При постепенном добавлении воды необходимо добиться сметанообразной консистенции.
При условии соблюдения пропорций бетонный раствор приобретает требуемые свойства.
Жидкое стекло как присадка для бетонаПравильно заливаем жидкое стекло – добавка в бетон не терпит ошибок
Возникают ситуации, когда введение стекла не приносит ожидаемого результата. Это связано с отсутствием практического опыта, несоблюдением пропорций.
Важно придерживаться следующих рекомендаций:
- запрещается вводить силикатную добавку в приготовленный бетонный раствор. Необходимо вначале смешать ингредиенты, затем разбавить стекло водой. Затем необходимо постепенно заливать раствор, тщательно перемешивая;
- контролировать процентное соотношение добавляемых компонентов, не превышать проверенных на практике пропорций. Это гарантирует получение требуемых эксплуатационных свойств бетона.
Помните, что повышенная концентрация силикатного наполнителя, так же как и пониженная, отрицательно влияет на свойства бетона.
Вводим в бетон жидкое стекло – правила работы
Для обеспечения требуемого эффекта от использования присадки необходимо изучить правила работы с силикатной добавкой, а также подготовить необходимые инструменты.
Гидроизоляция жидким стекломДля поверхностной обработки бетонного массива понадобятся:
- широкий валик, позволяющий ускорить нанесение защитного состава;
- кисточка для обработки силикатной смесью небольших площадей и угловых зон;
- металлическая щетка для подготовки обрабатываемой поверхности;
- краскопульт, позволяющий наносить материал при выполнении работ в промышленных масштабах;
- емкость для смешивания ингредиентов и приготовления специальных строительных растворов;
- защитные рукавицы, предохраняющие кожный покров от контакта с силикатным компонентом.
Общие правила работы предусматривают:
- Тщательную очистку обрабатываемой поверхности от загрязнений органического и неорганического происхождения.
- Заделку глубоких трещин и выравнивание поверхности с применением шпатлевки для бетона.
- Послойное нанесение материала с использованием широкого валика, кисти или промышленного краскопульта.
При нанесении покрытия двумя слоями, оно проникает вглубь массива на 1,5–2 мм. Модифицирующий состав не содержит вредных компонентов, однако следует промыть кожу водой при попадании силикатного раствора на ее поверхность. После завершения работ необходимо осмотреть и очистить инструмент от остатков силикатной смеси.
Как покрыть бетонный пол жидким стекломМожно вводить добавку внутрь бетонного раствора на стадии приготовления. Для этого необходимо постепенно добавлять в бетоносмеситель или емкость жидкое стекло для бетона. Инструкция по применению должна соблюдаться для обеспечения требуемых характеристик бетона.
Для приготовления модифицированного бетонного состава потребуются следующие инструменты:
- специальная насадка на дрель, повышающие эффективность перемешивания компонентов;
- емкость для смешивания компонентов с помощью насадки или малогабаритная бетономешалка;
- средства индивидуальной защиты, предохраняющие кожный покров и слизистую оболочку от попадания добавки.
Алгоритм подготовки модифицированного бетонного состава предусматривает следующие операции:
- Дозирование ингредиентов в необходимых соотношениях.
- Добавление водного раствора специальной присадки в бетонную смесь.
- Подготовку бетонной смеси согласно рецептуре.
- Тщательное перемешивание компонентов до однородной консистенции.
Самостоятельно заливая жидкое стекло в бетон, пропорции необходимо строго соблюдать. Превышение предусмотренного рецептурой количества вызовет ускоренное высыхание бетона с появлением трещин. Добавление уменьшенного объема в бетон жидкого стекла не обеспечит требуемых эксплуатационных характеристик.
Заключение
Для обеспечения требуемых эксплуатационных характеристик бетона соблюдайте, вливая жидкое стекло, пропорции для бетона. Руководствуясь рекомендациями профессионалов, соблюдая проверенную на практике рецептуру, можно обеспечить необходимые рабочие свойства монолита. За счет дешевизны силикатной добавки стоимость бетонного раствора возрастает крайне незначительно, а эксплуатационные качества позволяют использовать модифицированный бетон для решения широкого круга строительных задач. Консультация профессионалов поможет избежать ошибок.
Метод сухой обработки
Сухой метод обработки стекла
Уважаемые коллеги!
Разрешите рассказать Вам о новом, запатентованном методе обработки кромки листового стекла
Начиная с 2001 года в г.Н.Новгороде начал проходить испытания и внедряться в производство абсолютно новый метод обработки стекла. До этого момента все производители выпускали станки, которые не могли обходиться без воды, но группа изобретателей- Нижегородцев придумала метод сухой обработки стекла, разработала и запатентовала его применение.
Давайте остановимся более подробно на основных моментах обработки стекла.
Итак, для чего же нужна вода и так ли она не обходима в процессе обработки?
Основными функциями воды в процессе обработки стекла считаются:
- Охлаждение заготовки
- Абсорбирующие свойства воды для удаления частиц в процессе обработки стекла
Рассмотрим каждый из них
Охлаждение заготовки
Действительно, охлаждение заготовки в процессе обработки крайне необходимо. Это обуславливается тем, что при нагреве стекла происходит изменение межмолекулярных связей и стекло может «пойти» мелким бисером или вообще отколоться кусочек стекла. Но так ли необходима здесь охлаждающая жидкость? — Оказывается НЕТ!
Это продемонстрировали инженеры фирмы «Карат», которые впервые создали станок, в котором охлаждение заготовки осуществляется не только с помощью конвекции (специально направленных потоков воздуха внутри станка), но и самой абразивной лентой. Да, да — это не вероятно! Лента, совершая полный цикл за 1/7 секунды успевает охладиться внутренними потоками воздуха и взаимодействует с заготовокй уже в охлажденном состоянии, не увеличивая но поддерживая необходимую температуру в зоне обработки. Таким образом, мы решили проблему охлаждения заготовки без применения охлаждающей жидкости.
Абсорбирующие свойства воды для удаления частиц отработанного стекла
Данное свойство очень важно для обеспечения удаления частиц стекла, которые неизбежно появляются при обработке. Зачем же здесь вода? — а для того, чтобы вода как бы ‘смывала’ остатки стекла. Представляете себе поток воды, смешанный со стекольной пылью? Если через полчаса после обработки, эту смесь не убрать, она превратится в ‘бетонную плиту’, которую Вы не сможете выбить из поддона ни одним молотком!
Более того, вода, попадая на пол или на стены, неизбежно начинает испаряться. Но куда деваться стекольной пыли, которая растворена в воде? — Правильно, она начинает парить в помещении, оседая на Вашей одежде, руках и что более страшно — в Ваших легких.
Как же решили эту проблему наши инженеры?
Очень просто — если нет воды, а стекольная пыль имеет ту же структуру, что и домашняя пыль, нет ничего более лучше, чем удалить её с помощью… пылесоса! Но поставить обычный отсос воздуха было бы по крайней мере непродуктивно — пыль имеет свойство ‘разлетаться’ в разные стороны при попытке захватить её. Поэтому, в конструкцию станков были добавлены ряд нововведений, которые позволили изменить конвекционные потоки внутри станка так, что стекольная пыль образует облако в специальном месте внутри станка и уже оттуда, не взаимодействуя с оператором, спокойно удаляется с помощью мощного пылесоса в двух-контурную систему фильтров.
Как мы видим, проблемы связанные с необходимостью воды, решены нашими инженерами.
Отказ от использования охлаждающей жидкости позволил:
- применить нетрадиционные материалы для изготовления станка и тем самым значительно снизить его рыночную стоимость в сравнении с аналогами;
- использовать недорогие расходные материалы, что значительно снизило расходы в процессе его эксплуатации;
- устанавливать станки в помещениях, необорудованных водопроводом, сливной канализацией, а также в помещениях с пониженной температурой воздуха
Безопасность применения нашего метода подтверждает сертификат Санитарно-Эпидемиологической Службы, который мы получили в 2004 году, пройдя все санитарно-гигиенические тесты во время работы на станках.
Применение жидкого стекла для защиты дерева: как покрывать, пропитка
Дерево – отличных материал для бани, жилых построек. Пиломатериалы отвечают многим требованиям, отличаются удобством монтажа, надежностью. Экологичный материал, обработанный жидким стеклом для дерева, долговечен. Не боится влажности, насекомых, грибков.
Целесообразность обработки дерева
Использование силикатов для обработки дерева оправдано во многих случаях. Древесина с пропиткой более долговечна и огнеупорна, при этом сохраняется декоративность, хорошо видна древесная текстура.
Производители предлагают разнообразное жидкое стекло для дерева, применение смеси практикуется на протяжении двух веков. Современные технологии изготовления пиломатериалов не исключают подобных добавок в процессе производства. ЖС используют для обработки готовых деревянных строений из досок, фундаментов из массива (цельного бруса, кругляка, шпал). Обрабатывать древесину жидким стеклом смогут начинающие строители при возведении частных домов, бань, хозяйственных построек.
По эффективности защиты древесины от влаги покрытие из жидкого стекла превосходит пленки лакокрасочных материалов, ЖС намного дешевле и практичнее.
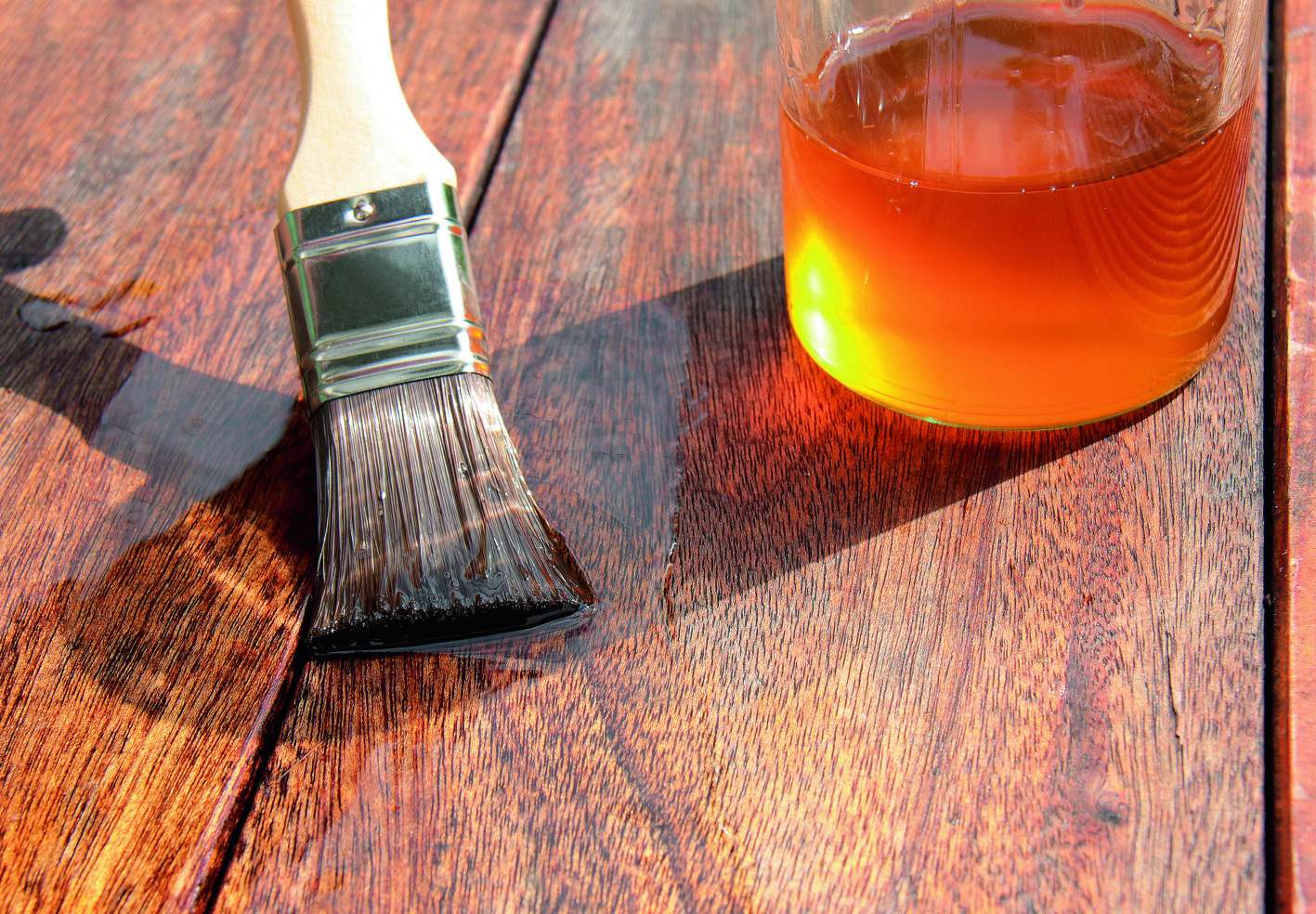
Древесина с пропиткой более долговечна и огнеупорна, при этом сохраняется декоративность, хорошо видна древесная текстура.
Применяют жидкое стекло для обработки всевозможных каркасов, различных конструкций, подверженной интенсивному воздействию негативных факторов. Рекомендуется использовать силикатные смеси для пропитки:
- Окладных венцов;
- Стропил;
- Элементов крыши;
- Лаг для установки пола;
- Деревянных свай;
- Ростверков;
- Конструктивных элементов колодцев.
Если обработать стены подвалов и погребов, не заведется грибок, плесень. Покрытие – надежная защита дерева от гниения при перепаде температур, образовании конденсата. Веранды, террасы и беседки с покрытием из жидкого стекла, сохраняются под воздействием осадков, ультрафиолета. Рекомендуется обрабатывать места прокладки канализационных и водопроводных труб в деревянных зданиях.
После нанесения на поверхность, жидкое стекло заполняет неровности и трещины, происходит структурная стабилизация древесины. На поверхности образуется пленка, не пропускающая влагу.
Покрытие сохраняет защитные свойства до 10 лет. Затем дерево нужно покрывать ЖС снова.
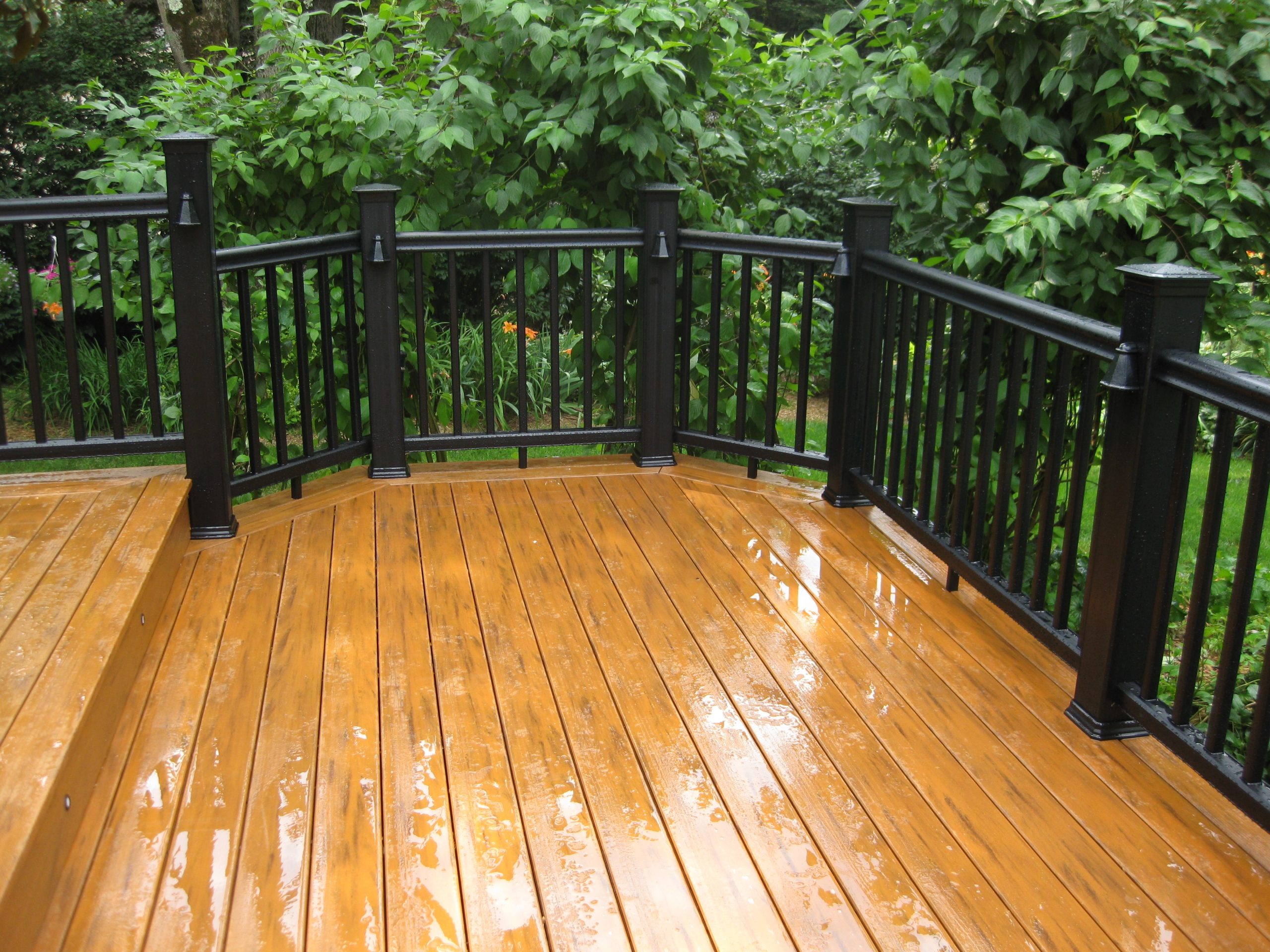
Покрытие – надежная защита дерева от гниения при перепаде температур, образовании конденсата.
Необходимость защиты дерева
Гидроизоляционная пропитка нужна любым лесоматериалам, используемым для каркасов. Без защиты со временем древесина теряет прочность, становится рыхлой. Дерево впитывает из воздуха пары влаги, разбухает, становится питательной средой для спор грибка, плесени. Губительно действует сухой воздух: волокна сжимаются, в структуре лесоматериалов появляются глубокие трещины, надломы. Нагружаемость конструкций значительно снижается.
Еще одна беда – опасность возгорания. По необработанным деревянным каркасам быстро распространяется горение, вскоре все строение будет охвачено пламенем. Когда поры в дереве закупорены, доступ кислорода ограничен.
Образовавшийся защитный слой не обрабатывают, дополнительно не полируют.
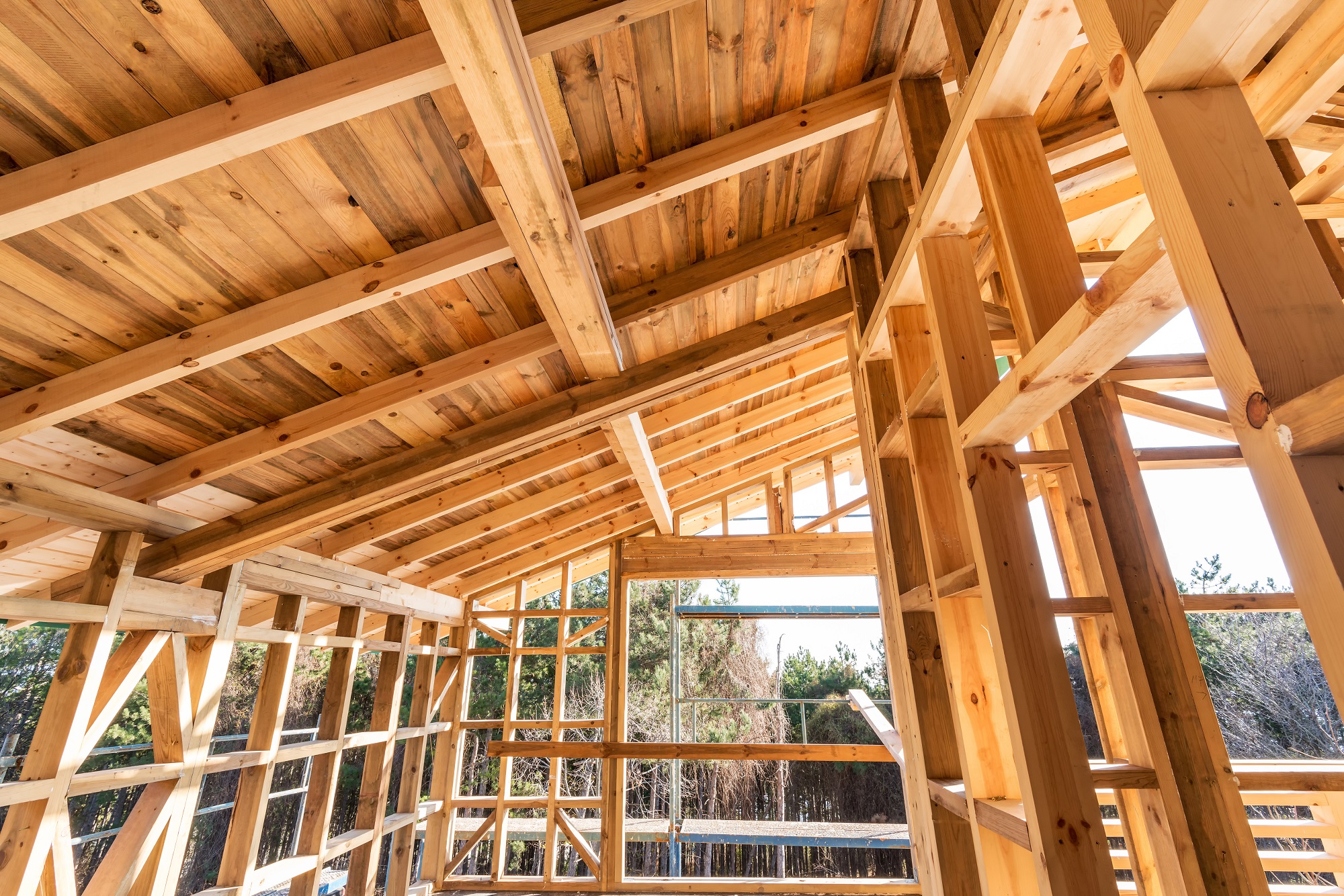
Гидроизоляционная пропитка нужна любым лесоматериалам, используемым для каркасов.
Огнеупорный состав
Для строительных работ выпускают смеси на основе растворимых в воде силикатов натрия, калия, лития. В состав также входит:
- Органические соединения кремния;
- Кремниевая кислота в коллоидной форме;
- Различные присадки, улучшающие состав смеси.
Для огнезащиты приобретают ЖС с маркировкой «огнебиозащита». Смесь обладает свойствами антипирена, при температуре 600-650°С начинает плавиться. Образуемая пленка негорючая, гасит пламя, снижает дымление древесины, препятствует проникновению кислорода. Органосиликатные материалы применяются для обработки внутренних поверхностей в соответствии с правилами пожарной безопасности, по инструкции. Смолистые породы хвойных деревьев сильнее подвержены возгоранию из-за высокого содержания углеводородов, лиственные менее опасны.
ЖС не применяется для огневой обработки поверхностей, для которых предусмотрена финишная отделка ЛКМ.
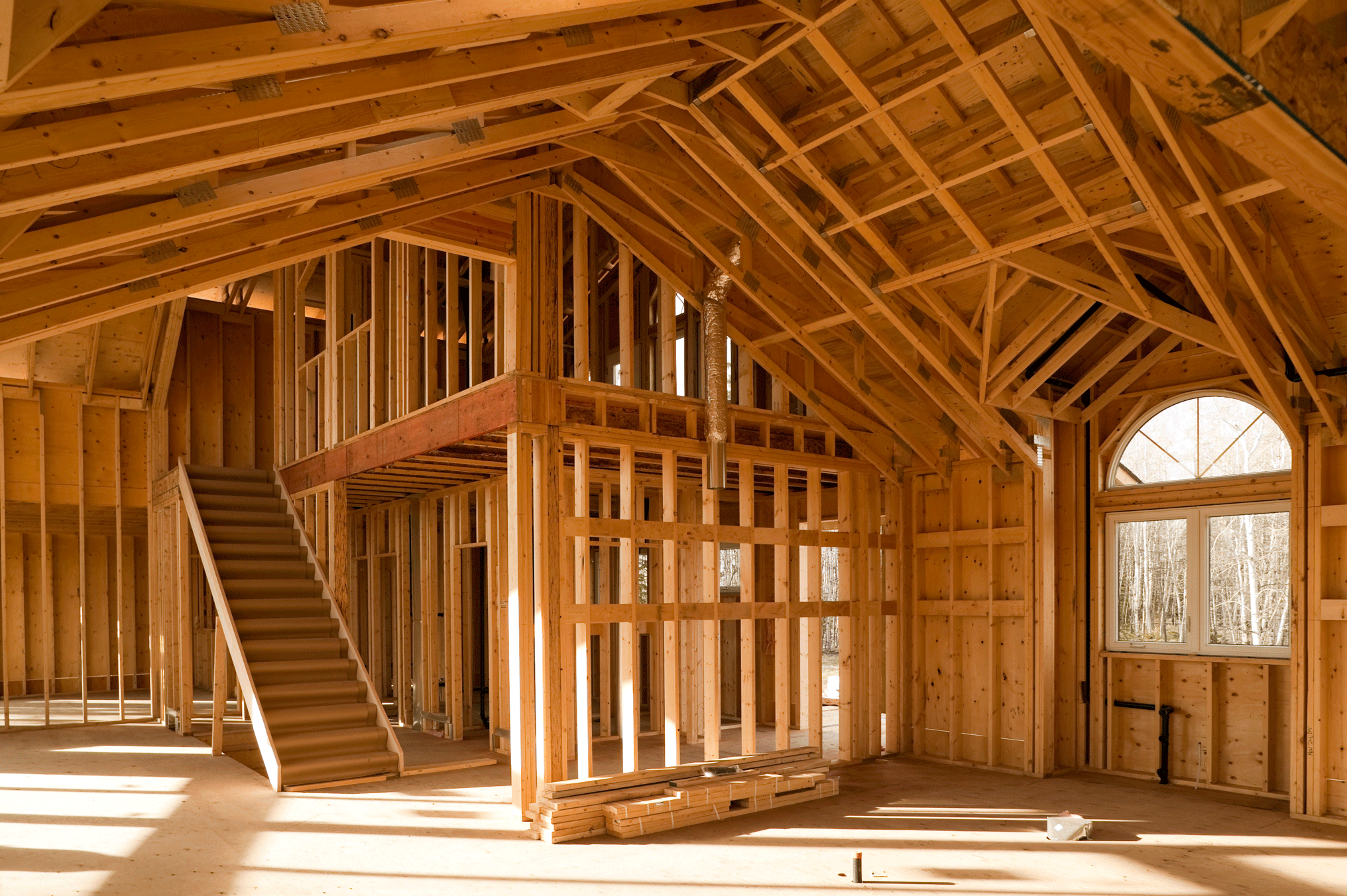
Органосиликатные материалы применяются для обработки внутренних поверхностей в соответствии с правилами пожарной безопасности.
Жидкое стекло для древесины: как приготовить
Прежде, чем покрыть составом пиломатериалы, необходимо прочитать этикетку. Производители указывают пропорции, в которых ЖС разводится. Для обработки древесины жидкое стекло должно обладать определенной проницаемостью, чтобы проникать глубоко, а не оставаться на поверхности. По консистенции рабочий раствор должен напоминать жидкий кисель. Количество воды рассчитывается в зависимости от концентрации. На рынке можно встретить 30-ти и 50% смеси.
Для эффективной обработки состав необходимо наносить два раза. Второй наносится после полного просыхания и отвердевания первого.
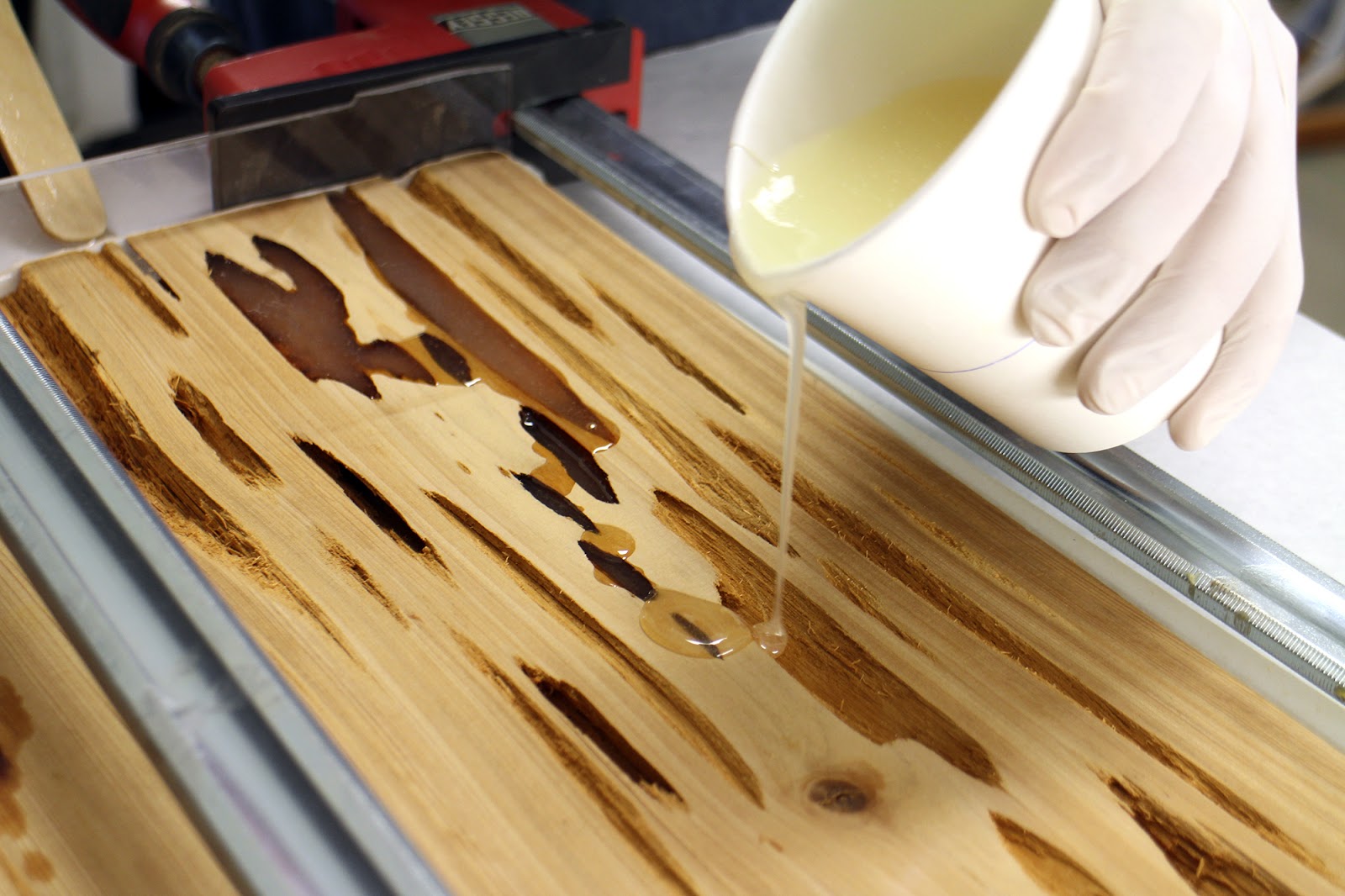
По консистенции рабочий раствор должен напоминать жидкий кисель.
Подготовительные работы
Обработку древесины проводят в защитной одежде и перчатках. Предварительно необходимо зачистить, выровнять обрабатываемую поверхность, удалить остатки стружки, древесной пудры. Жидкое стекло разбавляют в стеклянной или пластиковой посуде чистой водопроводной водой до нужной консистенции.
Поверхность зачищают от отслоившихся волокон, удаляют пыль, остатки стружки и древесной муки. Для минимизации расхода ЖС, усиления прочности конструкций крупные щели целесообразно заполнить грунтовкой.
Жидкое стекло – экологичный материал, тем не менее, при попадании на кожу или слизистые глаза, губ способен вызывать раздражение. В случае попадания смывают ЖС проточной водой.
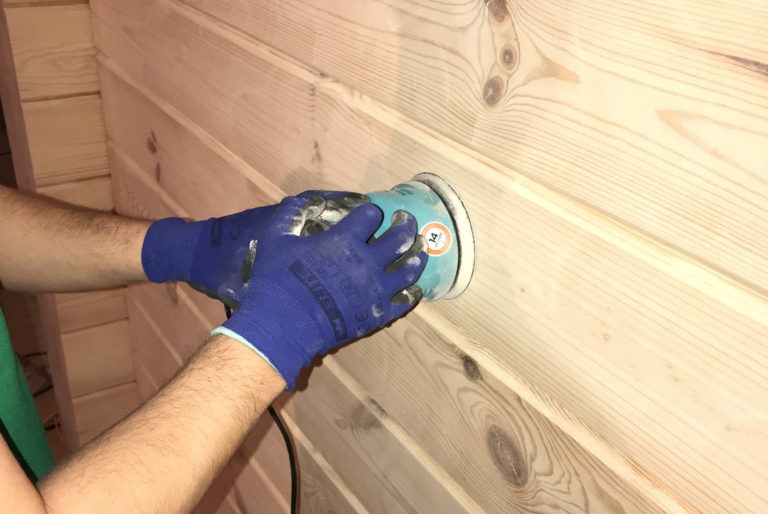
Предварительно необходимо зачистить, выровнять обрабатываемую поверхность, удалить остатки стружки, древесной пудры.
Обработка древесины
Рекомендуется предварительная пропитка сухих лесоматериалов грунтовкой, рабочий состав разбавляют вдвое. Если влажность каркасов или заготовок не менее 22%, сразу проводится обработка дерева жидким стеклом. Для расчета нужного количества раствора принимается усредненный расход –300 г/м2. Жидкое стекло разбавляют только перед проведением работ, тщательно перемешивают.
Обработку проводят в любое время года, при температуре воздуха не ниже -20°C, не выше +40°С. Смесь наносят флейцевой кистью или войлочным валиком по направлению волокон. Мелкие детали проще обработать обмакиванием.
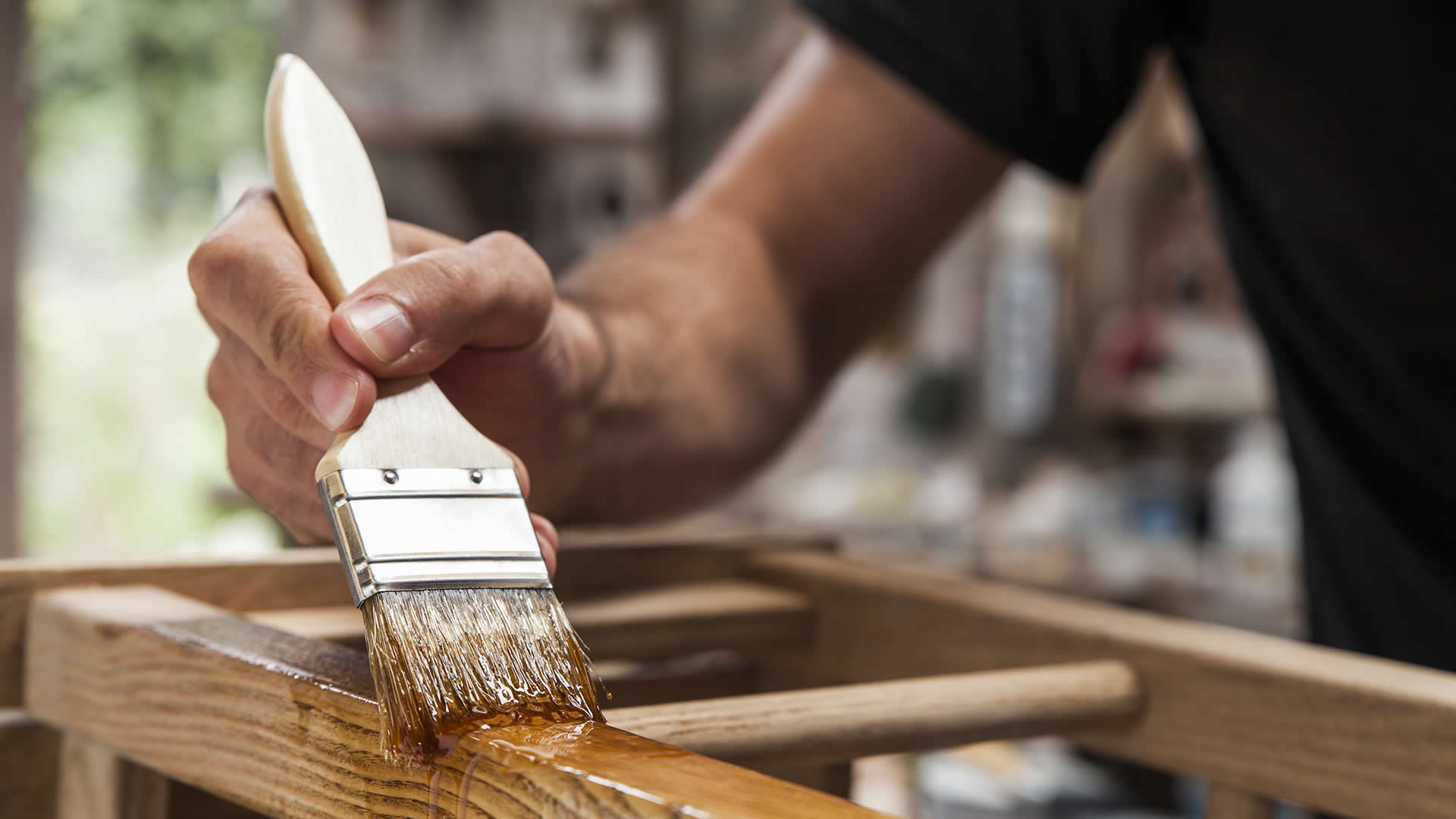
Обработку проводят в любое время года, при температуре воздуха не ниже -20°C, не выше +40°С.
Уход за поверхностью
Жидким стеклом нередко обрабатывают деревянные щиты при изготовлении обеденных столов. При нанесении ЖС на столешницы хорошо просматривается волоконная текстура. На стол можно выкладывать продукты питания, пленка химически нейтральная, не разрушается от контакта с пищевыми кислотами и щелочами, не портится от моющих средств, дезинфицирующих растворов.
Единственный минус силикатов – обработанную поверхность невозможно покрасить. Объясняется это тем, что поверхность становится зеркально гладкой. Сцепление с обычными ЛКМ плохое, приходится применять специальные силикатные краски и лаки. После обработки дерево незначительно темнеет, если использовать составы с присадками, можно добиться хорошей декоративности.
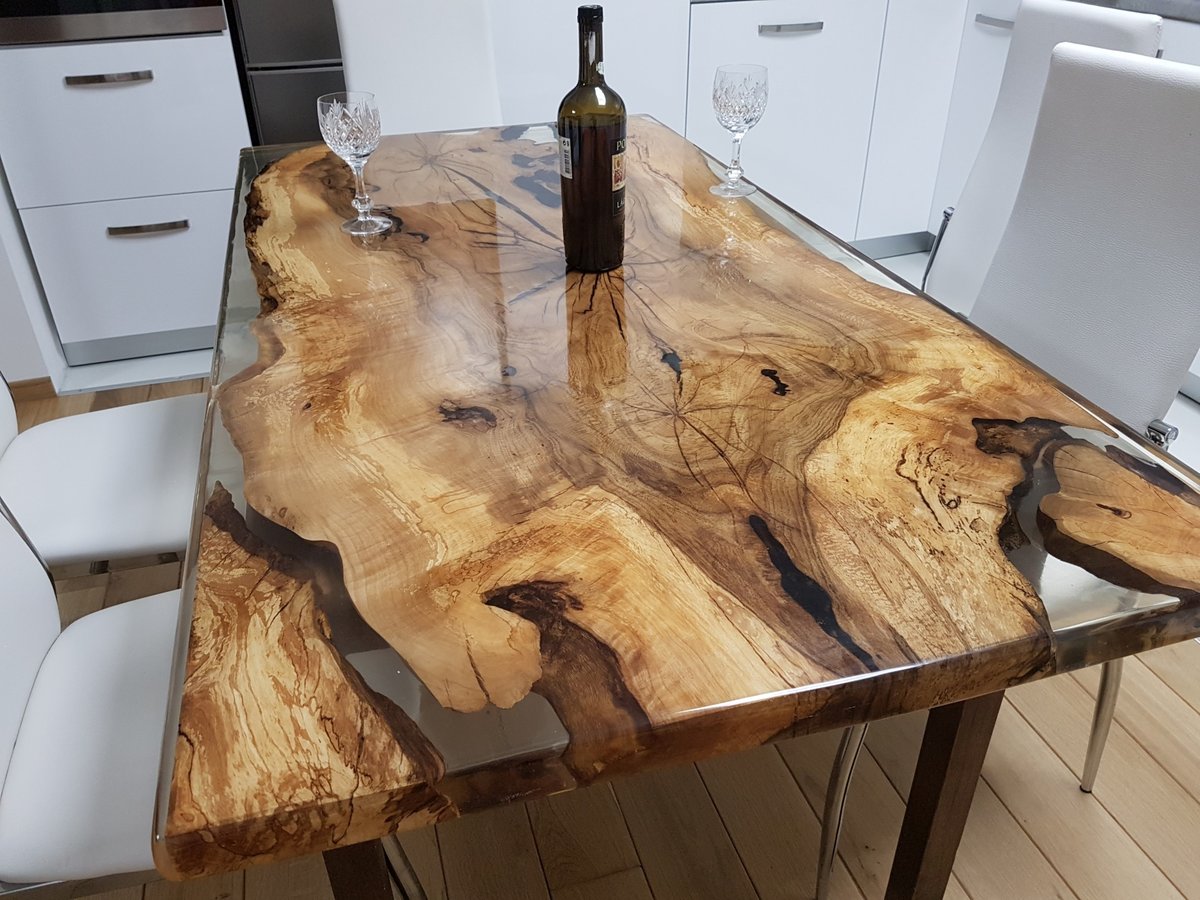
При нанесении ЖС на столешницы хорошо просматривается волоконная текстура.
При низкой стоимости жидкое стекло обладает высокими потребительскими свойствами, обеспечивает защиту древесины от атмосферных воздействий, микроорганизмов, насекомых, огня. Продукция различных производителей обладает схожими свойствами, но может отличаться составом присадок. При выборе жидкого стекла лучше приобретать продукцию брендовых производителей.
Видео: Стол из эпоксидной смолы
Стеклянная тара для фармацевтического применения: состав, типы, оценка
Стеклянная тара — один из основных упаковочных материалов, нашедших применение в фармацевтической промышленности. Большое количество фармацевтических составов было упаковано с использованием стеклянных контейнеров, стеклянных контейнеров, и они обычно являются первым выбором упаковочных материалов. Стекло — это неорганический материал (в основном силикаты) или смесь материалов, которые при нагревании и последующем охлаждении затвердевают без кристаллизации.
Состав стекла
Стекло в основном состоит из диоксида кремния (59-80%) с различной степенью оксида кальция (5-12%), оксида натрия (12-17%), оксида алюминия (0,5-3,0%), бария оксид, оксид бора, оксид калия и оксид магния. Высокая температура плавления стекла обусловлена наличием кремнезема. Температура плавления и вязкость расплава стекла изменяются добавлением оксидов.
Классификация стекла
Стеклянная тара подразделяется на стекло типа I, стекло типа II, стекло типа III и стекло типа IV в зависимости от степени их химической / гидролитической устойчивости к воздействию воды.Степень атаки зависит от степени выделения щелочи под воздействием агрессивной среды.
и. Стеклянные контейнеры типа I (боросиликатное стекло / нейтральное стекло)
Это тип стеклянных контейнеров, которые содержат 80% кремнезема, 10% оксида бора, небольшое количество оксида натрия и оксида алюминия. Он химически инертен и обладает высокой гидролитической стойкостью из-за присутствия оксида бора. Он имеет самый низкий коэффициент расширения и, следовательно, обладает высокими характеристиками термического удара.
Использование стеклянных контейнеров типа I
- Стекло типа I подходит в качестве упаковочного материала для большинства препаратов, как парентеральных, так и непарентеральных.
- Их также можно использовать для содержания сильных кислот и щелочей.
Читайте также: Пластиковые контейнеры для фармацевтического применения
ii. Стеклянная тара типа II (натриево-кальциево-силикатное стекло / обработанное натриево-известковое стекло / дещелоченное натриево-известковое стекло)
Это модифицированный тип стеклянной тары типа III с высокой гидролитической стойкостью, возникающей в результате соответствующей обработки внутренней поверхности стекло типа III с серой.Это делается для удаления вымываемых оксидов и, таким образом, предотвращения цветения / выветривания бутылок. Стекло типа II имеет более низкую температуру плавления по сравнению со стеклом типа I и поэтому его легче формовать.
Использование стеклянных контейнеров типа II
- Они подходят для большинства кислых и нейтральных водных препаратов, как парентеральных, так и непарентеральных.
iii. Стеклянная тара типа III (обычное натриево-известковое стекло)
Это необработанное натриево-известковое стекло со средней химической стойкостью.Он содержит 75% диоксида кремния, 15% оксида натрия, 10% оксида кальция, небольшое количество оксида алюминия, оксида магния и оксида калия. Оксид алюминия влияет на химическую стойкость, а оксид магния снижает температуру, необходимую во время формования.
Использование стеклянных контейнеров типа III
- Они используются в качестве упаковочного материала для парентеральных продуктов или порошков для парентерального применения ТОЛЬКО там, где имеются подходящие данные испытаний на стабильность, указывающие, что стекло типа III является удовлетворительным .
- Они используются для упаковки неводных препаратов и порошков для парентерального применения, за исключением лиофилизированных препаратов.
- Они также используются для упаковки непарентеральных препаратов.
Стеклянная тара типа IV (стекло типа NP / известково-натриевое стекло общего назначения)
Стеклянная тара этого типа имеет низкую гидролитическую стойкость. Этот тип стеклянной тары не используется для продуктов, которые необходимо автоклавировать, поскольку это увеличивает скорость реакции эрозии стеклянной тары.
Использование стеклянной тары типа IV
- Используется для хранения продуктов местного действия и пероральных лекарственных форм
Процесс формования стеклянной тары
Стеклянная тара формируется следующими способами
- Выдувание — это включает в себя: использование сжатого воздуха для формирования расплавленного стекла в полости формы.
- Чертеж — это включает вытягивание расплавленного стекла через матрицы, которые формируют из мягкого стекла ампулы, пузырьки и т. Д.
- Прессование — Стекло формируется за счет использования механической силы, которая прижимает или заставляет расплавленное стекло двигаться по форме.
- Отливка — сила тяжести или центробежная сила используется для инициирования образования расплавленного стекла в полости.
Как производится стеклянная тара
a. Как производятся стеклянные бутылки
б. Как изготавливаются стеклянные флаконы
c. Как изготавливаются ампулы
Оценочные исследования стеклянных емкостей
- Испытание на гидролитическую стойкость
i.Тест на зернистость стекла — используется для отличия стекла типа I от стекла типа II и стекла типа III
ii. Тестирование поверхности стекла — используется для отличия стеклянных контейнеров типа I и типа II от стеклянного контейнера типа III. Он основан на гидролитической стойкости внутренних поверхностей стеклянной тары.
iii. Испытание на травление поверхности / Сравнение результатов испытания стеклянных зерен и данных испытания поверхностного стекла — предназначено для определения того, является ли высокая гидролитическая стойкость стеклянных емкостей типа I или типа II результатом обработки внутренней поверхности или химического состава стеклянных емкостей
- Свет / спектральное пропускание для цветных стеклянных контейнеров
- Выделение мышьяка — используется для обнаружения присутствия мышьяка в водных парентеральных препаратах
Факторы, влияющие на выбор стеклянного контейнера
Существуют различные факторы, влияющие на процесс выбора стеклянных контейнеров как первичные пакеты.Эти факторы включают:
- Предел щелочности и гидролитической стойкости стеклянной емкости
- Свойства теплового расширения стеклянной емкости (сублимационная сушка)
- Чувствительность стеклянной емкости к ионам бария или кальция
Преимущества стеклянной емкости
- Стеклянная тара в основном используется для упаковки жидких препаратов из-за ее жесткости и превосходных защитных свойств.
- Высокая прозрачность позволяет легко проверять ее содержимое.
- Он обеспечивает лучшую защиту, поскольку относительно непроницаем для воздуха и влаги.
- Обладает химической стойкостью к большинству лекарственных средств.
- Цветное стекло (янтарное стекло и стекло красного цвета) может защитить его содержимое от ультрафиолетовых лучей и определенных длин волн.
- Стеклянная тара легко стерилизуется с помощью тепла.
Недостатки стеклянных контейнеров
- Стеклянные контейнеры дороги в производстве
- Они хрупкие и относительно тяжелые
- Во время тепловой стерилизации некоторые типы стеклянных контейнеров имеют тенденцию выделять часть кремнезема в состав.
Ссылка
- НАСА П. (2014). Обзор фармацевтического упаковочного материала. Всемирный журнал фармацевтических исследований , 3 (5): 344-368.
- Пиллаи С. А., Чобиса Д., Урими Д. и Равиндра Н. (2016). Взаимодействие с фармацевтическим стеклом: обзор возможностей. Журнал фармацевтических наук и исследований, 8 (2), 103-111.
- Shivsharan U. S., Raut E.S. и Шейх З. М. (2014). Упаковка косметики: обзор. Журнал фармацевтических и научных инноваций, 3 (4), 286-293.
Связанные ключевые слова: типы стеклянной тары, используемой в фармацевтических препаратах pdf, оценка стеклянной тары Slideshare, стекло как упаковочный материал ppt, оценка стеклянной тары ppt, пример стекла типа 2, типы стеклянной тары, используемые в фармацевтике ppt, недостатки стекла контейнеры для парентерального приготовления, использование стекла типа 2, различные типы стеклянных контейнеров, используемых в фармацевтических препаратах, использование стеклянных контейнеров типа 2, стекло в фармацевтической упаковке, спецификация стекла USP типа 3, стеклянные контейнеры типа 2, подходящие для стеклянных контейнеров типа 2, используемые для , стекло типа 1 использует
.Типы буровых растворов — PetroWiki
Существует несколько различных типов буровых растворов в зависимости от их состава и использования. Три ключевых фактора, которые определяют выбор типа бурового раствора для конкретной скважины:
- Стоимость
- Технические характеристики
- Воздействие на окружающую среду.
Выбор правильного типа жидкости для конкретных условий является важной частью успешных буровых работ.
Классификация буровых растворов
В ежегодной классификации жидкостных систем World Oil [1] перечислены девять различных категорий буровых растворов, в том числе:
- Пресноводные системы
- Системы морской воды
- Системы на масляной или синтетической основе
- Пневматические (воздух, туман, пена, газ) «жидкостные» системы
Тип жидкости, выбранной для конкретной скважины, обычно определяется тремя ключевыми факторами:
- Стоимость
- Технические характеристики
- Воздействие на окружающую среду
Жидкости на водной основе (WBF) являются наиболее широко используемыми системами и считаются менее дорогими, чем жидкости на масляной основе (OBF) или жидкости на синтетической основе (SBF).OBF и SBF, также известные как инвертно-эмульсионные системы, содержат масляную или синтетическую базовую жидкость в качестве непрерывной (или внешней) фазы и рассол в качестве внутренней фазы. Системы с обращенной эмульсией имеют более высокую стоимость за единицу, чем большинство жидкостей на водной основе, поэтому их часто выбирают, когда условия в скважине требуют надежного ингибирования образования сланца и / или отличной смазывающей способности. Системы на водной основе и обратно-эмульсионные системы могут быть разработаны так, чтобы выдерживать относительно высокие температуры в скважине. Пневматические системы чаще всего применяются в областях, где пластовое давление относительно низкое и риск потери циркуляции или повреждения пласта относительно высок.Для использования этих систем требуется специальное оборудование для регулирования давления, которое помогает предотвратить развитие опасных условий при обнаружении углеводородов.
Жидкости на водной основе
Жидкости на водной основе (WBF) используются для бурения примерно 80% всех скважин. [2] Базовая жидкость может быть пресной водой, морской водой, рассолом, насыщенным рассолом или рассолом формиата. Тип выбранной жидкости зависит от ожидаемых условий в скважине или от конкретного интервала пробуриваемой скважины.Например, поверхностный интервал обычно пробуривается с использованием бурового раствора низкой плотности на водной или морской основе, который содержит небольшое количество промышленных добавок. Эти системы включают в себя природные глины в процессе бурения. Некоторое количество коммерческого бентонита или аттапульгита также может быть добавлено для помощи в контроле потери жидкости и повышения эффективности очистки скважины. После того, как обсадная колонна установлена и зацементирована, оператор часто продолжает бурение с WBF, если только условия скважины не требуют замены системы на нефтяную или синтетическую.
WBF делятся на две большие категории: недисперсные и диспергированные.
Недисперсные системы
Простые гель-водные системы, используемые для бурения верхних скважин, недисперсны, как и многие современные полимерные системы, которые содержат мало или совсем не содержат бентонита. Природные глины, входящие в состав недисперсных систем, регулируются путем разбавления, инкапсулирования и / или флокуляции. Правильно спроектированная система контроля твердых частиц может использоваться для удаления мелких твердых частиц из системы бурового раствора и помогает поддерживать эффективность бурения.Недисперсные полимерные системы с низким содержанием твердых частиц (LSND) основаны на длинноцепочечных полимерах с высоким и низким молекулярным весом для обеспечения контроля вязкости и водоотдачи. Твердые вещества с низким содержанием коллоидов инкапсулируются и флокулируются для более эффективного удаления с поверхности, что, в свою очередь, снижает требования к разбавлению. Доступны специально разработанные высокотемпературные полимеры, помогающие преодолеть проблемы гелеобразования, которые могут возникнуть в скважинах с высоким давлением и высокой температурой (HP / HT). [3] При правильной обработке некоторые системы LSND могут быть взвешены до 17.От 0 до 18,0 ppg при температуре 350 ° F и выше.
Дисперсные системы
Дисперсные системы обрабатываются химическими диспергаторами, которые предназначены для дефлокуляции глинистых частиц, чтобы обеспечить улучшенный контроль реологии в буровых растворах с более высокой плотностью. Широко используемые диспергаторы включают лигносульфонаты, лигнитные добавки и дубильные вещества. Дисперсные системы обычно требуют добавления каустической соды (NaOH) для поддержания уровня pH от 10,0 до 11,0. Диспергирование системы может увеличить ее толерантность к твердым частицам, делая возможным взвешивание до 20 единиц.0 стр. Обычно используемая лигносульфонатная система основана на относительно недорогих добавках и знакома большинству операторов и персонала буровой установки. Дополнительные обычно используемые дисперсные буровые растворы включают известь и другие катионные системы. Дисперсная система с твердыми частицами также может значительно снизить скорость проникновения и способствовать эрозии отверстия.
Буровые растворы на морской воде
Буровые растворы на морской воде часто используются для подавления образования сланцев и для бурения соляных пластов. Также известно, что они препятствуют образованию ледоподобных гидратов, которые могут накапливаться вокруг подводных устьев скважин и оборудования для контроля скважин, блокируя линии и затрудняя критические операции.Системы без твердых частиц и с низким содержанием твердых частиц могут быть составлены с использованием рассолов высокой плотности, таких как:
- Хлорид кальция
- Бромид кальция
- Бромид цинка
- Формиат калия и цезия
Полимерные буровые растворы
Полимерные буровые растворы используются для бурения реактивных пластов, где требование по ингибированию сланца является значительным. Часто используемые ингибиторы сланца — это соли, гликоли и амины, все из которых несовместимы с использованием бентонита.Эти системы обычно получают свой профиль вязкости из полимеров, таких как ксантановая камедь, и контроля потери жидкости из крахмала или производных целлюлозы. Хлорид калия — недорогой и высокоэффективный ингибитор сланца, который широко используется в качестве основного рассола для полимерных буровых растворов во многих частях мира. Ингибиторы на основе гликоля и амина могут быть добавлены для дальнейшего усиления ингибирующих свойств этих жидкостей.
Буровые растворы
Бурение продуктивной зоны с использованием обычного флюида может привести к множеству ранее неопределенных рисков, все из которых уменьшают связь коллектора со стволом скважины или уменьшают проницаемость пласта.Это особенно верно для горизонтальных скважин, где продуктивная зона может подвергаться воздействию бурового раствора в течение длительного интервала. Выбор наиболее подходящей жидкостной системы для бурения продуктивной зоны требует глубокого понимания коллектора. Используя данные, полученные в результате лабораторных испытаний керновых пробок из тщательно отобранных кернов продуктивной зоны, необходимо провести исследование чувствительности пластового флюида для определения морфологического и минералогического состава породы-коллектора. Необходимо проанализировать природные пластовые флюиды, чтобы установить их химический состав.Степень ущерба, который может быть причинен ожидаемыми проблемами, можно смоделировать, как и эффективность возможных решений для снижения рисков.
Жидкость для бурения скважин (DIF) — это чистая жидкость, которая предназначена для того, чтобы вызвать небольшую потерю естественной проницаемости продуктивной зоны или не вызвать ее вообще, а также обеспечить превосходную очистку ствола и легкую очистку. DIF могут быть:
- На водной основе
- на рассоле
- На масляной основе
- На синтетической основе
Помимо того, что он безопасен и экономичен для применения, DIF должен быть совместим с природными флюидами коллектора, чтобы избежать осаждения солей или образования эмульсий.Подходящая неповреждающая жидкость должна образовывать фильтрационную корку на поверхности пласта, но не должна проникать слишком глубоко в структуру пор пласта. Фильтрат жидкости должен препятствовать или предотвращать набухание реактивных частиц глины в поровых каналах.
Повреждение формации обычно вызывается:
- Проникновение в продуктивную зону и закупорка мелкими частицами
- Вздутие пластовой глины
- Смешивание несовместимых жидкостей
- Движение частиц смещенного пласта, заполняющего поры
- Изменение смачиваемости коллекторов и пород
- Образование эмульсий или водоблоков
После того, как механизм повреждения уменьшил проницаемость резервуара, редко удается восстановить резервуар до его исходного состояния.
Жидкости на масляной основе
Системы на масляной основе были разработаны и внедрены в 1960-х годах для решения нескольких проблем бурения:
- Пластовые глины, которые реагируют, набухают или отслаиваются после воздействия WBF
- Повышение забойных температур
- Загрязняющие вещества
- Застрявшая труба, крутящий момент и сопротивление
Используемые сегодня жидкости на масляной основе (OBF) состоят из дизельного топлива, минерального масла или малотоксичных линейных олефинов и парафинов.Олефины и парафины часто называют «синтетическими», хотя некоторые из них получают при перегонке сырой нефти, а некоторые синтезируются химическим путем из более мелких молекул. Электрическая стабильность внутреннего рассола или водной фазы контролируется, чтобы помочь гарантировать, что прочность эмульсии поддерживается на заданном или близком к нему значении. Эмульсия должна быть достаточно стабильной, чтобы включать дополнительный объем воды, если встретится поток воды в скважине.
Барит используется для увеличения плотности системы, а специально обработанный органофильный бентонит является основным загустителем в большинстве систем на масляной основе.Эмульгированная водная фаза также влияет на вязкость жидкости. Добавляются органофильные лигнитные, асфальтовые и полимерные материалы, чтобы помочь контролировать потери жидкости HP / HT (высокое давление / высокая температура). Смачивание маслом необходимо для того, чтобы твердые частицы оставались во взвешенном состоянии. Поверхностно-активные вещества, используемые для смачивания маслом, также могут работать как разбавители. Системы на масляной основе обычно содержат известь для поддержания повышенного pH, противостояния вредному воздействию сероводорода (H 2 S) и углекислого газа (CO 2 ) и повышения стабильности эмульсии.
Ингибирование сланца — одно из ключевых преимуществ использования масляной системы. Водная фаза с высокой соленостью помогает предотвратить гидратация, набухание и оседание сланцев в стволе скважины. Большинство традиционных систем бурового раствора на нефтяной основе (РУО) состоит из рассола хлорида кальция, который, по-видимому, обладает лучшими ингибирующими свойствами для большинства сланцев.
Отношение процентного содержания нефти к процентному содержанию воды в жидкой фазе системы на масляной основе называется ее отношением масло / вода.Системы на масляной основе обычно хорошо работают при соотношении масло / вода в диапазоне от 65/35 до 95/5, но наиболее часто наблюдаемый диапазон составляет от 70/30 до 90/10.
Сброс целой жидкости или шлама, образовавшегося с помощью OBF, не разрешен в большинстве морских районов бурения. Весь такой буровой шлам и отработанные жидкости перерабатываются и отправляются на берег для утилизации. В то время как многие наземные скважины по-прежнему бурятся с использованием жидкостей на основе дизельного топлива, разработка жидкостей на синтетической основе (SBF) в конце 1980-х предоставила новые возможности для морских операторов, которые зависят от характеристик бурения нефтяных систем, чтобы помочь удерживать их в целом. затраты на бурение, но требуются более экологически чистые жидкости.В некоторых регионах мира, таких как Северное море, даже эти жидкости запрещены к сбросу в море.
Буровые растворы на синтетической основе
Жидкости на синтетической основе были разработаны из-за растущего желания уменьшить воздействие на окружающую среду при проведении морских буровых работ, но без ущерба для рентабельности систем на нефтяной основе.
Как и традиционные OBF, SBF могут использоваться для:
- Максимальное увеличение скорости проникновения (ROP)
- Повышение смазываемости в наклонно-направленных и горизонтальных скважинах
- Сведение к минимуму проблем со стабильностью ствола скважины, например, вызванных химически активными сланцами.
Полевые данные, собранные с начала 1990-х годов, подтверждают, что SBF обеспечивают исключительные характеристики бурения, легко сравнимые с жидкостями на основе дизельного топлива и минеральных масел.
Во многих шельфовых зонах правила, запрещающие сброс шлама, пробуренного с помощью OBF, не применяются к некоторым системам на синтетической основе. Стоимость SBF на баррель может быть выше, но они оказались экономичными во многих морских применениях по тем же причинам, что и традиционные OBF: высокая скорость проникновения и меньшее непроизводительное время (NPT), связанное с буровым раствором. SBF, в состав которых входят линейные альфаолефины (LAO) и изомеризованные олефины (IO), демонстрируют более низкую кинематическую вязкость, которая требуется в ответ на растущую важность проблем вязкости по мере того, как операторы переходят в более глубокие воды.Ранние системы на основе эфиров демонстрировали высокую кинематическую вязкость, состояние, которое усиливается при низких температурах, встречающихся в глубоководных стояках. Однако сложный эфир с более короткой длиной цепи (C 8 ) и низкой вязкостью, который был разработан в 2000 году, демонстрирует вязкость, аналогичную вязкости других базовых жидкостей или ниже, чем у других основных жидкостей, в частности, широко используемых систем IO. Из-за их высокой биоразлагаемости и низкой токсичности сложные эфиры повсеместно признаны лучшей базовой жидкостью для защиты окружающей среды.
К концу 2001 года глубоководные скважины обеспечивали 59%; нефти, добываемой в Мексиканском заливе. [4] До тех пор, пока операторы не начали бурение в этих глубоководных местах, где предел порового давления / градиента трещин (PP / FG) очень узкий, а стояки длиной в милю не редкость, стандартные синтетические составы обеспечивали удовлетворительные характеристики. Однако проблемы, возникшие из-за глубоководного бурения и изменения экологических норм, побудили более пристально изучить несколько, казалось бы, важных добавок.
При низких температурах обычные SBF могут иметь нежелательно высокую вязкость в результате присутствия в системе органофильной глины и лигнитных добавок. Введение SBF, составленных с нулевым или минимальным добавлением органофильной глины и лигнитных продуктов, позволило контролировать реологические свойства и свойства водоотдачи с помощью характеристик жидкой эмульсии. К преимуществам производительности этих систем относятся:
- Высокая прочность плоского геля, который разрушается при минимальном давлении инициирования
- Значительно более низкие эквивалентные плотности циркуляции (ECD)
- Снижение потерь бурового раствора при бурении, спуске обсадной колонны и цементировании
Полностью нефтяные жидкости
Обычно водная фаза с высоким содержанием соли в инвертно-эмульсионной жидкости помогает стабилизировать реактивный сланец и предотвратить набухание.Однако буровые растворы, в состав которых входит нефть на дизельной или синтетической основе и не содержащая водной фазы, используются для бурения длинных сланцевых интервалов, в которых соленость пластовой воды сильно варьируется. За счет исключения водной фазы буровой раствор, полностью состоящий из нефти, может сохранять стабильность сланца на протяжении всего интервала.
Буровые растворы пневматические
Сжатый воздух или газ можно использовать вместо бурового раствора для циркуляции выбуренной породы из ствола скважины. Пневматические жидкости делятся на три категории:
- Только воздух или газ
- Газированная жидкость
- Пена [5]
Пневматические буровые работы требуют специального оборудования для обеспечения безопасного управления шламом и пластовыми флюидами, которые возвращаются на поверхность, а также резервуаров, компрессоров, трубопроводов и клапанов, связанных с газом, используемым бурение или аэрация бурового раствора или пены.
За исключением случаев бурения пластов с высоким давлением, содержащих углеводороды или флюиды, для которых требуется флюид высокой плотности для предотвращения проблем с контролем скважины, использование пневматических флюидов дает несколько преимуществ [6] :
- Незначительное повреждение пласта или его отсутствие
- Экспресс-оценка шлама на наличие углеводородов
- Предупреждение потери обращения
- Значительно более высокая скорость проходки в горных породах
Специальные продукты
Компании по обслуживанию буровых растворов предоставляют широкий спектр добавок, предназначенных для предотвращения или уменьшения дорогостоящих задержек при строительстве скважин.Примеры этих продуктов включают:
- Материалы для потери циркуляции (LCM), которые помогают предотвратить или остановить потерю скважинного бурового раствора в слабые или истощенные пласты.
- Жидкости для обнаружения прихвата трубы.
- Смазочные материалы для WBF, снижающие крутящий момент и сопротивление и облегчающие бурение в условиях больших углов.
- Защитные химические вещества (например, ингибиторы накипи и коррозии, биоциды и поглотители H 2 S), предотвращающие повреждение труб и персонала.
МТР
Существует множество типов LCM для устранения ситуаций потери:
- Карбонат кальция крупный
- Слюда
- Волокнистый материал
- Целлофан
- Измельченная скорлупа грецкого ореха
Разработка деформируемых графитовых материалов, которые могут непрерывно закрывать трещины в условиях изменяющегося давления, позволила операторам более последовательно устранять некоторые виды потерь. Применение этих и подобных материалов для предотвращения или замедления физической дестабилизации ствола скважины оказалось успешным.Гидратируемые и быстро схватывающиеся пилюли против потери циркуляции также эффективны для лечения серьезных и полных потерь. Некоторые из этих быстродействующих таблеток можно смешивать и перекачивать с помощью стандартного бурового оборудования, в то время как для других требуется специальное оборудование для перемешивания и перекачивания.
Жидкости для капель
Большинство разведочных жидкостей предназначены для проникновения и разрушения корки стенок вокруг бурильной колонны. Для достижения результатов обычно требуется период замачивания. Жидкости для обнаружения капель обычно состоят из базовой жидкости и добавок, которые могут быть включены в активную систему бурового раствора без каких-либо побочных эффектов после освобождения трубы и / или возобновления циркуляции.
Смазочные материалы
Смазочные материалы могут содержать материалы на углеводородной основе или могут быть составлены специально для использования в областях, где экологические нормы запрещают использование присадок на масляной основе. Крошечные стеклянные или полимерные шарики также могут быть добавлены в буровой раствор для повышения смазывающей способности. Смазочные материалы предназначены для уменьшения трения при контакте металла с металлом и для обеспечения смазывающей способности бурильной колонны в открытом стволе, особенно в наклонно-направленных скважинах, где бурильная колонна, вероятно, будет постоянно контактировать со стволом скважины.
Коррозия, ингибиторы, биоциды и поглотители
Коррозия вызывает большинство потерь в бурильных трубах и повреждает обсадные трубы, буровые насосы, долота и скважинные инструменты. По мере увеличения скважинных температур коррозия также увеличивается с соответствующей скоростью, если бурильная колонна не защищена химической обработкой. Абразивные материалы в буровом растворе могут ускорить коррозию, стирая защитные пленки. Коррозия, как правило, вызывается одним или несколькими факторами, включая:
- Воздействие кислорода, H 2 S и / или CO 2
- Бактериальная активность в буровом растворе
- Высокотемпературная среда
- Контакт с серосодержащими материалами
Купоны бурильной колонны можно вставлять между соединениями бурильных труб при спуске трубы в скважину.Когда в следующий раз труба будет выведена из ствола скважины, купон можно проверить на наличие признаков точечной коррозии и коррозии, чтобы определить, подвергаются ли компоненты бурильной колонны аналогичному повреждению.
H 2 S и CO 2 часто присутствуют в одном и том же пласте. Обработка поглотителем и ингибитором должна быть разработана таким образом, чтобы противодействовать обоим газам, если приток происходит из-за условий бурения на депрессии. Поддержание высокого pH помогает контролировать H 2 S и CO 2 , а также предотвращает скисание бурового раствора бактериями.Бактерии также можно контролировать с помощью микробиоцидной добавки.
Ссылки
- ↑ World Oil 2004 Буровые жидкости, жидкости для заканчивания и ремонта скважин. 2004. World Oil 225 (6): F-1.
- ↑ Отчет о нефтяном рынке за 2004 год. Spears & Assoc. Inc., Талса, Оклахома, www.spearsresearch.com.
- ↑ Мейсон У. и Глисон Д. 2003. Система, разработанная для глубоких горячих скважин. Американский репортер нефти и газа 46 (8): 70.
- ↑ Сводка по глубоководной добыче по годам, регион Мексиканского залива, морская информация.Служба управления минералами, Министерство внутренних дел США, www.gomr.mms.gov/homepg/offshore/deepwatr/summary.asp.
- Перейти ↑ Lyons, W.C., Guo, B., and Seidel, F. 2001. Air and Gas Drilling Manual. Нью-Йорк: Макгроу-Хилл.
- ↑ Negrao, A.F., Lage, A.C.V.M., и Cunha, J.C. 1999. Обзор бурения воздухом / газом / пеной в Бразилии. SPE Drill и Compl 14 (2): 109-114. SPE-56865-PA. http://dx.doi.org/10.2118/56865-PA
Интересные статьи в OnePetro
А. Р.Исмаил, А. Камис, San Boon Engineering; К. С. Фу, Технологический университет Малайзии: Характеристики систем бурового раствора на основе сложного минерального эфира и нефти, 2001-044, http://dx.doi.org/10.2118/2001-044
Мохаммад Ф. Закария, SPE, Маен Хусейн, SPE: новый буровой раствор на основе наночастиц с улучшенными характеристиками, 156992-MS, http://dx.doi.org/10.2118/156992-MS
Внешние ссылки
См. Также
Буровые растворы
PEH: Буровые растворы
.Руководство по охлаждающим жидкостям и присадкам к двигателям
Теперь, когда температура повышается и мой двигатель, кажется, становится все горячее, я читаю в Интернете много всякой всячины о различных охлаждающих жидкостях. Я также видел заявления о присадках, которые можно просто влить, и двигатель будет охлаждаться. Что-нибудь из этого работает?
Д.П.
Джефф Смит: За эти годы я потратил больше времени, чем следовало бы, на исследование и тестирование охлаждающих жидкостей двигателя , присадок и их рабочих характеристик.И, как вы обнаружили, существует множество дезинформации и возмутительных заявлений о производительности. Но если мы применим немного науки и немного покопаемся, вы можете обнаружить, что традиционный, упрощенный подход часто оказывается лучшим — оставляя «чудодейственные» жидкости преследователям сновидений.
Начнем с неопровержимого факта. Обычная пресная вода — удивительная жидкость. Он обладает способностью поглощать больше тепла на единицу измерения, чем любой другой хладагент, и совпадает с этой способностью передавать это тепло радиатору более эффективно, чем любой другой хладагент.Так что сразу может показаться, что лучшая охлаждающая жидкость, которую вы можете использовать, — это чистая вода.
Но, очевидно, нам понадобится добавка для борьбы с коррозией, а также что-то для защиты от замерзания в холодное время года. Здесь, в Южной Калифорнии, если в разгар зимы температура опускается ниже 50 градусов по Фаренгейту, это становится заголовком новостей. Тем, кто живет в более мягком климате, можно обойтись чистой водой только с антикоррозийной добавкой. Существует масса этих добавок, и многие из них отлично справляются со своей задачей.
Наш опыт работы с различными антикоррозийными продуктами за последние 20 лет привел нас к компании под названием Applied Chemical Specialties (APS). Они предлагают пару продуктов, которые будут работать. Недавно компания представила высокоэффективную присадку под названием Hyper-Kuhl, которая выполняет антикоррозийную работу, но также повышает эффективность системы охлаждения. В течение многих лет мы использовали их добавку No-Rosion, и она отлично себя зарекомендовала. Он рассчитан на использование около года, а затем его следует укрепить.Другие аналогичные продукты, которые я также использовал в этой же категории, — это Royal Purple’s Purple Ice и Driven’s Coolant System Protector (CSP).
На протяжении многих лет мы обсуждали проблему уменьшения коррозии с владельцем APS Джеем Россом, и я довольно много узнал о том, что происходит в системе охлаждения. Главный шаг, который вы можете предпринять для улучшения производительности системы охлаждения, — это начать с правильной воды. Как вы понимаете, не вся вода одинакова. Мы проверили водопроводную воду в нашей местной Южной Калифорнии и были потрясены уровнем примесей.Мы не будем вдаваться в подробности, но в воде был шокирующе высокий уровень так называемых общих растворенных твердых веществ, а также металлов, таких как железо, что только усложняло работу антикоррозийной присадки. Ясно, что использование воды, которая удаляет все эти загрязнения, было бы хорошо. Но будь осторожен.
Вы, наверное, слышали, как и мы, что лучше всего использовать дистиллированную воду. Но Росс предупреждает, что дистиллированная вода не так идеальна, как кажется. Да, процесс дистилляции удаляет почти 100 процентов примесей, но процесс удаления этих материалов также приводит к химическому дисбалансу воды.
Хотя мы мало что узнали в химии в старших классах, мы сохранили один факт: любой химический раствор будет пытаться уравновесить себя. Таким образом, когда дистиллированная вода заливается в систему охлаждения, она немедленно запускает процесс отрыва электронов от мягких металлов в системе. К ним относятся цинк, магний и алюминий. Таким образом, вы можете видеть, что использование дистиллированной воды, смешанной с любыми антикоррозийными присадками, сразу же создает гораздо большую нагрузку на антикоррозионные присадки.
Есть несколько различных версий очищенной воды, которые являются гораздо лучшими альтернативами. Так называемая мягкая вода — это процесс, при котором хлорид натрия (NaCl) смешивается с водой для удаления тех же примесей. Этот процесс использует ион натрия для создания сбалансированного раствора. Поскольку вода химически сбалансирована, она не отрывает электроны от мягких металлов в системе охлаждения, а это именно то, что нам нужно. Хотя некоторые энтузиасты возражают против этого, поскольку утверждают, что он добавляет соли в воду, если вы когда-нибудь пробовали мягкую воду, вы знаете, что это не так.Мягкая вода — отличный выбор.
Если получить мягкую воду сложно, ищите питьевую воду, очищенную методом обратного осмоса. Мы нашли компанию под названием Glacier Water , которая размещает диспенсеры для воды возле продуктовых магазинов и продает эту воду по тридцать центов за галлон. Мы протестировали эту воду и обнаружили, что она удаляет практически все растворенные металлические примеси. Это то, что мы используем исключительно во всех наших системах охлаждения. Если не считать этого, любая бытовая система очистки водопроводной воды, безусловно, лучше, чем обычная водопроводная вода.
В условиях гонок на многих кольцевых трассах и драг-полосах запрещено использование этиленгликоля и других охлаждающих жидкостей с антифризом для использования на трассе, поскольку эти охлаждающие жидкости очень затрудняют очистку. Это еще одна ситуация, когда фильтрованная вода с антикоррозийной добавкой, такой как вышеупомянутый Hyper-Kuhl, была бы отличным выбором. Hyper-Kuhl обладает как антикоррозийными свойствами, так и улучшенными характеристиками теплопередачи. Это относится к категории химикатов, называемых поверхностно-активными веществами.
Поверхностно-активное вещество — это химическое вещество, которое снижает поверхностное натяжение воды. Если вы когда-нибудь наполняли стакан с водой до самого края, вы заметите, что вода будет немного выше края стакана. Это связано с очень высоким поверхностным натяжением воды. Высокое поверхностное натяжение воды создает большие пузыри, которые вы видите на дне глубокой кастрюли с водой, когда она кипит. Если вы внимательно понаблюдаете за процессом кипячения, вы заметите, что эти пузырьки остаются на дне кастрюли на мгновение, а затем вырываются и поднимаются на поверхность воды.Эти большие пузыри создаются высоким поверхностным натяжением воды. Теперь представьте, что большие пузырьки, вероятно, возникают также на стороне водяной рубашки камеры сгорания, когда ваш двигатель вырабатывает большую мощность. Когда образуются эти большие пузыри, они снижают характеристики теплопередачи воды и образуют горячие точки. Эти горячие точки могут вызвать детонацию в камере сгорания.
В результате этого выпуска была создана целая линейка продуктов, снижающих поверхностное натяжение воды и улучшающих теплопередачу.Идея заключается в том, что если тепло передается охлаждающей жидкости в головной части, оно также будет более эффективно передаваться охлаждающим трубкам радиатора, что приведет к снижению общей рабочей температуры. Теория есть, но если вы не гонщик по круговой трассе или шоссейный гонщик, не бежите со скоростью 140 с лишним миль в час на гонке Silver State Open Road или гонщик Bonneville, эти добавки могут незначительно повлиять на температуру охлаждающей жидкости. . Но по крайней мере теперь вы знаете, как они работают. Это не просто волшебство.
Среди продуктов, которые работают как поверхностно-активные вещества, можно назвать Water Wetter от Red Line, Hyper-Kuhl Applied, Purple Ice от Royal Purple и Lucas Super Coolant и многие другие.
Если вы ищете антикоррозионную присадку, которая действительно работает с чистой водой, а также потенциально может немного снизить температуру охлаждающей жидкости, то Hyper-Kuhl от Applied Chemical Specialties или Purple Ice от Royal Purple — отличные продукты.
Итак, теперь, когда мы знаем, с какой воды начать, появилось много дезинформации о незамерзании в качестве охлаждающей жидкости. Несомненно, старый резервный этиленгликоль работал десятилетиями. При смешивании в соотношении 50/50 с мягкой или фильтрованной водой это отличный способ добавить антикоррозионные присадки и предотвратить замерзание зимой.Но обычный энтузиазм: «Если что хорошо, тем лучше!» здесь не работает. Любая жидкость, используемая в качестве хладагента, зависит от физического фактора, называемого удельной теплоемкостью. Это определяется как способность жидкости отводить тепло от двигателя — она конкретно определяется как количество БТЕ на фунт жидкости. Неудивительно, что прямая вода является отличной жидкостью для отвода тепла от двигателя.
Но когда мы смешиваем вместе антифриз (этиленгликоль) и воду, способность охлаждающей жидкости отводить тепло от двигателя уменьшается.Мы создали диаграмму (взятую с веб-сайта engineeringtoolbox.com ), которая показывает, что при смеси воды и антифриза 50/50 удельная теплоемкость этой смеси всего на 86 процентов эффективнее, чем у чистой воды.
Я также читал заявления гонщиков, использующих 100-процентный антифриз из-за его температуры кипения 387 градусов F. Проблема с этим подходом заключается в том, что удельная теплоемкость прямого незамерзания составляет 0,66, как показано в прилагаемой таблице. Согласно вышеупомянутому сайту, система охлаждения потеряла 20 процентов своей мощности.Это означает, что вы должны увеличить поток жидкости, по крайней мере, на это, а возможно, и больше. Главное, что нужно запомнить: бесплатного обеда не бывает. И, для справки, точка замерзания прямого антифриза составляет примерно 10 градусов по Фаренгейту — это выше нуля, в то время как смесь 50/50 ближе к -35 градусов по Фаренгейту.
Прошу прощения, что этот ответ длился дольше, чем вы, вероятно, хотели (золотая звезда тем из вас, кто прошел через весь этот кусок!). Это сложная тема, и я постарался сделать ее менее запутанной.Надеюсь это поможет.
Автор: Джефф Смит Джефф Смит страстно увлекался автомобилями с тех пор, как в 10 лет начал работать на заправочной станции своего деда. После окончания Университета штата Айова со степенью журналистики в 1978 году он объединил свои две страсти: автомобили и писательство. Смит начал писать для журнала Car Craft в 1979 году и стал редактором в 1984 году. В 1987 году он взял на себя роль редактора журнала Hot Rod, прежде чем вернуться к своей первой любви к написанию технических рассказов.С 2003 года Джефф занимал различные должности в Car Craft (включая редактора), написал книги о характеристиках автомобилей Small Block Chevy и даже собрал впечатляющую коллекцию Chevelles 1965 и 1966 годов. Теперь он является постоянным автором OnAllCylinders. .20 способов решения проблемы загрязнения воды
Загрязнение воды происходит, когда в водоем попадают токсичные и вредные соединения. Этот водоем включает реку, океан или любой другой источник воды. Загрязнение воды — серьезная проблема, поскольку оно оказывает негативное воздействие как на людей, так и на окружающую среду. Это может вызвать болезнь и необратимое загрязнение источника чистой воды. В этой статье описаны 20 способов решения проблемы загрязнения воды. Эти решения могут помочь снизить интенсивность загрязнения воды.
Также прочтите:
1. Избегайте сброса отходов в реки
Эффективный способ решить проблему загрязнения воды — избегать сброса отходов в реки. Сюда входят как твердые, так и жидкие отходы. Отходы содержат много материалов с вредными химическими веществами, которые могут ухудшить качество воды в реке. Чем больше отходов в реках, тем токсичнее становится вода. Загрязнение продолжит распространяться на другие водоемы, когда люди по-прежнему сбрасывают отходы в реку.Когда сброс отходов прекратится, вода снова начнет постепенно улучшаться.
2. Используйте натуральные удобрения
Возможно, вам понадобится использовать удобрения или пестициды для сада дома. Но у этого есть и обратная сторона: эти вещи содержат токсичные химические вещества, которые могут попасть в источники воды. В конечном итоге вода может сильно загрязниться. Всегда лучше использовать натуральные удобрения или пестициды, которые можно купить у местных фермеров.Компостирование также может быть альтернативой химическим удобрениям, которые могут представлять меньшую угрозу для качества воды.
Также прочтите: Угрозы морским млекопитающим
3. Очистка рек
Реки могут быстро испачкаться, если люди продолжают сбрасывать в них отходы. Прежде чем весь мусор начнет скапливаться, рекомендуется начать очистку рек. Очистка рек может помочь увеличить количество токсичных веществ, отравляющих воду. Очистка может быть в форме непосредственного удаления отходов из воды.Еще один способ помочь в уборке — собрать малейший намек на мусор вокруг реки, прежде чем больше мусора скапливается и плавает в речной воде.
4. Избегайте слива масла в раковину
Выбрасывать любое масло в раковину — плохая идея. Большая часть накопления масла возникает в результате приготовления пищи. Может быть удобно просто смыть его водой в раковине, но это способствует загрязнению воды. Нефть в конечном итоге окажется в огромном водоеме и загрязнит его.Хороший способ избавиться от масла — собрать его в контейнере, а затем выбросить в мусор.
Подробнее:
5. Сократите использование машин, которым требуется вода
Многим нашим бытовым приборам для работы требуется вода. Примерами таких приборов являются посудомоечная машина, а также стиральная машина. Обе эти машины нуждаются в большом количестве воды для работы. Лучше всего сократить использование этих машин. Способ сделать это — заставить их работать только при полной загрузке.Это уменьшит частое использование машин. Это также означает, что меньше воды будет загрязнено мылом, которое в конечном итоге будет стекать в реки.
6. Используйте экологически чистые моющие жидкости или порошки
Большинство моющих жидкостей или порошков содержат химические вещества, токсичные для воды. Когда они слишком часто используются, они могут привести к еще большему загрязнению воды. Способ решить эту проблему — использовать экологически чистые моющие жидкости или воду. Начните использовать более экологичное мыло для стирки.Они могут стоить дороже, но они не вредят окружающей среде.
Также прочтите: Разлагатели океана
7. Используйте меньше мыла для стирки
Поскольку мы уже знаем, что мыло для стирки превращает чистую воду в грязную, лучше использовать только то количество мыла, которое уже рекомендовано. по направлениям. Старайтесь не использовать больше, чем предполагается, чтобы уменьшить количество нечистой воды. Это также может помочь уменьшить количество загрязненной воды, которую необходимо использовать для лечения.
8. Используйте меньше пластика
Пластик разлагается десятилетиями. К сожалению, это один из наиболее часто используемых материалов во многих предметах домашнего обихода. После того, как пластик выброшен, большая его часть оказывается где-то в воде. Когда пластик начинает разлагаться, в воду попадают вредные и токсичные химические вещества. Вода начинает загрязняться. Использование меньшего количества пластика может уменьшить количество пластиковых отходов в воде. Это означает более чистую и здоровую воду.
Подробнее:
9. Избегайте выбрасывать предметы в туалеты
Туалетную бумагу можно выбрасывать в туалете, поскольку она изготовлена из материалов, которые могут безопасно распадаться при контакте с водой. Чего следует избегать, так это выбрасывать такие предметы, как лекарства, такие как таблетки. Хотя они могут казаться маленькими, химические вещества могут растворяться в воде. Неиспользованные лекарства лучше всего выбросить в специальный мусор.
10. Техническое обслуживание автомобиля
Забота о вашем личном автомобиле — важный аспект уменьшения загрязнения воды.Вода — это элемент, на который влияет состояние воздуха в окружающей среде. Когда автомобиль не проверяется регулярно, высока вероятность того, что он будет выделять больше вредного газа. Газ выйдет в воздух. Воздух загрязняется, и это влияет на общее качество воды вокруг него.
Также прочтите: Влияние океанских течений на климат
11. Увеличение количества растений вокруг дома
Посадка большого количества растений или деревьев вокруг дома — это способ помочь решить проблему загрязнения воды.Чем больше они будут выращиваться, тем лучше. Деревья и другие растения могут помочь в фильтрации воды под землей. Более того, если в воде, текущей вокруг дома, присутствует вредная жидкость, эти деревья и растения могут помочь остановить сток жидкости в близлежащие источники чистой воды.
12. Уборка района
Иногда мусор или мусор может скапливаться вокруг домов или окрестностей. Если мусор не выбросить должным образом, он может вызвать распространение вредных химических веществ в источники чистой воды.Например, когда идет дождь, вода уносит разлагающиеся материалы, которые могут попасть в реки. Чтобы этого не произошло, нужно регулярно убирать окрестности. Убедитесь, что вокруг нет мусора, который может превратиться в вредный мусор.
Подробнее:
13. Обучайте друзей и членов семьи
Еще один хороший шаг к устранению загрязнения воды — повышение осведомленности. Начните рассказывать друзьям, членам семьи или кому-либо еще о важности качества воды.Расскажите им, как загрязнение воды может оказать долгосрочное негативное воздействие на людей, а также на окружающую среду. Когда все больше людей начнут беспокоиться об этой проблеме, можно будет внести большой вклад в поддержание чистоты воды.
14. Взаимодействуйте с организациями
Начните сотрудничать с организациями по вопросам благополучия окружающей среды. Организации не обязательно уделять особое внимание качеству воды. Это может быть организация, которая занимается переработкой или другими видами обращения с отходами.В конце концов, огромная причина загрязнения воды — плохое управление отходами. Когда вы работаете в организации, вы можете достичь большего с участием многих людей с одной и той же миссией.
Также прочтите: Виды китов, находящиеся под угрозой исчезновения
15. Требуйте более эффективного регулирования от правительства
Правительство имеет больше полномочий, когда дело доходит до принятия нормативных актов. Подайте петицию или потребуйте от правительства большего внимания к лучшему регулированию качества воды.Когда вмешается правительство, могут быть созданы новые или более строгие правила для поддержания хорошего качества воды.
Подробнее:
Другие способы решения проблемы загрязнения воды (16-20)
Вот список других способов решения проблемы загрязнения воды, которые также важны:
- Повторное использование пластика: Помимо сокращения использования пластик, повторное использование пластиковых предметов, которые были куплены, может во многом помочь решить проблему загрязнения воды. При повторном использовании меньшее количество пластиковых изделий попадет в реки.
- Очистка септика: Септик следует регулярно чистить или обслуживать во избежание утечки. Утечка приведет к загрязнению близлежащего источника воды отходами жизнедеятельности человека.
- Лучшее управление отходами в промышленности: Требование улучшенного управления отходами в промышленности может помочь снизить загрязнение воды. Некоторые отрасли промышленности позволяют своим химическим веществам попадать прямо в реки. Им необходимо уменьшить количество токсичных стоков, которые они вызывают.
- Утилизируйте автомобильное масло отдельно: Выполняя техническое обслуживание автомобиля в домашних условиях, обязательно выбрасывайте автомобильное масло или жидкость в специальный мусор.Не позволяйте маслу стекать в сточные канавы или землю.
- Не мусорить на пляже: Не мусорить на пляже. Носите с собой любые отходы и выбрасывайте их, как только найдете мусорный бак. Засорение приведет к скоплению мусора в океане. Океан — это самый большой водоем в мире, который никогда не должен загрязняться.
Узнайте больше:
Эти 20 способов решения проблемы загрязнения воды никогда не сработают, если люди не осознают, насколько серьезна эта проблема.Люди должны понимать, что каждый день мы вносим огромный вклад в загрязнение воды, и это нужно остановить. Эти решения не будут эффективными, если люди не начнут действовать. Малейшее действие может помочь решить проблему загрязнения воды.
.